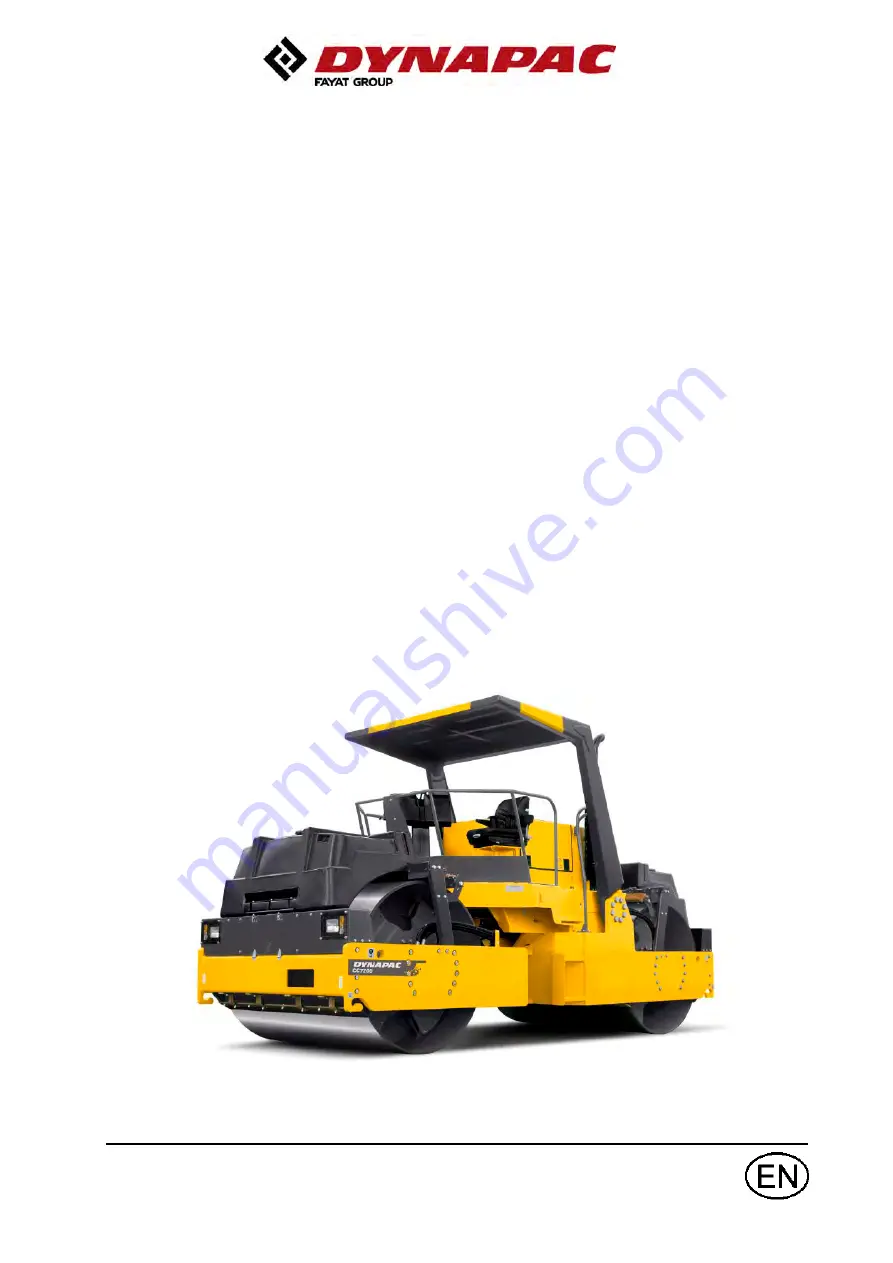
Instruction manual
Instruction manual
Operating & Maintenance
Operating & Maintenance
4812158801_E.pdf
4812158801_E.pdf
Vibratory roller
Vibratory roller
CC722/7200
CC722/7200
Engine
Engine
Cummins QSB 6.7 C (IIIB/T4i)
Cummins QSB 6.7 C (IIIB/T4i)
Serial number
Serial number
10000326xxA007761 -
10000326xxA007761 -
10000361xxA014104 -
10000361xxA014104 -
Translation of original instruction
Translation of original instruction
Reservation for changes
Reservation for changes
Printed in Sweden
Printed in Sweden
Summary of Contents for CC7200
Page 2: ......
Page 12: ...Introduction 4812158801_E pdf 2018 04 03 4...
Page 18: ...Safety Optional 4812158801_E pdf 2018 04 03 10...
Page 22: ...Special instructions 4812158801_E pdf 2018 04 03 14...
Page 66: ...Operating instructions Summary 4812158801_E pdf 2018 04 03 58...
Page 68: ...Preventive maintenance 4812158801_E pdf 2018 04 03 60...
Page 76: ...Maintenance Maintenance schedule 4812158801_E pdf 2018 04 03 68...
Page 88: ...Maintenance 50h 4812158801_E pdf 2018 04 03 80...
Page 101: ...Dynapac Compaction Equipment AB Box 504 SE 371 23 Karlskrona Sweden www dynapac com...