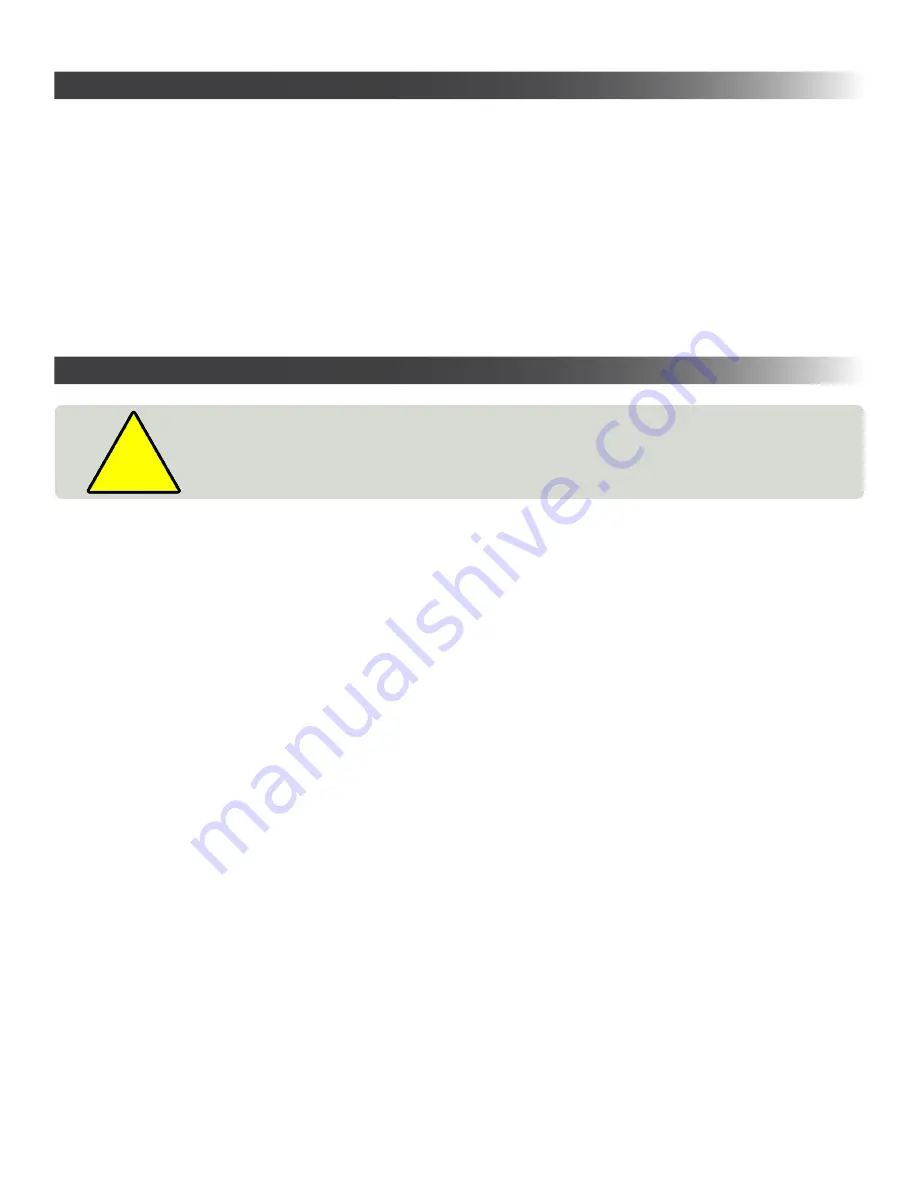
!
CAUTION: This should only be done in consultation with an authorized Diversitech
technician! The following steps have been done at the factory and should not need
adjustment
11
Alarms
Any alarm condition will be indicated on the user interface and the buzzer on the panel will be heard. When one of these alarms is present, the machine
will lock-down and will not allow to be started:
• Motor Overload: if the main motor overload is tripped. The alarm will remain until the situation is corrected and the over load is manually reset.
• High temperature: if the temperature in the filter units exceed the threshold. The alarm will remain until the situation is corrected.
• Pressure switch (optional): if the pressure in the unit exceed the threshold set on differential unit. The alarm will remain until the situation is corrected.
• Exhaust fan: if the exhaust fan is not detected as running within a certain amount of time once the machine is stopped. The alarm will remain until the
situation is corrected.
• Low level: if the water level reaches the low level set point set from the interface for 5 seconds or more. The alarm will remain until the situation is
corrected.
• High level: if the water level reaches the high level set point set from the interface for 5 seconds or more. The alarm will remain until the situation is
corrected.
Level Set Point:
Initial Set Point Adjustment if the PLC has been factory reset
At the initial star-up, the set point will be at 0.
To set the running water level, the machine has to be powered and “on”. Once on, the button #1 can be pressed to enter the manual set point entry.
Then, use the button #2 and #3 to modify the set point value. If no key is pressed within 5 seconds, the interface will go back to the main screen. The
other way would be to fill the machine to the desired level (start between 7 to 7.5 inches of water) and then press the button #4 for 5 seconds to teach
the set point.
The machine is ready to start.
Since the water level has to be higher while stopped, the running set point has to be set once the water has reached
turbulent levels. To set the “Running Set Point” press button 4 for 5 seconds or until the display shows the current
level=running level. Note the refill sequence has been set to start when the current level is 4 below the running level for at least 30 seconds.
Level alarms:
To set the level upper limit, the button #2 can be pressed. Then, use the button #2 and #3 to modify the set point value. If no key is pressed within 5
seconds, the interface will go back to the main screen.
To set the level lower limit, the button #3 can be pressed. Then, use the button #2 and #3 to modify the set point value. If no key is pressed within 5
seconds, the interface will go back to the main screen.
Initial Sensor Setup
Summary of Contents for TYPHOON WX Series
Page 19: ...19 NOTES...