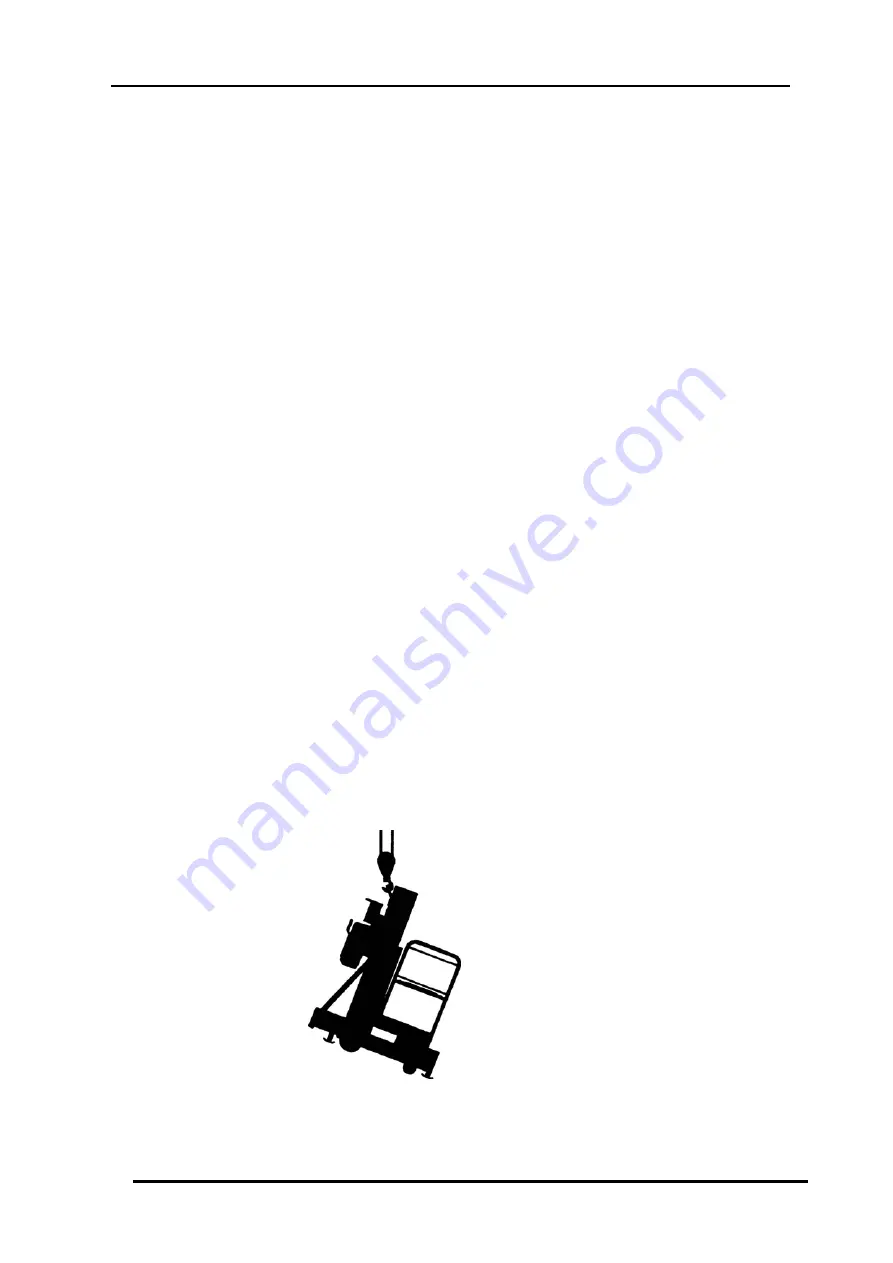
Operator’s Manual
Transport Instructions
GTWY1200 SERIES 20
Winching the Machine onto a
Flatbed Truck
1. Fully lower the platform.
2. Push in the red Emergency Stop buttons,
turn the key switch to the off position and
remove the key. Turn off the circuit
breaker. Cut out the power and fixed the
cable.
3. Remove the outriggers from the base and
place them in the storage sockets.
4. Inspect the entire machine for loose or
unsecured items.
5. Connect
the
cable
to the winching point
located at the rear of the base.
6. Carefully winch the machine onto the
truck.
7. Secure the machine base to the transport
vehicle. See Securing the Machine.
Loading the Machine with a
Crane
Use the lifting eye
mounted on the rear
mast column.
The battery pack must
be removed before lifting
the machine with a crane.
Disconnect the battery
plug before removing the
battery pack.
Be sure to inspect the machine and remove
any loose or unsecured items.
Always place the lifting hook through the lifting
eye so that it points away from the machine.