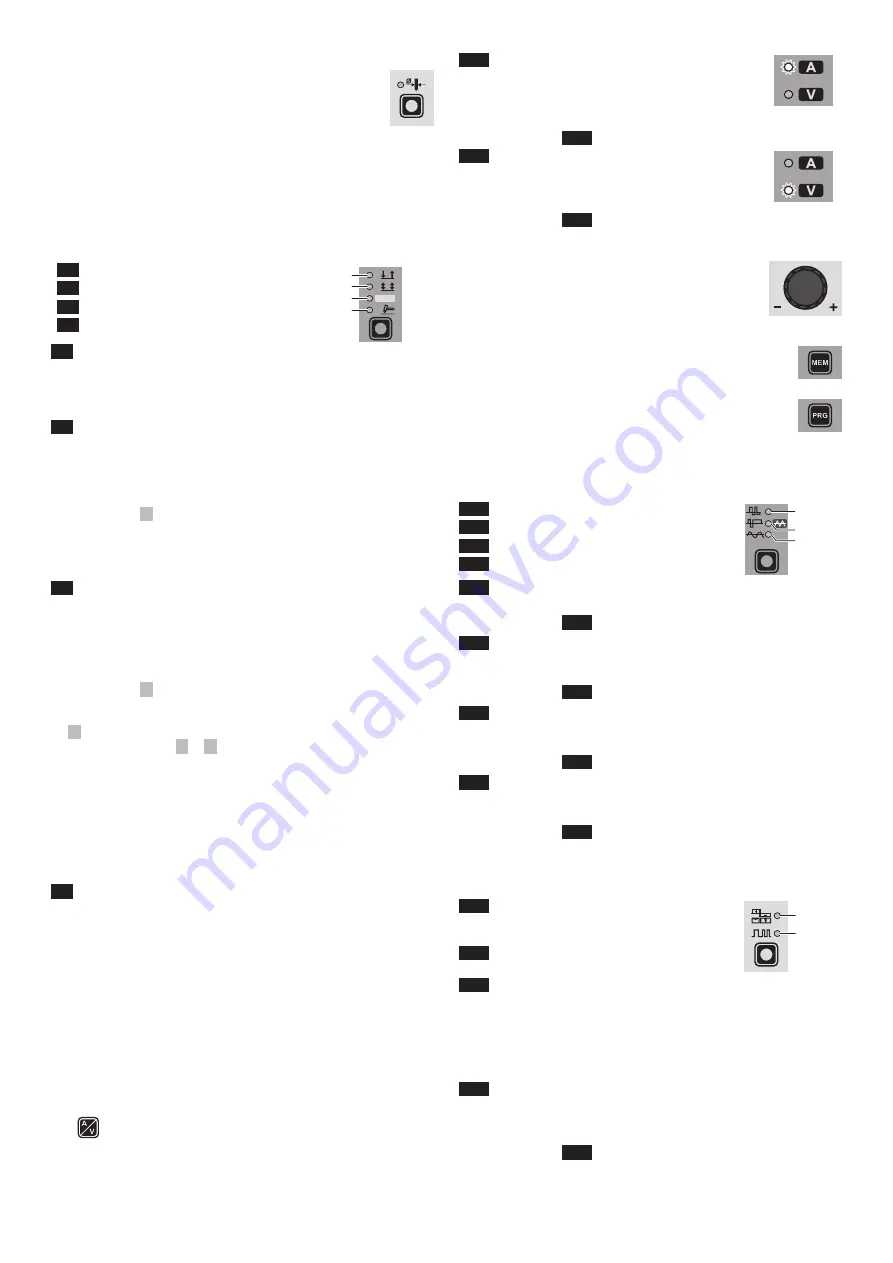
16
■
ELECTRODE DIAMETER
For TIG welding with HF ignition, it allows you to use the
relevant key to set the diameter of the tungsten electrode
used, and/or to change it using the ENCODER knob, in
order to achieve the best control of the AC arc in a syn-
ergic manner.
WARNING: The electrode diameter CANNOT be selected when
the welding power source is set for the SPECIAL configuration.
■
WELDING MODE
The welding power source offers
4
welding modes. Each time
the button is pushed, the welding power source switches to se-
lect the welding mode indicated by the LED that stays lit, in the
following order:
L5
2 STROKES
L6
4 STROKES
L7
SWITCH
L8
SPOT WELDING
L5
L6
L7
L8
SWITCH
L5
2 STROKES
When the torch button is pushed welding begins starting with the
INITIAL CURRENT (if SLOPE UP is selected), while when it is re-
leased welding ends when the FINAL CURRENT is reached (if
SLOPE DOWN is set).
L6
4 STROKES
TIG welding takes place as follows:
•
When the torch button is pushed welding begins at the INITIAL
current.
•
When the torch button is released the SLOPE UP process is
carried out (if applicable) and the current returns to the PRIN-
CIPAL value
I
1
.
•
When the torch button is pushed the SLOPE DOWN process
is carried out (if applicable) and the current returns to the FI-
NAL value.
•
When the button is released the welding SWITCH ends.
L7
SWITCH
When this function has been activated, TIG welding takes place
as follows:
•
When the torch button is pushed welding begins at the INITIAL
current.
•
When the torch button is released the SLOPE UP process is
carried out (if applicable) and the current returns to the PRIN-
CIPAL value
I
1
.
•
When the SWITCH button is pressed and released within less
than 1 second the welding current goes to the SWITCH value
(
I
2
), and by repeating this operating you can move between the
two current levels (
I
1
), (
I
2
) an infinite number of times.
•
When the torch button is pushed and held down (for longer than
1 second) you exit the SWITCH, the SLOPE DOWN process is
carried out (if applicable) and the current returns to the FINAL
value. When the torch button is released the welding SWITCH
ends.
This welding mode is especially indicated for welding profiles with
different thickness, where continuous current variation is required.
Also, when welding aluminium, it allows you to have a higher initial
current, thereby facilitating pre-heating of the workpiece.
L8
SPOT WELDING
This can be used by pushing the torch button to spot weld for a pre-
set period of time (in seconds) at the end of which the arc switches
off automatically. The tack welding function is divided into 3 types:
•
TIG AC and TIG LIFT DC tack welding.
•
TIG HF DC tack welding with a single DIX ARC COOL SPOT
point.
•
TIG HF DC tack welding with a Multi-DIX ARC COOL SPOT
function.
See the relevant paragraphs in the subsequent pages of this man-
ual.
■
DISPLAY
Displays the selections made using the various Keys (with corre-
sponding LED on or flashing) and regulated using the ENCOD-
ER knob.
The
button can also be used to view:
L32
AMPERE (CURRENT )
•
When the welding power source is in stand-by, the
Amps (A) set.
•
When the welding power source is welding the real
Amps (A) at which the operator is actually welding.
WARNING: LED
L32
switched on and steady.
L33
VOLT (VOLTAGE)
•
The actual VOLTS (V) at the welding clamps (the
value displayed CANNOT BE CHANGED OR
REGULATED).
WARNING: LED
L33
switched on and steady.
■
ENCODER knob
This is used to regulate and change the welding
parameters, according to which LED is switched
on and the value shown on the DISPLAY, which
is necessary for the welding power source to work
correctly.
■
SAVE “MEM”
Used to save the parameters for the welding programs.
■
PROGRAM “PRG”
Used to call up welding programs.
■
WAVE
During TIG AC welding with HF ignition, it makes it possible to con-
trol the following wave shapes:
L24
DYNAMIC TIG
L25
SPEED TIG
L25
COLD TIG
L26
SOFT TIG
WAVE
L24
L25
L26
L24
DYNAMIC TIG
Square wave: highly dynamic arc for all applications.
WARNING: LED
L24
switched on and steady.
L25
SPEED TIG
Mixed wave: excellent penetration with high welding speed and
low electrode consumption.
WARNING: LED
L25
switched on and steady.
L25
COLD TIG
Triangular wave: low heat generation with reduced distortion, ide-
al for minor thicknesses.
WARNING: LED
L25
switched on and flashing.
L26
SOFT TIG
Sinusoidal wave: gentle, soft arc with low noise, ideal for aver-
age thicknesses.
WARNING: LED
L26
switched on and steady.
■
BALANCING and FREQUENCY
During TIG AC welding with HF ignition, it makes it possible to set
one of the following parameters, using the relevant key:
L30
BALANCING of the TIME and
AMPLITUDE of the AC welding
current (BALANCE PLUS)
L31
FREQUENCY of the AC welding
current
L30
L31
L30
BALANCING of the TIME and AMPLITUDE of the AC
welding current (BALANCE PLUS)
It is possible to adjust both the time (t) and the amplitude of the
current (I) independently or simultaneously, using positive or neg-
ative values for the time the electrode stays in place. These set-
tings ensure perfect control of penetration and cleanliness, with a
drastic reduction in side incisions.
L31
FREQUENCY of the AC welding current
The high frequency makes it possible to weld minor thicknesses
with excellent results, while the low frequency is ideal for welding
average thicknesses, or where edge preparation is poor.
WARNING: LED
L31
switched on and flashing.
Summary of Contents for DIX TIG GO 1806.M AC/DC
Page 10: ...10 Wiring diagram DIX TIG GO 1806 M AC DC...
Page 11: ...11 2101WA31...
Page 12: ...12 Wiring diagram DIX TIG GO 2506 M AC DC...
Page 13: ...13 2101WB09...