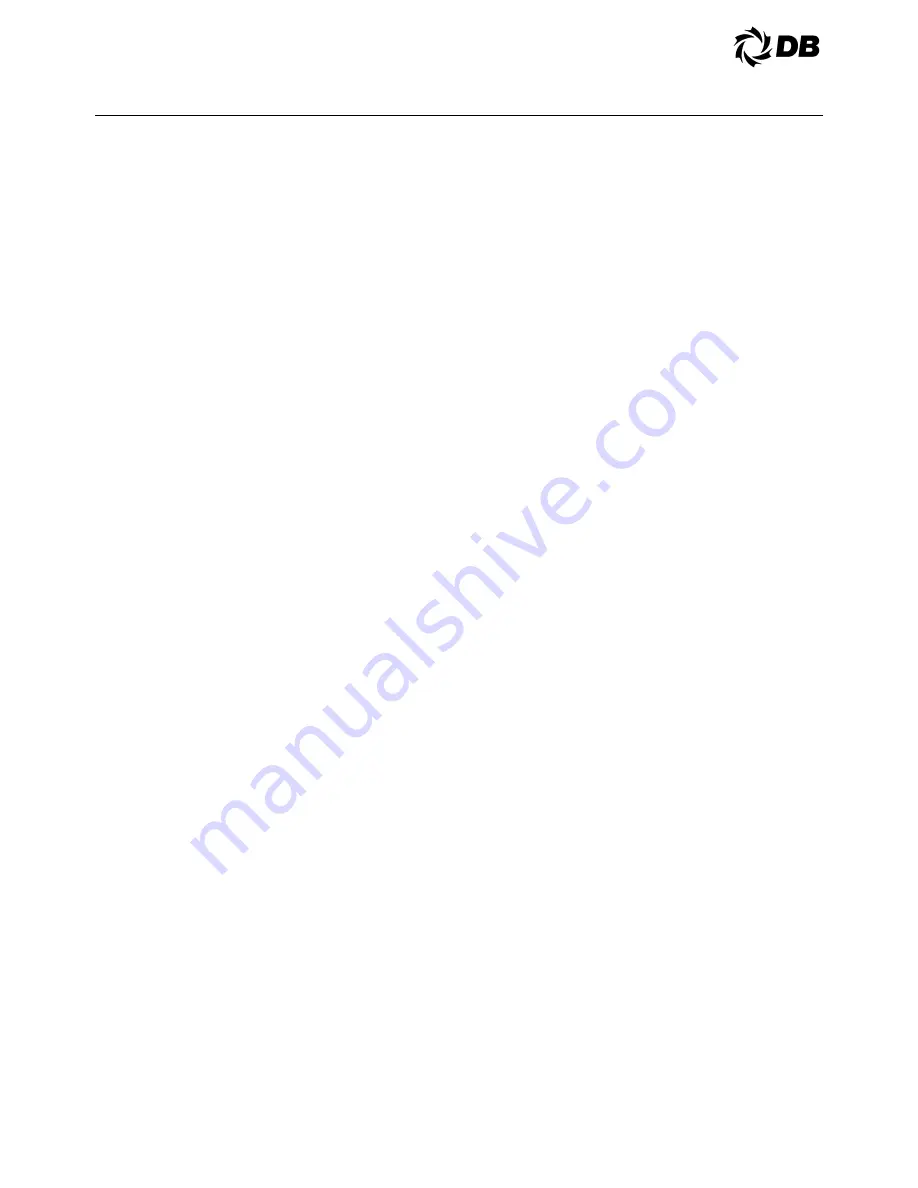
- 35 -
GUIDE SPECIFICATIONS
5. Evaporator and condenser vessels shall all be
cleanable shell and tube type with integral finned
copper water tubes mechanically expanded into heavy
fixed steel tube sheets. They are to be available in
one, two or three pass design as required on the
drawings with Victaulic connections. The shell side of
the evaporator and condensers shall have pressure
relief valve with provision for refrigerant venting.
Evaporators and condensers shall be designed,
constructed in accordance with the ASME Code for
Unfired Pressure Vessels. The condenser shall be
sized for full pump down capacity. The flooded
evaporator shall have a built in distributor for feeding
refrigerant evenly under the tube bundle to produce a
uniform boiling action and baffle plates shall be
provided to ensure vapor separation. Water heads are
to be removable for tube cleaning. Vent and drain
plugs are to be provided in each head. (All low
temperature surfaces shall be factory insulated.)
(Provide a dual bundle on condenser for heat
reclaim.)
6. The flooded evaporator shall be fitted with an oil
recovery system. The oil recovery system will insure
that the evaporator is operating at peak efficiency at
all times and provide optimal energy efficiency during
extended periods of part load. Units without oil
recovery systems mounted on the evaporator will not
be acceptable.
7. To maximize energy efficiency, the packaged chiller
shall be equipped with a economizer and modulating
refrigerant expansion devices. Refrigerant vapor from
the economizer shall be fed back into an intermediate
compressor stage, reducing the enthalpy of the
refrigerant and increasing the net refrigeration effect
of the evaporator.
8. The packaged chiller shall be furnished with a
modulating refrigerant control system to optimize
efficiency and compressor protection. This refrigerant
control system will reduce the flow of efficiency
robbing refrigerant vapor in the condenser from
entering the evaporator at reduced load by directly
modulating a motorized refrigerant valve in the liquid
line entering the evaporator. In addition, the
refrigerant control system shall measure the level of
liquid refrigerant in the flooded evaporator and restrict
refrigerant flow entering the evaporator upon a rise in
the level, protecting the compressor from slugging
liquid refrigerant. Fixed orifice control systems will not
be acceptable. (Hot gas bypass shall be factory
installed for operation down to approximately 10% of
full load.)
9. The packaged chiller shall be equipped with controller
control. The control shall provide for compressor
loading based on leaving chilled water temperature. It
shall provide for high and low refrigerant pressure
protection, low oil level protection, evaporator water
freeze protection, sensor error protection, and motor
load control (demand limiter) based on amp draw.
Anti-recycle protection shall also be provided. The
computer shall have a simple keyboard accessed
input system and be complete with 320x240 pixel, 256
color display. Input shall be accomplished through
simple menu driven display screens, with on-line help
available by pressing a help button at anytime during
operation. The controller shall continuously monitor
evaporator leaving water temperature; evaporator and
condenser pressure; compressor amp draw; and
refrigerant. The computer shall be complete with all
hardware and software necessary to enable remote
monitoring of all data through the addition of only a
simple, phone modem and terminal. The controller
shall be completed with an RS232 "local"
communications port and an RS485 long distance
differential communications port. The controller shall
also accept a remote start and stop signal, 0 to 5VDC
chilled water temperature reset signal and (0 to 5VDC
compressor current limit reset signal). Terminal or PC
with communication software installed to enable
remote monitoring.
10. The electrical control panel shall be wired to permit
fully automatic operation during - initial start-up,
normal operation, and shutdown conditions. The
control system shall contain the following control and
safety devices:
MANUAL CONTROLS
D
Control circuit stop and start switches
D
Compressor enable switch
SAFETY CONTROLS
D
Solid state compressor motor starter overloads (3
phase)
D
Low oil level optical sensor
D
High condenser pressure
D
Low evaporator pressure
D
Freeze protection
D
Chilled water flow loss
D
Under voltage phase failure relay
AUTOMATIC CONTROLS
D
Compressor motor increment contactors
D
Increment start timer
D
Anti-recycle timer
D
Oil sump heater interlock relays
REFRIGERANT CONTROLS
D
Motorized refrigerant flow control
D
Liquid refrigerant level sensor for evaporator
D
Compressor load and unload solenoid valves
INDICATOR LIGHTS
D
Power on
D
Compressor high oil temperature
D
Compressor motor overload
D
System common alarm
11. The control system shall be provided with an anti-
recycle device. The control shall limit compressor
starting to a minimum of 15 minutes between starts.
12.
The packaged chiller shall be furnished with unit
mounted reduced inrush starting system for each
compressor. The starters shall be factory mounted
and wired, with individual circuit breakers on multiple
compressor units. The unit shall be wired so that the
only field electrical connection to the packaged chiller
shall be to a single three-phase power terminal.
Optional items in ( )
Summary of Contents for WCFX-E Series
Page 27: ...27 TYPICAL WIRING SCHEMATIC Two Compressors Unit...
Page 28: ...28 TYPICAL WIRING SCHEMATIC...
Page 29: ...29 TYPICAL WIRING SCHEMATIC...
Page 30: ...30 TYPICAL WIRING SCHEMATIC...
Page 31: ...31 TYPICAL WIRING SCHEMATIC...
Page 36: ......