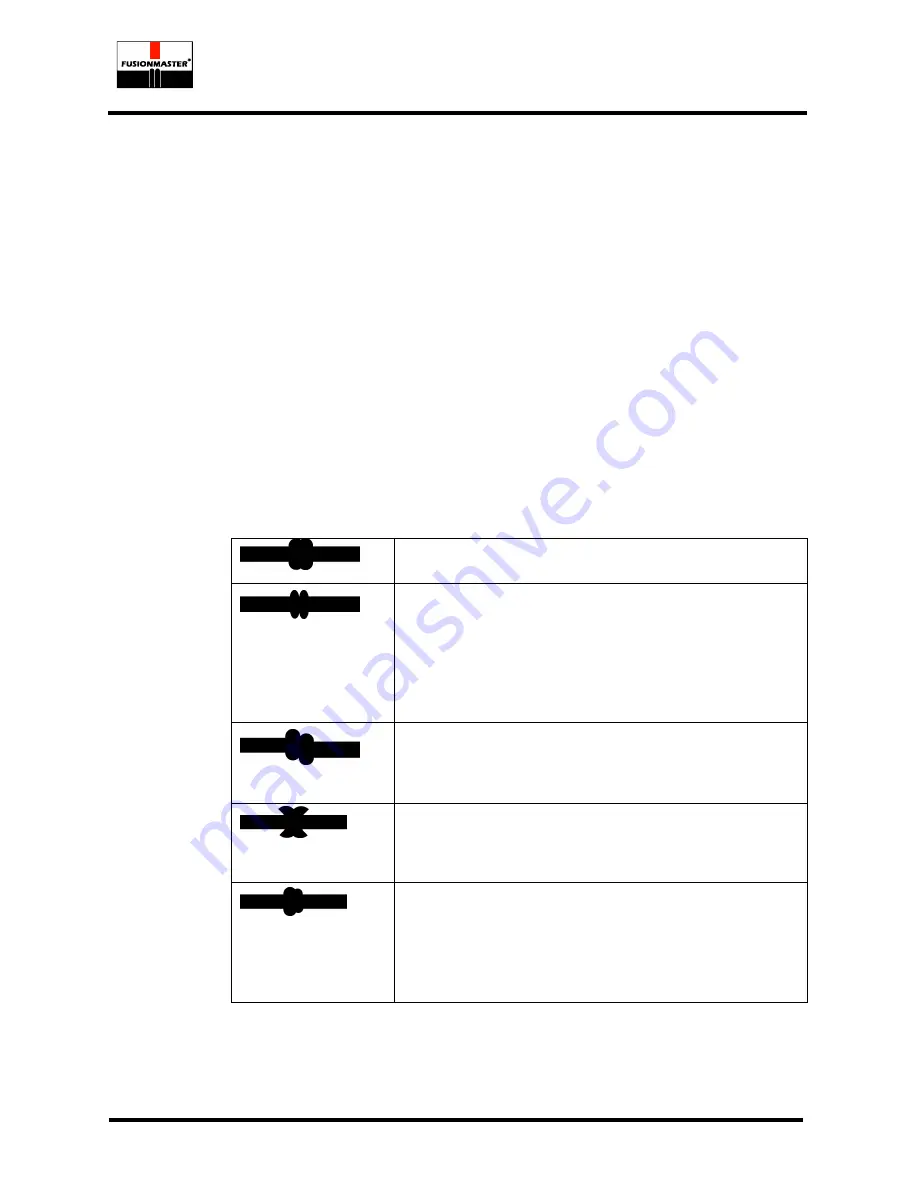
HF225 manual hydraulic butt welder
Simply Better.
Simply Better.
Simply Better.
Simply Better.
FUSIONMASTER®
and
DIXON
®
are registered trademarks of Dixon Industries Pty. Ltd.
©August 2002
Revised August 2013
Page 14
7.
Butt Welding Guidelines
It is recommended that the following guidelines be downloaded from Plastics Industry Pipe
Association of Australia Ltd web site (www.pipa.com.au)
1.
POP003 Butt Fusion Jointing of PE Pipes and Fittings - Recommended Parameters.
2.
TP003 Specifying Butt Welding of Polyethylene Pipe Systems.
FUSIONMASTER®
welders are designed for the “single pressure – low pressure” fusion
method described in POP003.
The welding tables appended to the HF225 operating manual are based on POP003-SP-LP.
Operators should take care to determine the compatibility of materials for butt welding and only
attempt to weld pipes and fittings made of the same polymer, eg PE to PE, PP to PP, PVDF to
PVDF, etc.
The joint area must always be protected from adverse weather conditions, eg strong winds,
excessive cold or heat, or rain, which could lead to the pipe wall developing non-uniformly
heated zones and consequent failure issues.
The weld zone should be free of bending stress, free of notches or similar damage, and be free of
contamination.
8.
Weld failure trouble shooting
(Bead shapes are exaggerated for effect.)
Uniform bead correct welding.
NB the external bead is always more uniform than the internal bead.
Crack down centre of bead.
"Cold weld" signified by clean break through the middle of the weld
with a smooth appearance.
Could be due to insufficient heat soak time or temperature, or
changeover time too long, or excessive soak pressure, or insufficient
fusion pressure, or no allowance for drag pressure, or drag pressure
too great eg due to pulling pipe up a gradient.
Misalignment - maximum allowable 10% of wall thickness.
Care should also be taken to ensure pipes or fittings being joined
have the same diameter and wall thickness or the probability of weld
failure is significantly increased.
Insufficient bead roll over.
Could be due to insufficient heat soak time or temperature, or
changeover time too long, or insufficient fusion pressure, or no
allowance for drag pressure,
Unequal bead size.
Look for temperature gradients e.g. pipe surface in the hot sun vs
pipe in the shade, or heater plate hot spots.
Look for unequal application of pressure.
If unequal uniformly around the whole circumference, look for
physical difference in materials being joined eg melt flow index.