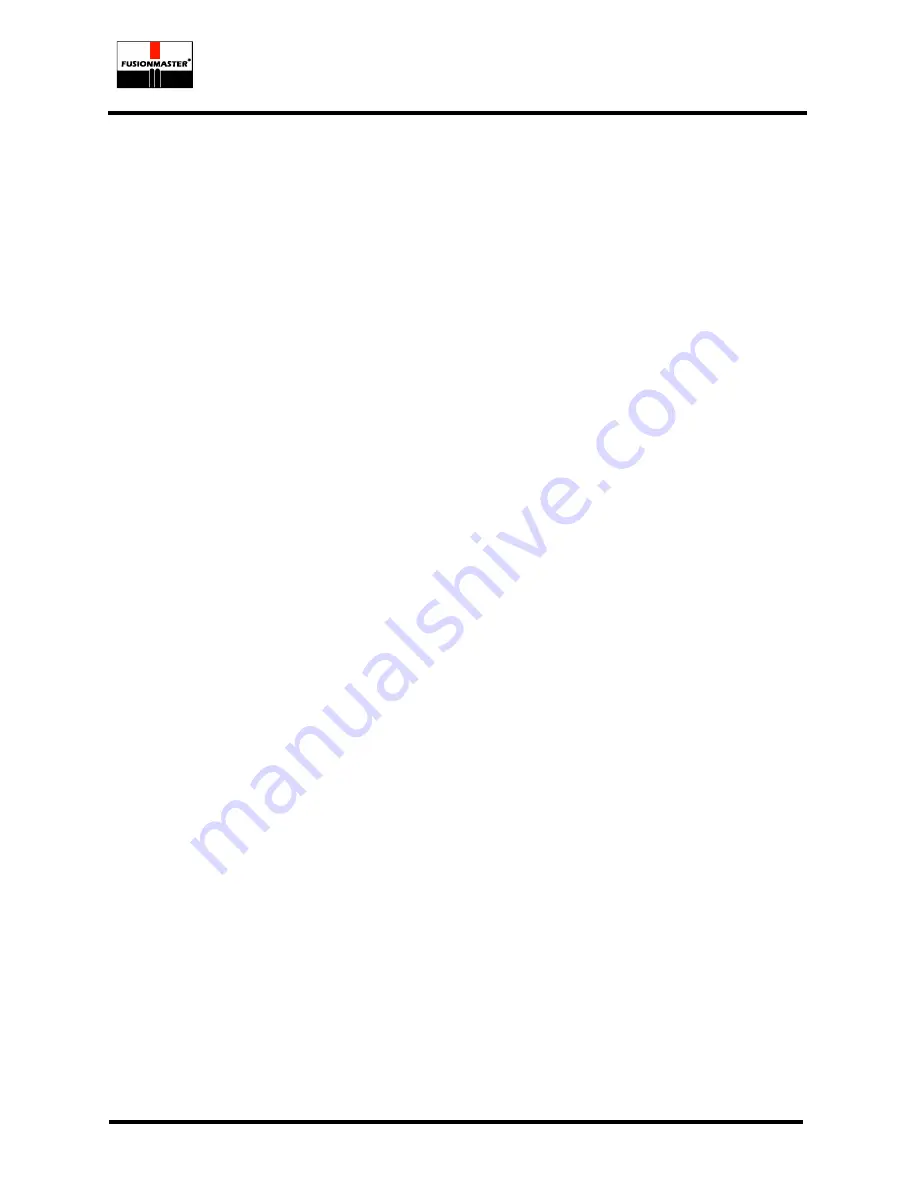
HF225 manual hydraulic butt welder
Simply Better.
Simply Better.
Simply Better.
Simply Better.
FUSIONMASTER®
and
DIXON
®
are registered trademarks of Dixon Industries Pty. Ltd.
©August 2002
Revised August 2013
Page 11
(should be 40 ohms ±10%). If there is a short circuit, the element pad must be
replaced. If the element, leads and connectors are OK, the controller will be faulty
and must be replaced.
6.
Before re-fitting the controller, sparingly coat the sensor probe with some silicon
heat sink compound to increase thermal sensitivity, then carefully insert the
probe into the probe hole.
7.
Reassemble the handle and bracket to the heater plate and tighten screws
securely.
8.
Reconnect the power cord and switch on. Both LEDs should glow immediately.
Allow 20 minutes for the heater to reach temperature and to stabilise before
making any adjustments or measuring temperature.
5.9.
Hydraulic Operating Pressure
The operating pressure of the HF225 is limited to 7,500kPa by a relief valve on the side of the
pump. Should it be necessary to adjust the relief pressure contact the manufacturer for advice.
Care should be taken if increasing the pressure above this setting as the pressure gauge may be
damaged.
(Older models were fitted with a 0-6000kPa gauge with operating pressure limited to 5,500kPa.)
5.10.
Pressure Gauge Calibration
Pressure gauges are easily damaged and may lose their accuracy. Periodically either
1.
Remove the pressure gauge and check it against a known standard test gauge, or
2.
Replace the pressure gauge with a certified gauge from time to time.
5.11.
Hydraulic Bleeding Method
The presence of air in the system could result from loose hydraulic fittings, damaged hydraulic
cylinder shaft or seals. These should all be inspected and repaired before bleeding the system.
The following method is recommended for recharging with oil (use ISO 46 viscosity)
1.
Check there are no loose hydraulic fittings.
2.
The hydraulic system contains approximately 750ml of oil in total.
3.
With the machine standing in its normal position, remove the filler/breather cap
from the oil reservoir, insert a filling funnel and add oil to the reservoir. The
reservoir oil level should be kept about 25mm below the filler/breather cap.
4.
Operate the pump and directional valve alternately such that the cylinder moves
slowly no more than 50mm in either direction. Top up the reservoir as required,
especially if motion stops while pumping.
5.
Repeat this action several times, increasing the distance moved by the cylinder a
few millimetres each time as more oil is transferred into the cylinder. If oil is
ejected from the filler/breather cap during this operation reduce the distance
and/or speed of travel.
6.
As the amount of air being forced from the system reduces, rotate the machine
along its longitudinal axis so that the cylinder piping entry points face vertically up
which allows trapped air to rise and escape.
Do not omit this step or air will
remain in the system.
7.
Continue pumping and move the cylinder to the fully open position, then back to
the fully closed position. Repeat this cycle in each direction until any operation of
the pump handle and the resultant motion of the carriage, is immediate and
exactly in sequence. There should also be no clamp spring back at the end of the
cylinder stroke (either end) on changing the directional control valve.
8.
At this point all air should be fully expelled from the system. Top up the reservoir
when the cylinder shaft is retracted such that the oil level is about 25mm below
the filler/breather cap.