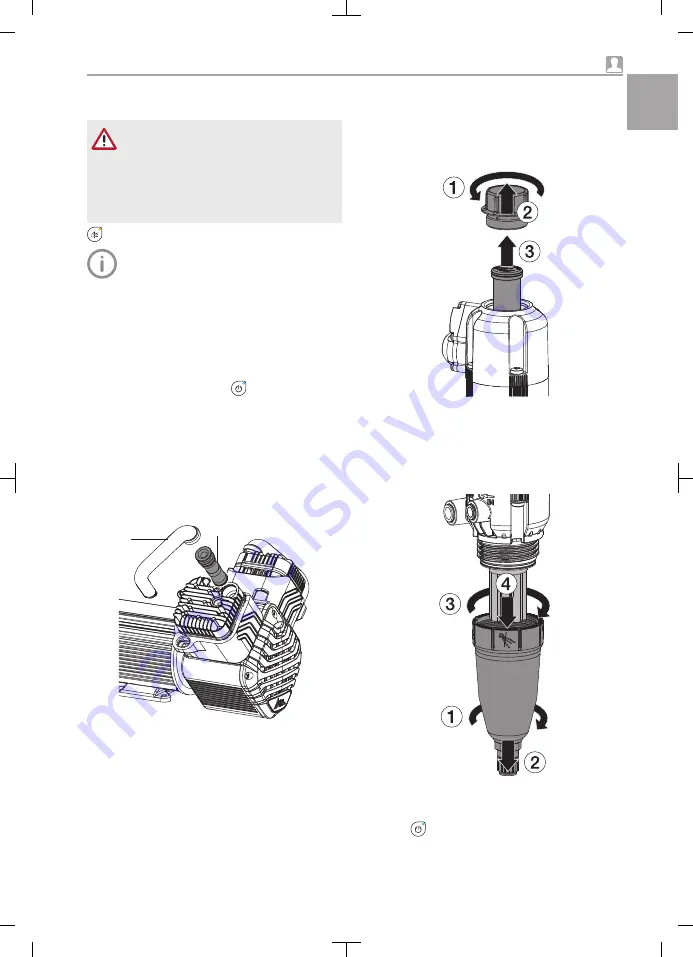
14.3 Changing the filter
NOTICE
Shortened service life, bad air quality,
reduced delivery
❯
As soon as the LED on the filter
replacement button lights up, replace
the filter.
Filter replacement button, LED lights up.
As soon as the LED lights up, it can be
temporarily switched off by pressing the
button. Every time the unit is switched
back on the LED comes on again.
The LED only goes out permanently once
replacement of the filter has been con-
firmed in set-up mode.
Disconnecting the unit from the mains
❯
Press the standby button
for at least 2 sec-
onds.
❯
Unplug the mains plug.
Replacing the air intake filter
❯
Pull off the noise reducer from the filter.
❯
Remove the filter.
❯
Insert a new filter.
❯
Push on the noise reducer onto the filter.
1
2
1
Noise reducer
2
Filters
Replacing the fine or virus bacteria filter
❯
Unscrew and remove the filter cover.
❯
Remove the filter.
❯
Insert a new filter.
❯
Replace the filter cover and close.
Sintered or coalescence filter
❯
Unscrew and remove the filter housing.
❯
Remove the filter.
❯
Insert a new filter.
❯
Replace the filter housing and close.
Confirming the filter replacement
❯
Connect the mains plug.
❯
Press
for at least 2 seconds.
Usage
4252100034L02 2105V002
35
EN