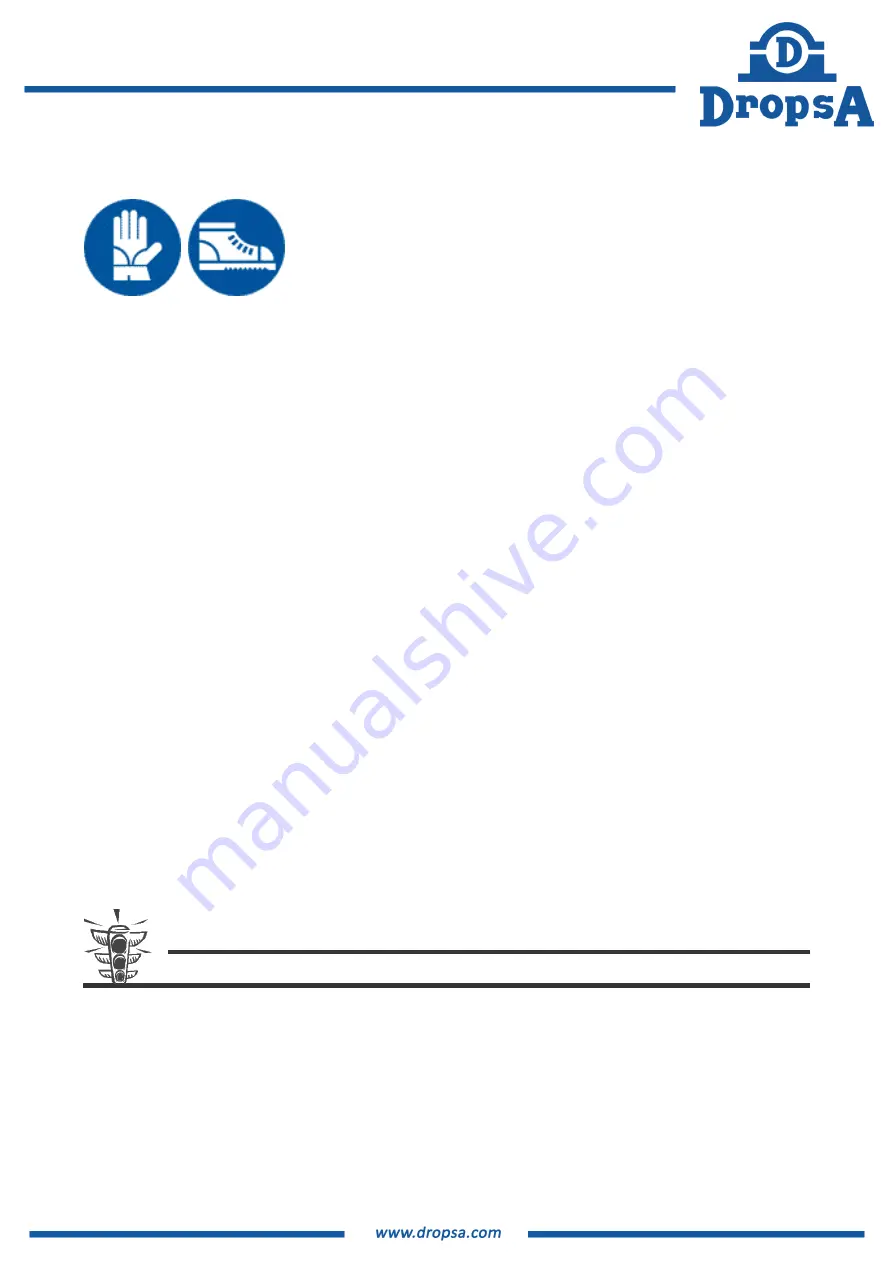
20
To carry out the task in question, the following Personal Protection Equipment is required:
4.2.1. Installation of the pump
To complete the task in question, carry out the following simple steps.
Position the pump and secure it to its support (on the wall or floor) by using the appropriate
Ø9mm eyelets, (0.354 in) with 4 suitable screws. The pump has limited dimensions and a
weight of 15 kg or 18 kg, depending on whether it is fitted respectively with a 5 kg or 10 kg
grease reservoir, to which the weight of the grease with a full reservoir must be summed.
Assemble the pump in such a way that the grease nipple for filling the reservoir is easily
accessible.
Leave at least 100mm (3.94 in) perimeter distance from other equipment or obstacles that
prevent access to the pump.
In the event of wall-mounted installation, mount the pump at “operator height” (about 1200
mm from the floor surface) to avoid abnormal posture or the possibility of impact.
Ensure that the pipes and wires have been properly fastened and protected from any possible
impact.
Verify that the grease used is fit for operating temperatures, especially at temperatures below
0° C. If in doubt, contact our Technical Office for the correct choice of lubricant.
4.2.2. Hydraulic connections
The plumbing connection point to install the pump to the system is located on the pumping body
with G1/4” thread for "Progressive" pumping elements and G1/8" for "Multi-line" pumping
elements. The possibility of having the return in pump with G1/8” thread is provided.
ATTENTION
:
the pipeline must reach the point of lubrication along the shortest route possible.
4.2.3. Electrical connection
The electrical connection is the responsibility of the user who must provide unequivocal
identification of the power supply connection and output signals.
Connect the machine to the electrical line as indicated in this manual.