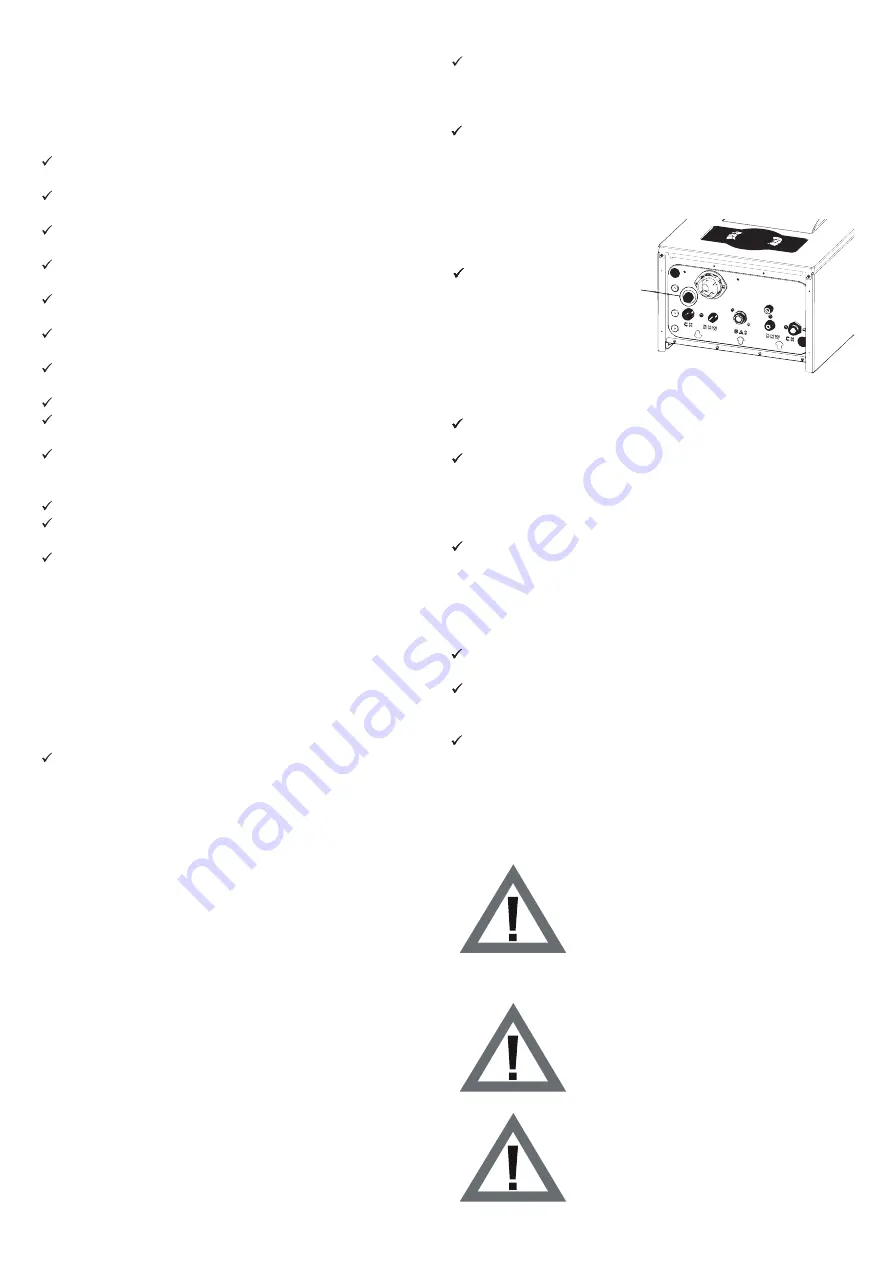
1-SAFETY RULES AND WARNINGS
1.1
.
Safety Instructions
When a gas leak is found or suspected;
Turn off the gas valve of the boiler and the valves of all
other devices operating with gas.
Shut off the stove, oven and similar appliances to put
their flame out.
Do not light matches, lighter etc, and stub out your
cigarette.
Ventilate the environment by opening doors and
windows.
Do not ever touch the buttons and plugs of your
electrical appliances.
Turn off the gas valves in the apartment and building
entrance.
Do not use the phones at places where the gas leak is
suspected.
Call your gas safe engineer as soon as possible.
Do not place and use flammable and explosive liquid or
materials around the boiler.
Keep materials such as water, foam away from
electrical connections during operations such as
cleaning, gas leak test etc.
The boiler must be installed in indoor spaces under normal
conditions. However, it can be operated in a suitable cabinet
in places such as garage, open balcony. Please consult
E.C.A for proper cabine sizes.
Do not lay the LPG container down
Do not block air vents, openings made in the walls of
the room which provide fresh air to the installation room.
Telephone number of the
National Gas
Emergency Service 0800 111 999
1
.2
.
Water Systems & Gas Supply Line
9
Before installation of the boiler, the water systems
(CH & DHW circuit) and gas supply line must be
completed in accordance with the relevant regulations and
standards by installer.
9
Installation for gas supply pipes must be fitted
according to BS6891 for GB and I.S.813.2002 for IE.
Install the connection pipes such that they are free from
mechanical stress.
1
.3
.
Gas Type Conversion
9
The standard gas type of boiler is Natural Gas. In
case of a demanding gas type conversion, this is
made
with charge.
9
Gas type conversion must be performed by the gas
safe engineer. Gas leak test must be made after
the
conversion operation.
9
Gas conversion label that indicates boiler is converted
from NG to LPG must be placed on the boiler
after gas
type conversion.
1
.4
.
Installation
9
The boiler must be installed in accordance with national
and local requirements, gas safety regulations,
relevant
standarts and this manual by gas safe engineer.
9
The boiler must be mounted against a closed wall.
9
The boiler can not be positioned having direct contact
to steam, detergent or gases.
9
Any change of flue position must not be made without
consulting gas safe engineer.
9
Sunlight can cause color change on the exterior of your
boiler over time.
CAUTION:
This boiler is not intended for
use by persons (including children) who
are low physical or sensory and mental
capacity and inexperienced persons
without informing and supervising the use
of the boiler by responsible persons.
Ensure that children under 8 years do not
play with the boiler.
CAUTION:
If boiler
is used incorrectly or
for other than its intended use, it may
present a life hazard and may cause
material damage to the product and its
surroundings.
CAUTION:
The
boiler
must be
transported and lifted by at least 2
people due to heavy weight.
If boiler is located in an unheated area, it must be
connected to mains, switched on, and pressure of
installation should be within operation range so that freeze
protection would be activated. Even if boiler is OFF position,
freeze protection stays activated.
Connecting the drain
pipework for the expansion
relief val
ve
1.5. Boiler Start Up
Boiler start up must be performed certainly by gas safe
engineer.
Gas Type (Natural Gas / LPG), gas supply pressure
(mbar), maximum DHW operating water pressure (bar) and
electricity supply voltage on the information plate must be
suitable with mains supply conditions. This is checked by
gas safe engineer.
After boiler start up, you should request information about
operating the boiler and safety precautions from gas safe
engineer.
1.6. Usage and Maintenance
Read carefully instructions and precautions in this manual
against wrong usage which causes unsafe conditions.
The boiler should be checked and serviced for general
maintenance once a year. Maintenance and service
operations must be carried out only gas safe engineer.
Only a damp cloth should be used for cleaning the outer
surface of the boiler and then the surfaces should be dried
completely. Do not use chemical substances or solutions
which cause rust and scratches in your boiler.
4