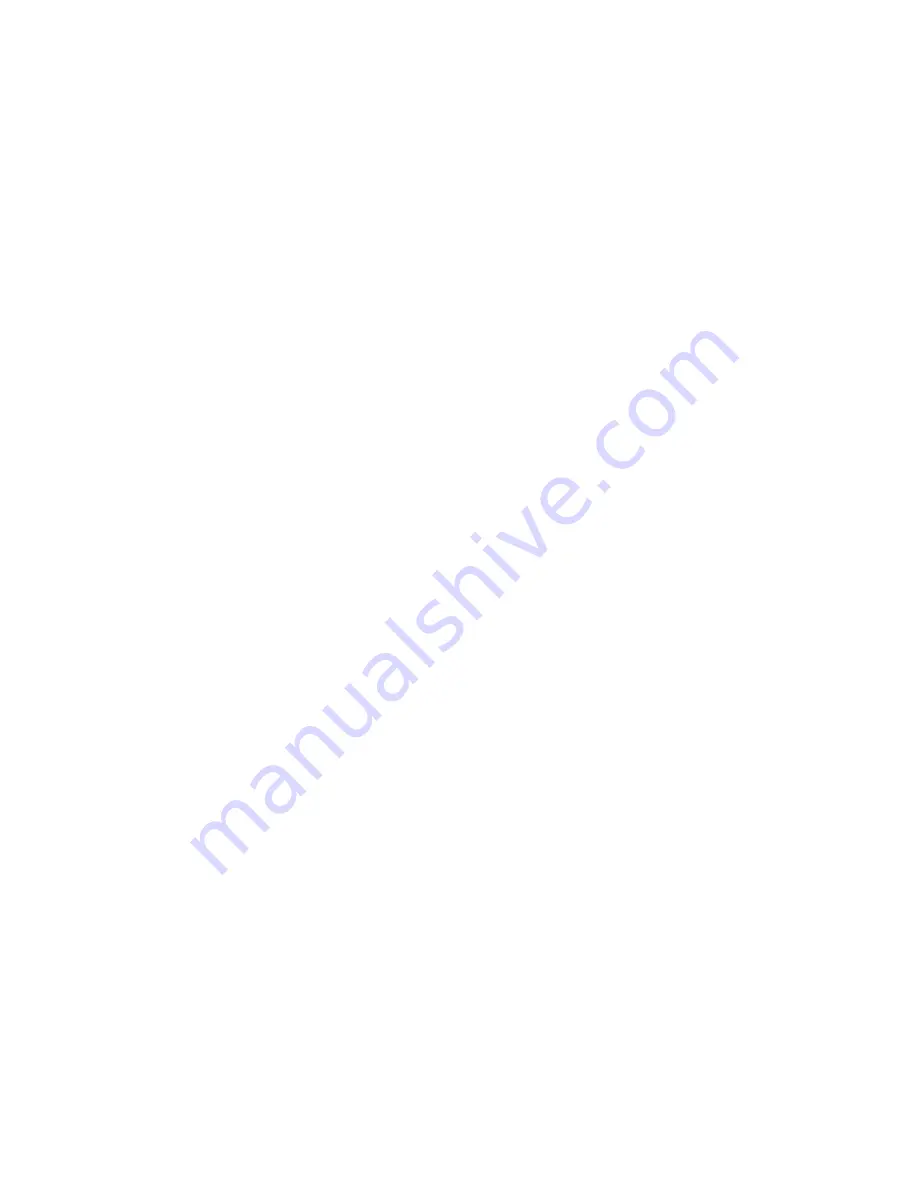
4
Initial Installation Considerations
The location of the unit(s) must be planned to maximize effective operation, service and
maintenance. Should questions arise or assistance is needed consult your DIVERSITECH
distributor.
After the installation, clearance must be available to service the following components:
1. Filters
2. Fan
3. Valves
4. Controls
5. Dust drawer
Inspection
Upon receipt, the collector and the optional components must be checked for damage or loss
incurred during shipping. Damage must be noted on the bill of laden and a claim be filed with
the carrier immediately.
Mechanical Installation of Weld Booth WD-4000D
Note:
Should question arise concerning total weight, consult your DIVERSITECH
Distributor or the DIVERSITECH Factory.
1. Unbolt and remove the master booth from skid. (Master booth is the one with the dust
collector on the top)
2. Rig and lift the master booth up and move it to the desired final position and anchor it
to the floor.
3. Unbolt and remove the slave booth from the skid. NOTE: THE SLAVE BOOTH CAN BE
INSTALLED TO LEFT, RIGHT OR REAR OF THE MASTER BOOTH.
4. Determine the desired location for the slave booth. Remove and
RETAIN the access
cover from the desired side of the master booth. The slave booth ships with only a
cover on the back. (If the slave is to be positioned back to back with the master,
remove and
RETAIN the back cover.)
5. On the inside of each booth there is a hinged door allowing access to the spark filters.
Open the hinged door and remove the spark filters in order to gain access to the nuts
and bolts holding the covers and to facilitate connection of the booths.
6. Set the slave booth in desired place and bolt both booths together using the holes
available.
7. Anchor the slave booth to the floor.
8. Install covers retained in earlier steps on all remaining openings on both booths.
9. Reinstall spark filters and secure hinged door.
10. Feed one light power supply cable through the hole provided in the top of the slave
booth and connect the power cable to the light.
11. Connect compressed air and electrical per Installation Manual.
Compressed Air Supply
The compressed air
supply is used to reverse jet pulse the dust coated cartridge filters. A 1”
diameter (minimum) dedicated supply with 80-90 PSI is required. The air supply line to the
accumulator tank must include water, oil and particulate filtration. Water and/or oil in the
compressed air will reduce the effectiveness of the reverse jet pulse cleaning, destroy the