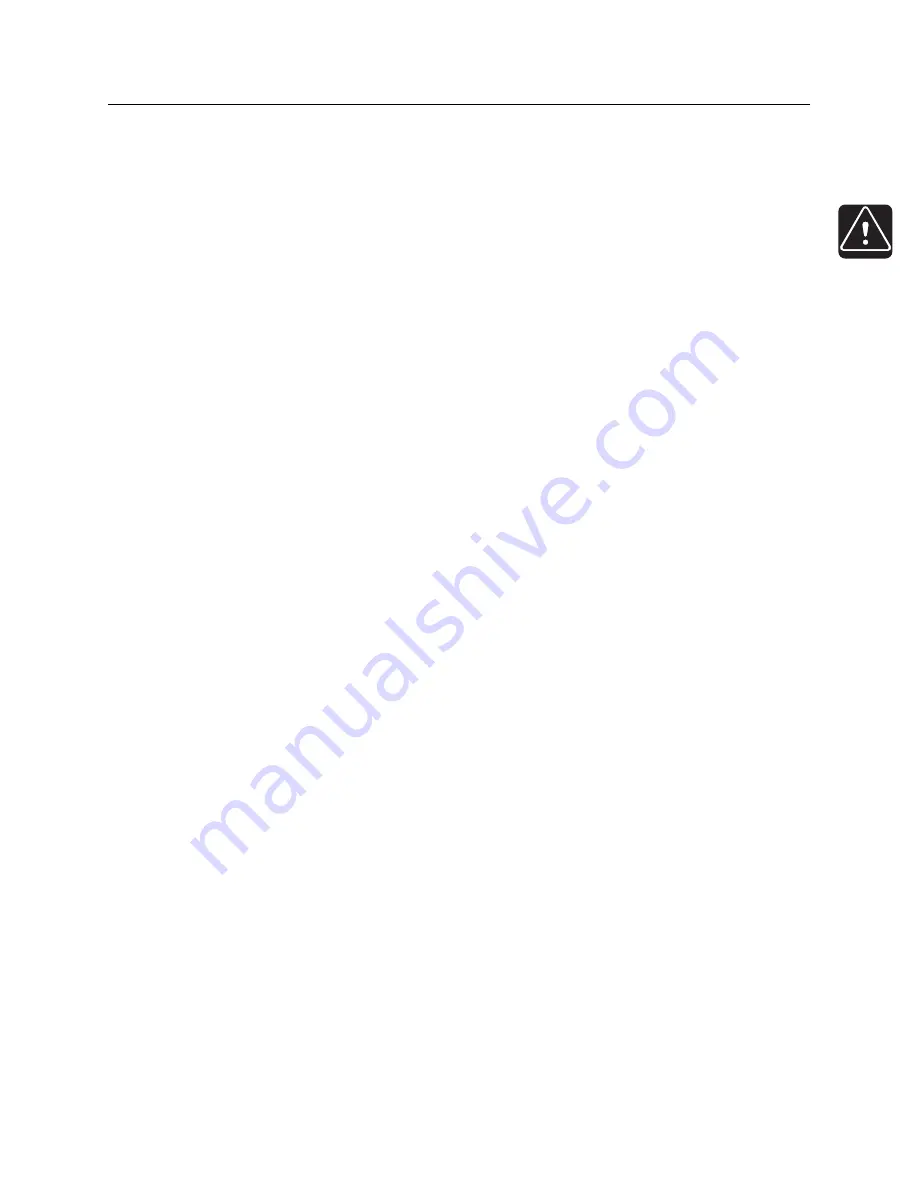
SK500 Operator’s Manual
Safety - 9
CMW
Safety
Chapter Contents
Guidelines . . . . . . . . . . . . . . . . . . . . . . . . . . . . . . . . 10
Safety Alert Classifications . . . . . . . . . . . . . . . . . . 11
Safety Alerts . . . . . . . . . . . . . . . . . . . . . . . . . . . . . . 12
Emergency Procedures . . . . . . . . . . . . . . . . . . . . . 15
•
Electric Strike Description . . . . . . . . . . . . . . . . . . . . . . . . . . . . . . . . . . .15
•
If an Electric Line is Damaged . . . . . . . . . . . . . . . . . . . . . . . . . . . . . . . .16
•
If a Gas Line is Damaged . . . . . . . . . . . . . . . . . . . . . . . . . . . . . . . . . . . .16
•
If a Fiber Optic Cable is Damaged . . . . . . . . . . . . . . . . . . . . . . . . . . . . .16
•
If Machine Catches on Fire . . . . . . . . . . . . . . . . . . . . . . . . . . . . . . . . . .16
Summary of Contents for SK500
Page 1: ...SK500 Operator s Manual 054 091 Issue 2 0 CMW...
Page 9: ...Contents 8 SK500 Operator s Manual CMW...
Page 33: ...Drive 32 SK500 Operator s Manual Shut Down CMW...
Page 65: ...Service 64 SK500 Operator s Manual 500 Hour CMW...
Page 72: ......
Page 73: ......
Page 74: ...SK500 Operator s Manual Service Record 73 CMW Service Record Service Performed Date Hours...
Page 75: ...Service Record 74 SK500 Operator s Manual CMW Service Performed Date Hours...