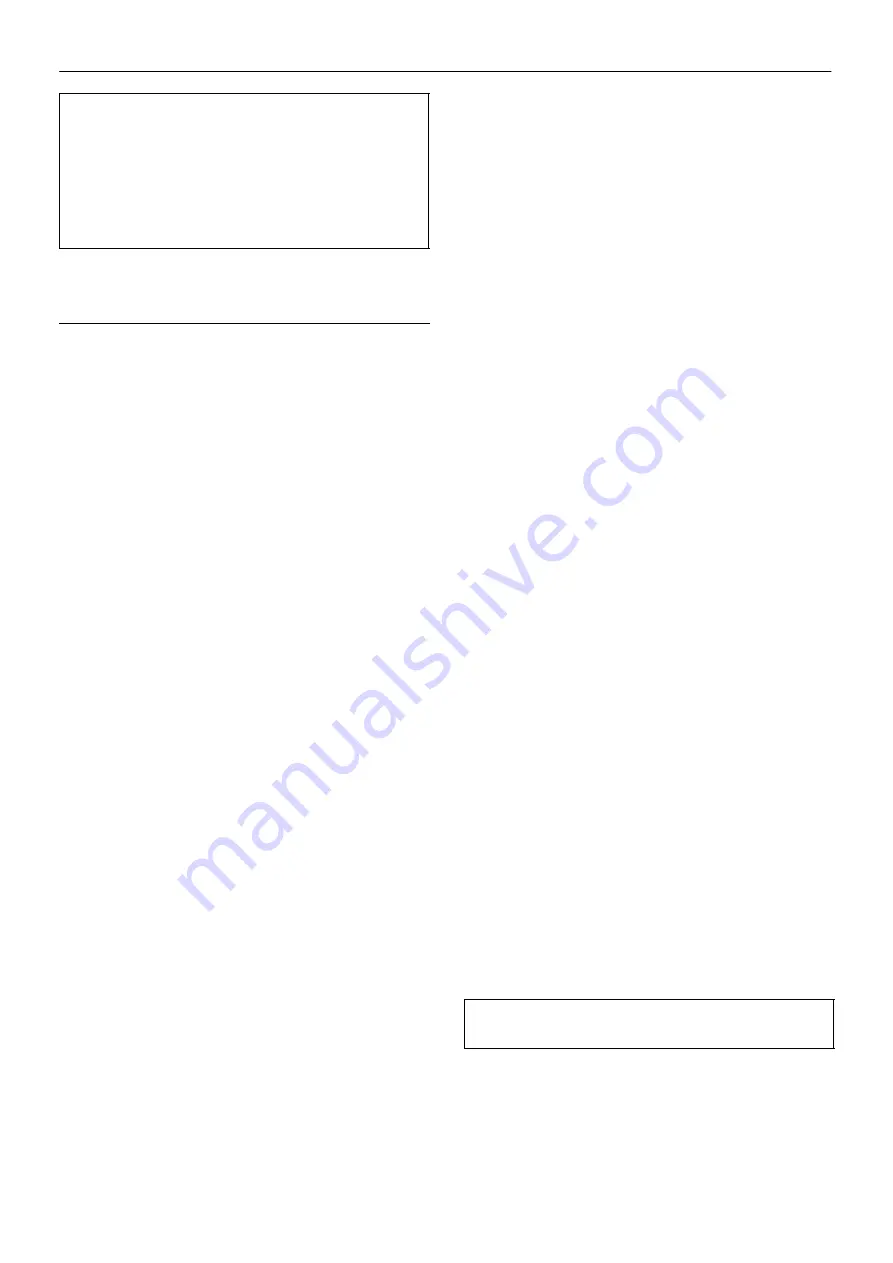
SAFETY
9
LIGHTSOURCE V9
WARNINGS
Warnings call attention to instructions which must be followed
precisely to avoid injury or death.
CAUTIONS
Cautions call attention to instructions which must be followed
precisely to avoid damaging the product, process or its surroundings.
NOTES
Notes are used for supplementary information.
General Information
Never operate unit without first observing all safety warnings and
carefully reading the operation and maintenance manual shipped from
the factory with this machine.
Ensure that the operator reads and
understands
the decals and
consults the manuals before maintenance or operation.
Ensure that the Operation and Maintenance manual, and the
manual holder, are not removed permanently from the machine.
Ensure that maintenance personnel are adequately trained,
competent and have read the Maintenance Manuals.
This machine is not designed for operating life sustaining
equipment. It is equipped with a safety shutdown system that will cause
the machine to stop operating whenever a shutdown condition is
present.
Hazards may exist on the jobsite should this unit shutdown
automatically and all lamps be extinguised. Personnel should be
advised of this and have additional lighting.
Hot Pressurized Fluid
−
Remove cap slowly to relieve PRESSURE
from HOT radiator. Protect skin and eyes. HOT water or steam and
chemical additives can cause serious personal injury.
Electrical shock hazard will cause severe injury or death. Do NOT
position light tower under electric power lines.
Improper operation of this machine can result in severe injury or
death.
Hazardous Voltage can cause serious injury or death.
Never inspect or service unit without first disconnecting battery
cable(s) to prevent accidental starting.
Wear eye protection while cleaning unit with compressed air, to
prevent debris from injuring eyes.
Do not enter ballast box while engine is running. Do not steam clean
ballast box. Capacitor/Ballast can cause severe injury.
Do not operate lights with broken or missing lens or broken glass
bulb. Ultra violet radiation can cause serious skin burn and eye
inflamation.
Do not place hand in tower recess while tower is being lowered or
raised. Pinch point can cause severe injury.
Ground equipment in accordance with applicable codes. (Consult
local electrician).
Do not operate electrical equipment while standing in water, on wet
ground, with wet hands or shoes.
Use extreme caution when working on electrical components.
Battery voltage (12V) is present unless the battery cables have been
disconnected. Higher voltage (potentially 500 volts) is present at all
times when the engine is running.
Always treat electrical circuits as if they were energized.
Before attempting any repair service, disconnect all leads to
electrical power loads.
Do NOT connect or disconnect lamps while engine is running.
Make sure that all protective covers are in place and that the
canopy/doors are closed during operation.
The specification of this machine is such that the machine is not
suitable for use in flammable gas risk areas. If such an application is
required then all local regulations, codes of practice and site rules must
be observed. To ensure that the machine can operate in a safe and
reliable manner, additional
equipment such as gas detection, exhaust
spark arrestors, and intake
(shut
−
off)
valves may be required,
dependant on local regulations or the degree of risk involved.
A weekly visual check must be made on all fasteners/fixing screws
securing mechanical parts. In particular, safety
−
related parts such as
coupling hitch, drawbar components, road
−
wheels, and lifting bail
should be checked for total security.
All components which are loose, damaged or unserviceable, must
be rectified without delay.
This machine produces loud noise with the doors open or service
valve vented. Extended exposure to loud noise can cause hearing loss.
Always wear hearing protection when doors are open or service valve
is vented.
Never inspect or service unit without first disconnecting battery
cable(s) to prevent accidental starting.
Do not use petroleum products (solvents or fuels) under high
pressure as this can penetrate the skin and result in serious illness.
wear eye protection while cleaning unit with compressed air to prevent
debris from injuring eye(s).
Rotating fan blade can cause serious injury. Do not operate without
guard in place.
Use care to avoid contacting hot surfaces (engine exhaust manifold
and piping, air receiver and air discharge piping, etc.).
WARNING: Under no circumstances should volatile liquids such
as Ether be used for starting this machine.
Never operate unit with guards, covers or screens removed. Keep
hands, hair, clothing, tools, blow gun tips, etc. well away from moving
parts.
Do not alter or modify this machine.
Summary of Contents for LIGHTSOURCE V9
Page 3: ......
Page 4: ......
Page 18: ...GENERAL INFORMATION 14 LIGHTSOURCE V9 FIXED HEIGHT RUNNING GEAR VARIABLE HEIGHT RUNNING GEAR...
Page 33: ...MAINTENANCE 29 LIGHTSOURCE V9...
Page 34: ...ELECTRICAL SYSTEM 30 LIGHTSOURCE V9 SCHEMATIC DIAGRAM FOR AC ELECTRICAL HARNESS...
Page 35: ...ELECTRICAL SYSTEM 31 LIGHTSOURCE V9 SCHEMATIC DIAGRAM FOR AC ELECTRICAL HARNESS...
Page 36: ...ELECTRICAL SYSTEM 32 LIGHTSOURCE V9 SCHEMATIC DIAGRAM FOR AC ELECTRICAL HARNESS...
Page 38: ...ELECTRICAL SYSTEM 34 LIGHTSOURCE V9 SCHEMATIC DIAGRAM FOR DC ELECTRICAL HARNESS...
Page 64: ......
Page 65: ......
Page 66: ......