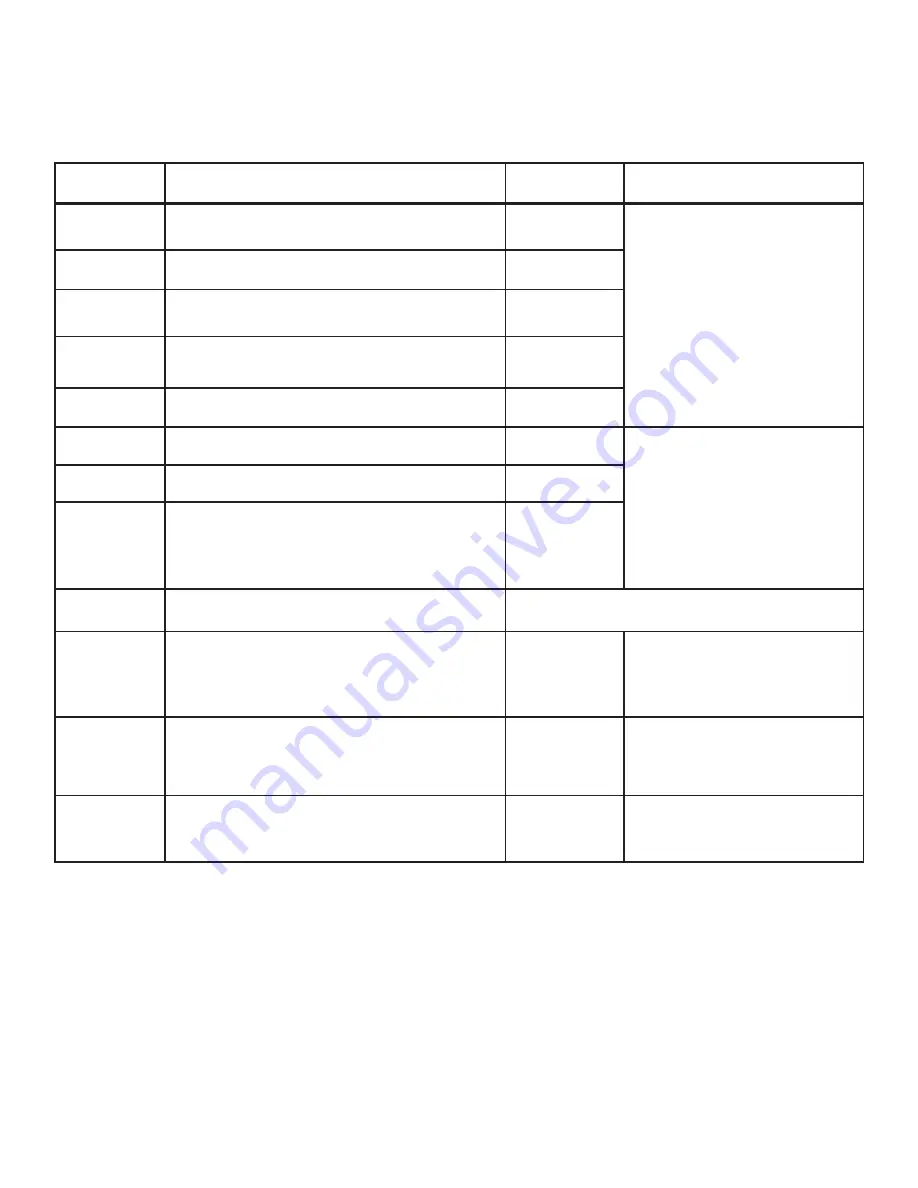
20
LUBRICATION
LUBRICATION CHART
LOCATION DESCRIPTION AND
SERVICE RECOMMENDATIONS
RECOMMENDED
LUBRICANT
LUBRICATION
INTERVAL*
LUBRICATION
POINT NO.
1
2
3
MONTHLY
WEEKLY
Insert Adjustment Screws.
Oil the threads.
INSERT CHANGE
Bandwheel Bearngs.
One (1) grease fitting each
bandwheel.
MONTHLY
MONTHLY
Head Carrage Lnear Bearng (Older machnes).
Four
(4) grease fittings.
Current machnes are sealed for lfe.
4
5
Head Pvot Pllow Blocks.
Two (2) grease fittings.
MONTHLY
6
Post.
Clean and apply oil.
7
MONTHLY
Mscellaneous: Vse Sldes, Hnges, Pvot Ponts,
Component Parts, Unpanted Surfaces, etc.
To ensure
function and maintain appearance while reducing wear,
corrosion, rust, etc. Apply when and where needed in
amounts required.
8
AS REQUIRED
High quality, rust and oxidation-inhibited,
medium hydraulic and general purpose
industrial oil.
ISO-VG Grade 68 (Formerly ASTM Grade
No. 315).
Union 76, UNAX RX 68, or equivalent.
Lubricate per manufacturer's recommendations.
9
Electrc/Hydraulc Motors.
Hydraulic Pump, Coolant,
Drive and Optional Chip Conveyor.
10
11
* Lubrcaton ntervals are based on a 8-hour day, 40-hour week.
Lubrcate more often wth heaver use.
Band Tenson Slde.
Clean and apply grease.
Vse Movable Jaw Sldes/Gbs.
Four (4) grease fittings.
1 for each gib. Add two (2) for
Optonal Outboard Vse
.
Premium quality, multi-purpose lithium-
base, EP (extreme pressure) grease.
NLGI No. 2.
Union 76, UNOBA EP 2, or equivalent.
12
Coolant Reservor (Drp Pan).
20 gallon (75.7 liter) capacity.
Chp Conveyor (Optonal).
50 gallon (189.2 liter) capacity.
Drain, clean and refill whenever coolant becomes
undesireable for further use. Clean the mesh strainer at the
same time.
Premium quality, saw band coolant and
lubricant.
DoALL cutting fluids and/or oils -
(Power-Cut).
CHECK DAILY/
AS REQUIRED
CHECK DAILY/
AS REQUIRED
Hydraulc Reservor.
20 gallon (75.7 liter) capacity.
Check oil level daily and keep the reservoir full. Drain,
change the filter element and refill after the 1st month;
every six (6) months thereafter.
Band Mst Lubrcator (Optonal).
Keep reservoir filled
and hoses clear.
Contact your DoALL sales representative
for the best oils and/or fluids for your
application.
DoALL cutting fluids and/or oils.
CHECK DAILY/
AS REQUIRED
Multi-purpose automatic transmission
fluid.
General Motors Dexron III, or equivalent.
Summary of Contents for TF-2025M
Page 1: ...TF 2025M Serial No 543 99101 to Band Sawing Machine Instruction Manual...
Page 5: ...MACHINE DIMENSIONS INCHES 03 MILLIMETERS 1 mm FLOOR PLAN...
Page 6: ...FRONT VIEW MACHINE DIMENSIONS Continued INCHES 03 MILLIMETERS 1 mm...
Page 7: ...MACHINE DIMENSIONS Continued SIDE VIEW INCHES 03 MILLIMETERS 1 mm...
Page 8: ...MACHINE FEATURES SIDE VIEW FRONT VIEW...
Page 9: ...MACHINE FEATURES Continued HEAD ASSEMBLY...
Page 10: ...MACHINE FEATURES Continued PROXIMITY LIMIT SWITCH LOCATIONS REAR VIEW HEAD TOP VIEW...