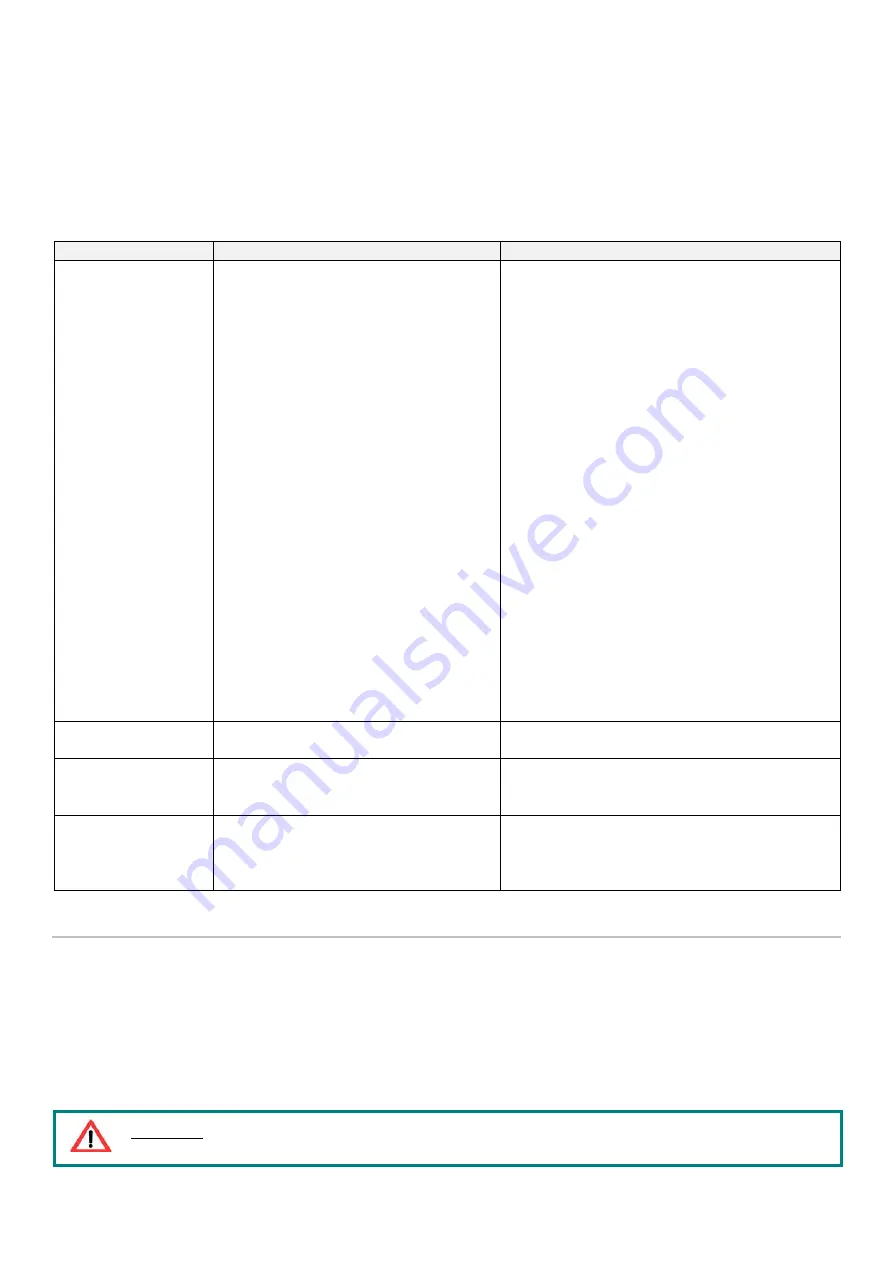
12
A diagnostics table is provided below that indicates the main anomalies, the probable causes and the possible solutions.
If you were not able to solve the problem after consulting the diagnostics table, do not try to find the fault by disassembling
machine parts but contact the Dropsa technical office and report the anomalies that have been discovered, with a detailed
description.
PROBLEM
CAUSE
SOLUTION
The electric pump does
not deliver lubricant.
The electric motor is not operating.
The tank is empty.
The pump does not prime. Cause for the
pump not priming:
•
The motor is rotating in the inverse
direction (clockwise);
•
The motor is rotating in the correct
direction, but the spatula is not rotating;
•
Air bubbles in the lubricant.
The pressure control valve (bypass) was
calibrated at a value that is too low
Presence of dirt in the non-return valve
Check the connection between the motor and the
electric power supply line.
Check the motor windings.
Check that the motor terminal board connection
plates have been positioned according to the power
supply voltage.
Fill the tank.
Attention: if the tank emptied itself and the electric
signal indicating that the minimum level was reached
was not given, check the minimum level contact.
Remove the tank cover and check that the spatula
rotates clockwise and moves the lubricant; otherwise,
invert two of the three motor phases.
See above.
Disconnect the pump delivery pipe and bleed the
lubricant until the air bubbles have been eliminated.
The pump does not
pressurise.
There may be dirt on the pumping element
check valve cone.
Clean the pumping element check valve cone and
seat, bleeding the lubricant.
No minimum level
signal when there is no
lubricant in the tank.
Minimum level incorrectly regulated.
Check the correct operation of the level probe as
follows:
Check the correct level adjustment of laser probe.
Minimum level
selection, with lubricant
below the minimum
and pump operating.
Minimum level incorrectly regulated.
The control panel lamp always remains on: check the
electric connection and replace the laser probe if
necessary.
9. MAINTENANCE PROCEDURES
The pump was designed and built in order to minimise maintenance requirements.
To simplify maintenance, it is recommended to install it in an easy to reach position.
•
Periodically check the pipe joints to detect any leaks. Furthermore, always keep the pump clean to be able to quickly detect
any leaks or defects.
•
Check if the loading filter is clean after every 2000 hours of operation.
The machine does not require any special equipment for any control and/or maintenance activity. It is recommended to use
tools and personal protective devices suitable for use (gloves) and that are in good condition according to current regulations to
prevent damage to people or machine parts.
ATTENTION
:
Make sure that the electric and hydraulic power supplies are disconnected before carrying out any
maintenance work.