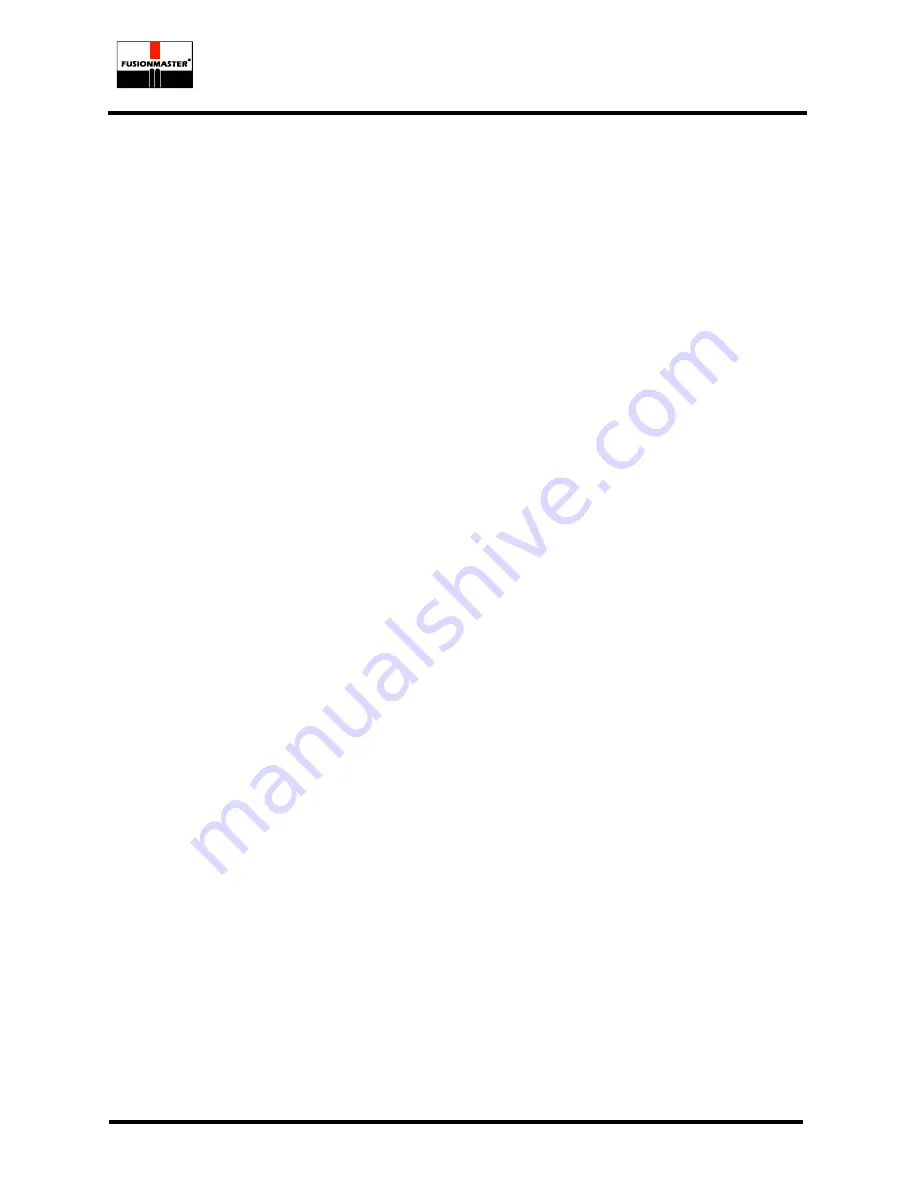
HF225 manual hydraulic butt welder
Simply Better.
Simply Better.
Simply Better.
Simply Better.
FUSIONMASTER®
and
DIXON
®
are registered trademarks of Dixon Industries Pty. Ltd.
©August 2002
Revised August 2013
Page 6
3.
Using the HF225 – single pressure low pressure method
3.1.
Preparation
1.
Connect only to a 240v, 50Hz power source. Ensure the output of any portable
generator used is 240v ±20v.
2.
Check for air in the hydraulic system and bleed if necessary (see maintenance
section).
3.
Clean and/or replace the non-stick cloths. Clean the heater plate before every
weld with clean dry paper or cotton cloth - never use synthetic materials that may
melt.
4.
Check, and if necessary adjust the heater surface temperature.
5.
Install the correct reducing liners for the pipe to be welded.
6.
Check the facer cutting action (the shaving thickness should be 0.30-0.40mm).
7.
Before facing, clean inside and outside of each pipe end, and the cutter blades.
8.
Record the drag pressure from the pressure gauge before every weld.
9.
Add the drag pressure to the calculated pressure to determine the appropriate
bead up and fusion gauge pressures.
3.2.
Pipe Alignment
Place the pipes in the clamp jaws with about 25mm of pipe extending past the clamps into the
weld zone. Tighten the clamp toggle bolts securely to prevent the pipe from moving when under
hydraulic pressure. The outer ends of the pipe should be supported such that any external
bending loads on the machine are eliminated and drag pressure is minimised
Move the pipe ends together until they are almost touching, then check for misalignment
(maximum allowable misalignment is 10% of wall thickness). Tolerances on small bore pipes
should be sufficient to permit pipe alignment in the HF225 without much adjustment of the three
segment clamps. However, in severe out of round situations, adjust out any misalignment by
loosening the clamps and rotating the pipes, and/or using packers as necessary. (Adjustment will
not be possible if the pipe ends are in contact and under pressure.)
Move the pipe end clear of the weld zone and record the drag pressure. Add this value to the
fusion pressure required to join the pipe (refer welding table).
3.3.
Drag Pressure
"DRAG" is the amount of pressure required to overcome carriage friction plus the effort required
to move the pipe. As drag pressure is a variable, it must be measured before every weld.
To determine the drag pressure, operate the pump handle and observe the pressure at which the
carriage just begins to move. The HF225 drag pressure without pipe loaded should be in the
range 200-500kPa.
If drag pressure is excessive it may adversely affect the weld. Drag may be reduced by one or
more of the following actions:
1.
Use a low friction pipe support/roller system.
2.
Ensure the pipe support/roller system maintains the whole length of the pipe level
with the machine base to prevent bending forces acting on the machine frame.
3.
Minimise the amount of pipe being pulled. Welding machines are not designed to
pull multiple lengths of pipe.
4.
Ensure the heater/facer rest bar does not obstruct carriage movement
All of these techniques are always important, but become critical when working near the limits of
machine capacity.
3.4.
Facing
Ensure the heater plate rest bars are retracted during the facing operation.