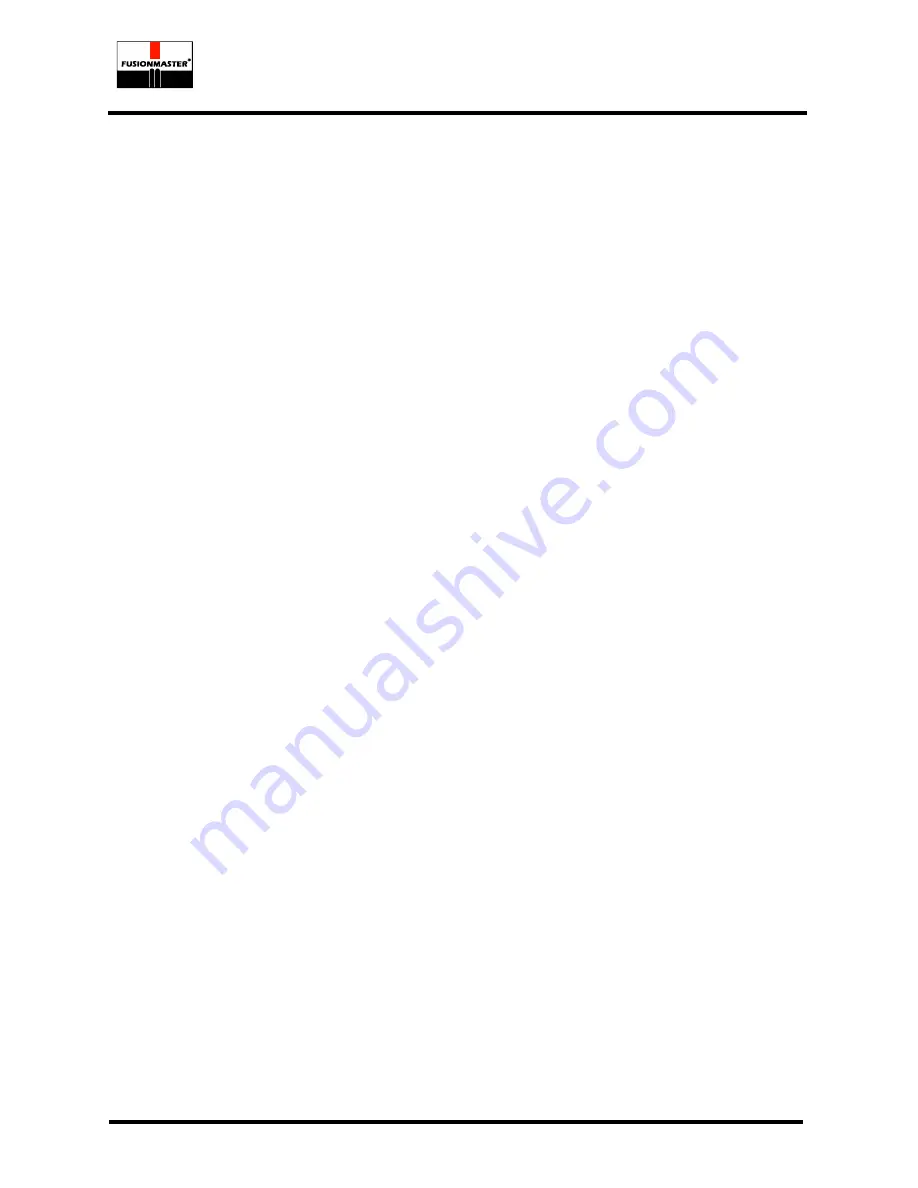
HF225 manual hydraulic butt welder
Simply Better.
Simply Better.
Simply Better.
Simply Better.
FUSIONMASTER®
and
DIXON
®
are registered trademarks of Dixon Industries Pty. Ltd.
©August 2002
Revised August 2013
Page 9
4.
Maintenance - Daily
4.1.
Maintenance - Daily Check List
1.
Keep the machine and accessories clean and free of dust and grease.
Do not
lubricate any HF225 components except for the facer drive (see later).
2.
Inspect hydraulic components for leaks from connections and seals. Overhaul
seals and fittings as necessary.
3.
Check for air in the carriage cylinder (as evidenced by shuddering, and/or
“springing back” of the cylinder). Air trapped in the hydraulics will adversely affect
weld quality and must be removed by bleeding (see later).
4.
Check the pressure gauge needle returns to zero and does not stick.
5.
Check the temperature of a number of points on the surface of both sides of the
heater plate. The reading at any point on either side of the heater plate surface
should not be more than ±10°C from the desired welding temperature. (Refer
later section on heater plates.)
6.
Do electrical safety checks.
7.
Replace non-stick cloths if damaged in way of the weld area.
8.
Facing blades should be sharp and have defect free cutting edges to provide
continuous shaving thickness of 0.30-0.40mm. Shim worn blades if necessary;
sharpen cutter blades if blunt; replace cutter blades if chipped.
9.
Ensure the facer drill is securely fixed into the facer body casting, if not the drive
gears may not mesh properly causing extensive damage.
10.
Feel for “sloppy” movement of the cutter plates. This indicates the need to adjust
the facer drive internally.
11.
If using a portable generator, ensure its output is 240v ± 20v and 50hz, to protect
electronic equipment from permanent damage.
5.
Maintenance - Periodic
In addition to the daily checks, more detailed inspections of the key machine components should
be carried out before commencing each new project, or after 250 operating hours. Any faults
found should be corrected as described in this section.
5.1.
General/Drag
Check the hydraulic cylinder shafts for cuts or dents likely to damage the hydraulic seals.
Check the machine frame, main carriage guide shafts, hydraulic shafts and heater rest bars are
not damaged or bent such that excessive drag pressure results. Without pipe in the machine,
drag pressure should not exceed 500kPa.
5.2.
Heater Plate
Heater surfaces should be flat, smooth and free of dents or gouges. Dress as necessary.
FUSIONMASTER
® heater plates have a vent machined in the edge of the casting to allow
entrapped air to escape from under the non-stick cloth. Clean out any build up of foreign
material from the air vent to prevent any adverse temperature effect.
Caution:
Ensure heater plate non-stick surfaces are protected from damage during transport.
5.3.
Heater Temperature Adjustment
The temperature setting of the HF225 heater is adjusted by turning the screw in the end of the
heater handle, clockwise for higher temperature, and anticlockwise for lower temperature. One
degree of turn will result in approximately one degree of temperature change.
Always allow
several minutes for the plate temperature to stabilise after making any adjustment.
The controller is factory set to 220°C. It has an operating range of 180°C to 260°C.