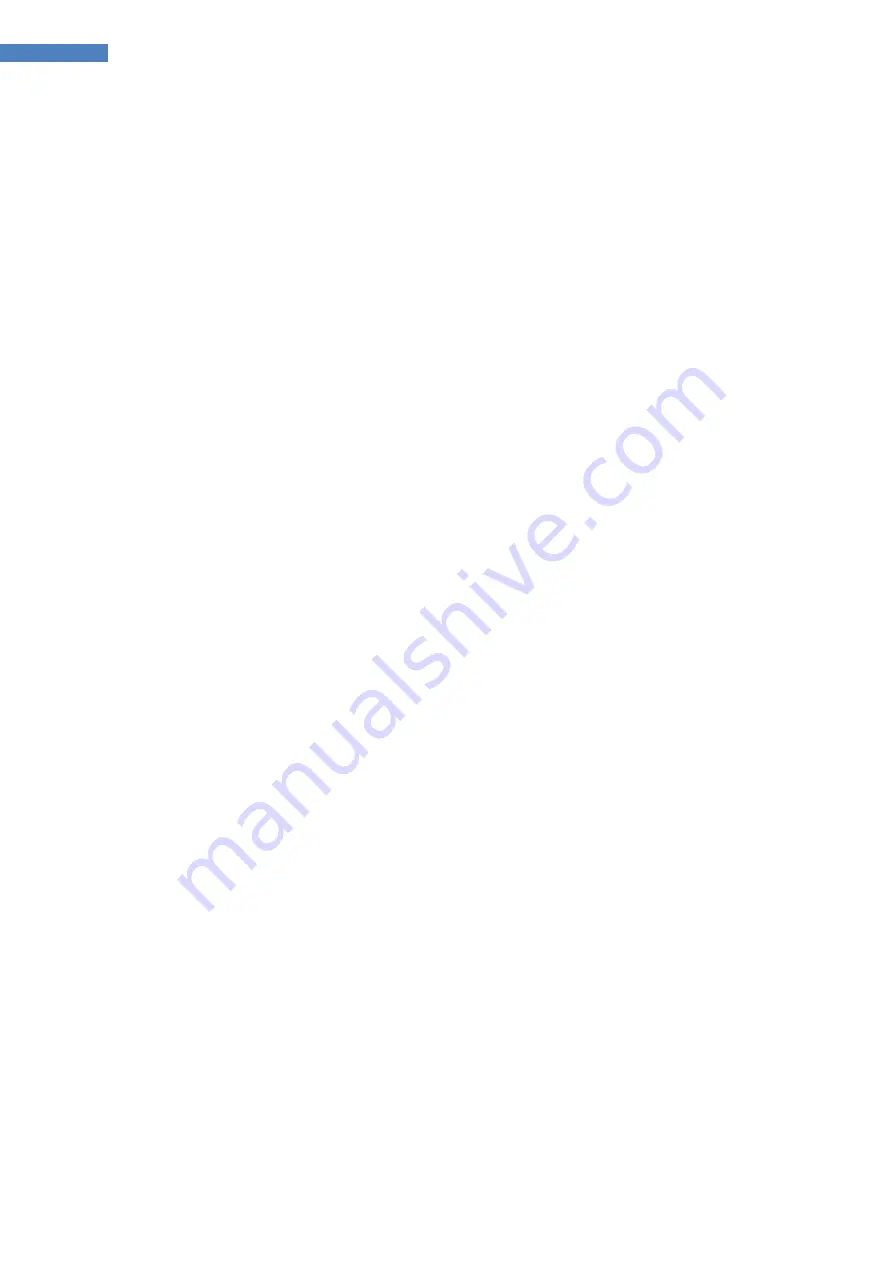
14
Dymax BlueWave® LED VisiCure® User Guide
Pin 3
–
Shutter In:
This signal line may be used to remotely activate the BlueWave LED VisiCure. When it
is being used, the local footswitch on the rear of the BlueWave LED VisiCure box is still capable of
operating the unit. Similar to the footswitch, if the timer/manual selector switch is in Timer Mode, the unit
will power the LED for the time set on the timer. In the Manual Mode, the unit will power the LED for the
duration of the remote activate signal.
Pin 4
–
Safety Interlock In:
A safety interlock can be connected between Pins 1 and 4. While +24V is
applied to Pin 4, the system will allow activation of the LED. If the connection is broken, power is
immediately removed from the LED. The safety interlock relies on the +24V signal being present on Pin 1.
In addition to removing power from the LED, if the system is being operated in the TIMED mode, breaking
this connection will reset the timer to zero. A second “shutter” signal will reactivate the LED for the timed
duration.
Pin 5
–
Intensity In (PWM):
This input is supplied as a means to actively control the output intensity of
the BlueWave LED VisiCure unit. It can be used to Pulse Width Modulate (PWM) the power to the LED.
This input cannot increase the intensity over the set point of the front panel intensity adjustment, but can
only reduce it. The front panel adjustment should be set fully clockwise to give Pin 5 the greatest range.
A high level (+24V) on Pin 5 will turn off the LED and a low level (0V) will allow maximum LED intensity. A
signal of 1.K Hz should be used with a duty cycle of 0 to 60%.
NOTE: A 10% duty cycle will generate a greater intensity than a 50% duty cycle.
This input can be used with an external controller to create any number of customized step-cure profiles
or with an additional sensor to regulate the output.
Output Signals
The output signals are all opto-isolated signals. Each signal has an NPN output transistor. The emitters of
all output transistors are tied together and connected to the PLC common on DB9 Pin 2. Each individual
output signal line is connected to the collector of each transistor. When the transistor is turned on, this
provides a ground to the PLC system that can be used to enable a relay coil signal to an opto-coupler. The
conducting transistor can also function as a set of contacts that can initiate actions within the PLC. When
the transistor is on, the signal is said to be “enabled” or “asserted”. When the transistor is off, the signal is
said to be “disabled” or “unasserted”. The transistors have a max current rating of 30 mA, and a max
power rating of
150 mW. Only positive voltages with respect to the PLC common should be used to a maximum of 24 Volts
DC. Series-limiting resistors should be used to ensure that the max conditions are not exceeded.
Pin 6
–
Lightguide Engaged Out:
When a lightguide is fully inserted into the unit, an internal switch will
allow the LED to operate. The same switch will send a signal to turn on the transistor and connect Pin 6 to
Pin 2. This output can be used to verify the condition of the system, should an error occur, or alert a user
to the failure.
Pin 7
–
LED Powered Out:
Pin 7 will be shorted to Pin 2 when the LED power supply is powered up and
the set point is above a predetermined level. Pin 7 will be open with respect to Pin 2, if the LED power
supply is off for any reason. This output can be used as go/no go confirmation that the array power supply
is engaged. Note: Verification of LED illumination should be made visually to ensure proper operation.
Pin 8
–
Intensity Out (PWM):
An internal circuit monitors the current sent to the LED, and generates a
PWM signal whose frequency and duty cycle varies with the current. Adjusting the front panel Intensity
Adjustment Screw, or using the Intensity Input on Pin 5, will cause a change in the signal seen on Pin 8.