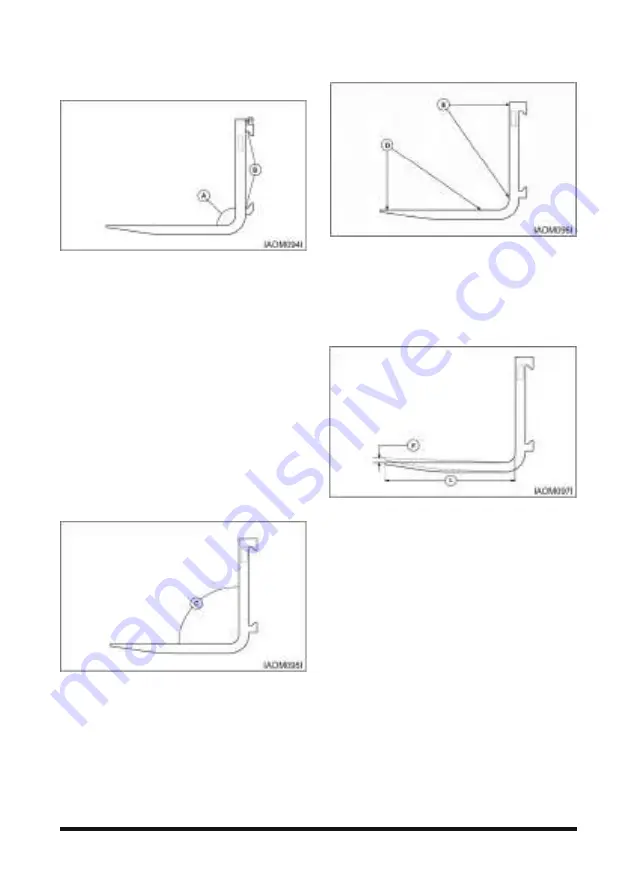
Maintenance Section
-147-
Fork – Inspect
Forks should be inspected, at a minimum, every 12
months. If the truck is being used in a multi-shift or
heavy duty operation, they should be checked every six
months.
1. Inspect the forks carefully for cracks. Special
attention should be given to the heel section (A), all
weld areas and mounting brackets (B). Inspect the
top and bottom hooks on forks used on hook type
carriages and tubes on shaft mounted forks.
Forks with cracks should be removed from service.
"Wet Test" magnetic particle inspection is generally
preferred due to its sensitivity and the ease of
interpreting the results. Portable equipment is
usually recommended so it can be moved to the lift
truck.
Inspectors should be trained and qualified in
accordance with The American Society for Non
Destructive Testing, Level II Qualifications.
2. Check the angle between the upper face of the
blade and the front face of the shank. The fork
should be withdrawn from service if angle (C)
exceeds 93 degrees or deviates by more than 3
degrees from an original angle other than 90
degrees, as may be found in some special
application forks.
3. Check the straightness of the upper face of blade
(D) and the front face of shank (E) with a straight
edge.
The fork should be withdrawn from service if the
deviation from straightness exceeds 0.5 percent of
the length of the blade and/or the height of the
shank respectively 5 mm/1000 mm (0.18"/36").
4. Check the difference in height of one fork tip to the
other when mounted on the fork carrier. A difference
in fork tip height can result in uneven support of the
load and cause problems with entering loads.
The maximum recommended difference in fork tip
elevation (F) is 6.5 mm (0.25") for pallet forks and 3
mm (0.125") for fully tapered forks. The maximum
allowable difference in fork tip elevation between the
two or more forks is 3 percent of blade length (L).
Replace one or both forks when the difference in
fork tip height exceeds the maximum allowable
difference. Contact your local DOOSAN Lift Truck
Dealer for further information.
https://www.forkliftpdfmanuals.com/