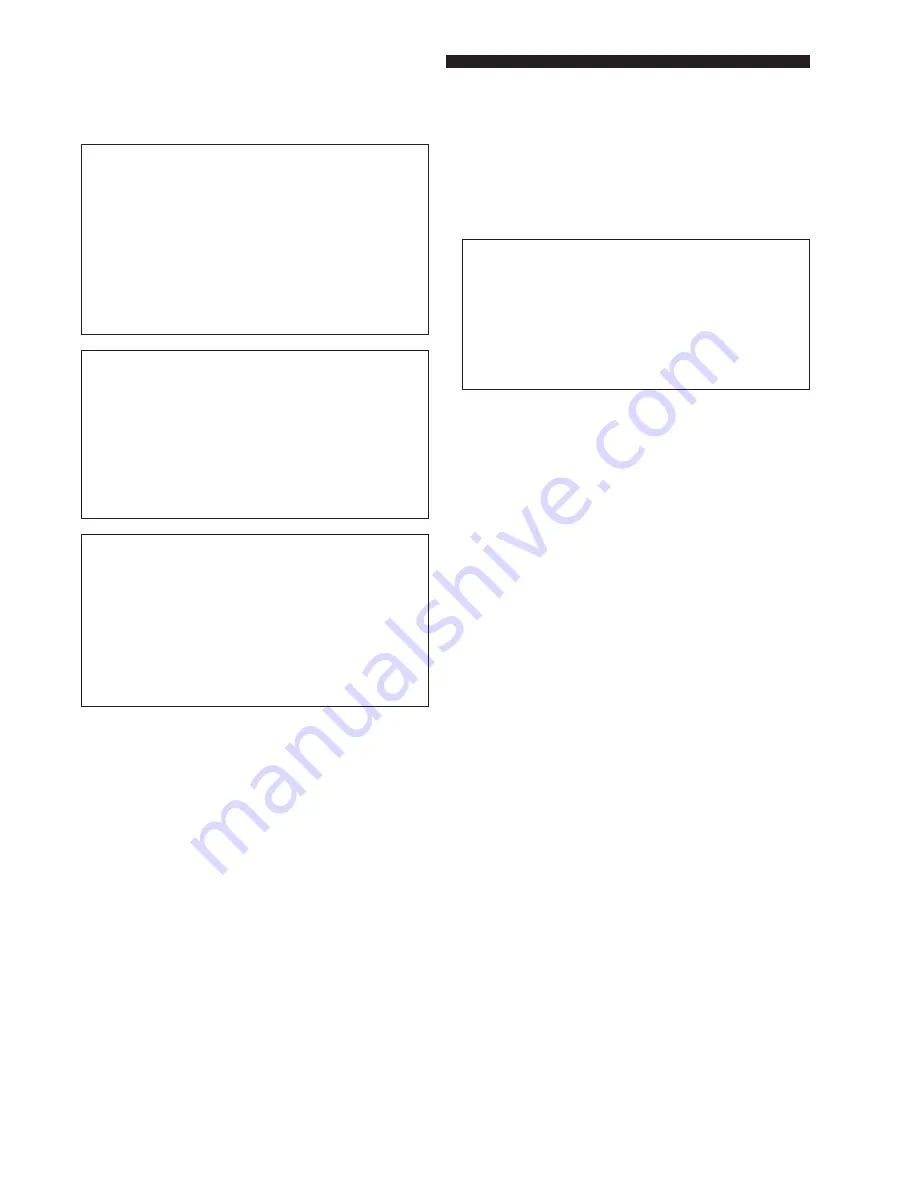
Service Manual for Speed Oven Model DSO 500
50
HIGH VOLTAGE RECTIFIER TEST
WARNING
THE HIGH VOLTAGES AND CURRENTS AT
THE HIGH VOLTAGE RECTIFIER ARE EX-
TREMELY DANGEROUS. NEVER MAKE ANY
DIRECT VOLTAGE MEASUREMENTS AT
THE HIGH VOLTAGE RECTIFIER CIRCUIT.
IT IS VERY DANGEROUS TO WORK NEAR
THIS PART WHEN THE OVEN IS ON.
WARNING
THE HIGH VOLTAGE RECTIFIER HAS HIGH
VOLTAGES PRESENT AT ALL TIMES EVEN
IF THE OVEN IS NOT OPERATING. BE SURE
THE OVEN IS ISOLATED BEFORE TESTING.
REFER TO THE SAFETY PRECAUTIONS AT
THE FRONT OF THIS MANUAL.
WARNING
THE HIGH VOLTAGE CAPACITOR RETAINS
THE 2.5 kVDC CHARGE EVEN AFTER THE
OVEN IS DISCONNECTED. THIS CAPACI-
TOR MUST BE DISCHARGED BEFORE
WORKING ON ANY COMPONENTS IN THE
HIGH VOLTAGE AREA.
Tools required
• Digital Multimeter
• Megohmmeter
Test Procedure
1. Disconnect the oven from the power
source.
2. Remove top cover and right side panel to
access the high voltage diodes (rectifiers).
WARNING
HIGH VOLTAGE CAPACITOR MUST BE
DISCHARGED BEFORE PERFORMING THIS
PROCEDURE. WAIT AT LEAST FIVE (5)
MINUTES AFTER SHUTDOWN OF HIGH
VOLTAGE SYSTEM.
3. Discharge the high voltage capacitor as
described in the paragraph DISCHARGING
THE HIGH VOLTAGE SYSTEM ON THE
DUKE SPEED OVEN.
4. Ensure that the High Voltage Capacitor is fully
discharged before commencing work.
5. Remove all connections from the High Volt-
age rectifier.
6. Using a megohmmeter, test for continuity
between rectifier terminals. Reverse mego-
hmmeter leads and check again. Check for
the following results:
a. Short circuit in both directions:
Replace rectifier
b. Open circuit in both direction:
Replace Rectifier
c. Conducts one way and shows leakage
the other way:
Replace Rectifier
d. C o n d u c t s o n e d i r e c t i o n o n l y :
Rectifier is good.
Summary of Contents for DSO 500
Page 2: ...Service Manual for Speed Oven Model DSO 500 2 ...
Page 26: ...Service Manual for Speed Oven Model DSO 500 26 SOLID STATE RELAYS NOTES ...
Page 28: ...Service Manual for Speed Oven Model DSO 500 28 MECHANICAL RELAYS AND INTERLOCK SWITCHES NOTES ...
Page 32: ...Service Manual for Speed Oven Model DSO 500 32 LINE FUSES NOTES ...
Page 34: ...Service Manual for Speed Oven Model DSO 500 34 JET PLATES NOTES ...
Page 36: ...Service Manual for Speed Oven Model DSO 500 36 CABINET COOLING FANS NOTES ...
Page 40: ...Service Manual for Speed Oven Model DSO 500 40 COOLING FAN THERMAL SWITCH NOTES ...
Page 42: ...Service Manual for Speed Oven Model DSO 500 42 KEYPAD CONTROL BOARD NOTES ...
Page 44: ...Service Manual for Speed Oven Model DSO 500 44 INVERTERS NOTES ...
Page 52: ...Service Manual for Speed Oven Model DSO 500 52 COMPONENT TESTING NOTES ...
Page 57: ...57 REPAIR PROCEDURES ...