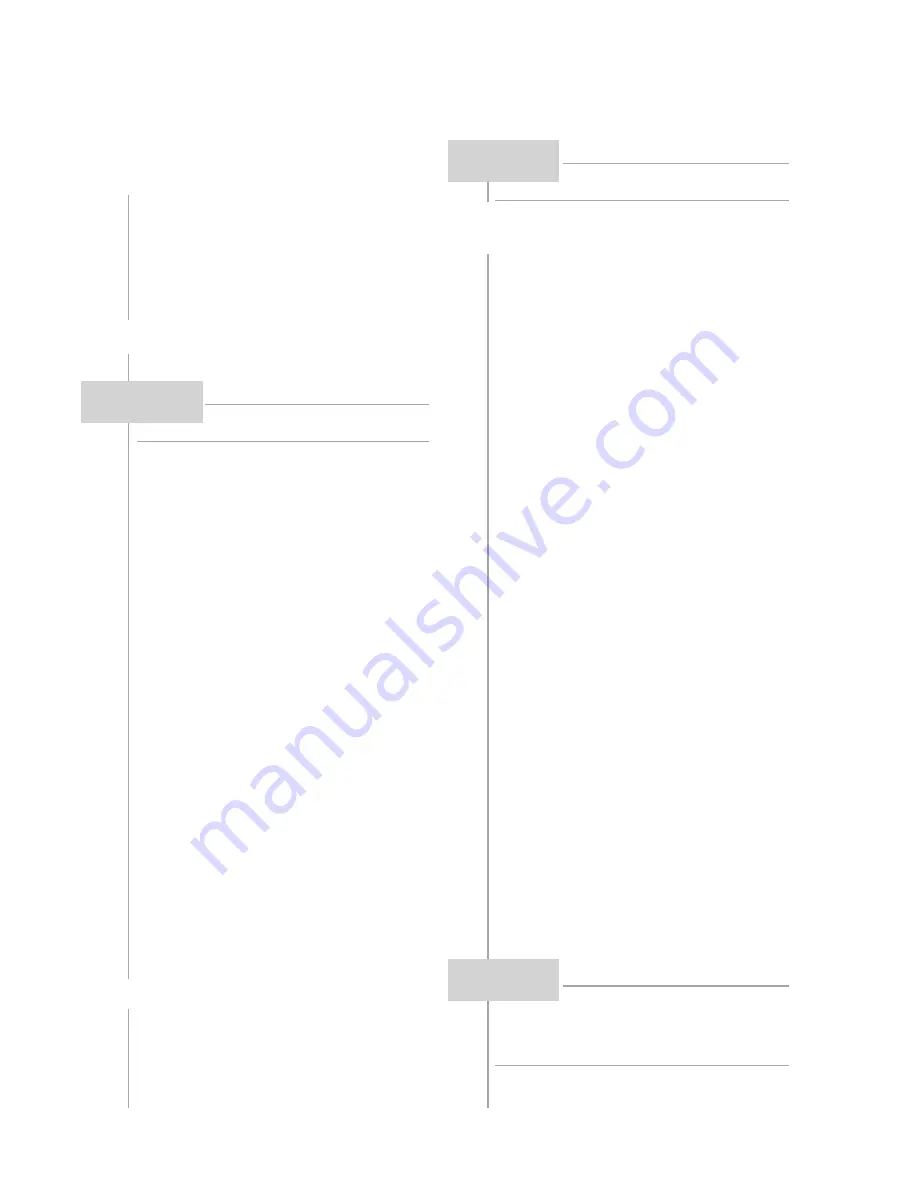
6
6
MOUNTING
CAUTION!
MOUNTING
6.1 General
The following connections need to be established
on the heat pump:
- supply/return flow of well system
- supply/return flow of heating system
- power supply
6.2 Heating-Side Connection
The heating system must be flushed
prior to connecting the heat pump.
Before completing the heat pump connections on
the heating water side, the heating installation must
be flushed in order to remove any impurities that
may be present, as well as residues of sealing
material, and the like. Any accumulation of deposits
in the condenser may result in a total failure of the
heat pump.
Once the installation on the heating side has been
completed, the heating system must be filled, de-
aerated and pressure-tested.
Heating water minimum flow rate
The heating water minimum flow rate through the
heat pump must be assured in all operating states
of the heating system. This can be accomplished,
for example, by installing a differential pressure-free
manifold or an overflow valve. The procedure for
setting an overflow valve is described in the Chapter
Commissioning.
Frost protection for installations prone to frost
Provided the controllers and circulating pumps are
ready for operation, the frost protection feature of the
controller is active. If the heat pump is taken out of
service or in the event of a power failure, the system
has to be drained. In heat pump installations where
a power failure cannot be readily detected (holiday
house), the heating circuit must contain a suitable
antifreeze product.
6.3 Heat Source-Side Connection
The following procedure must be observed when
making the connection:
Connect the well lines to the flow and return pipes
of the heat pump.
The well water must meet the required
water quality standard.
6.4 Electrical Connection
The following electrical connections must be
established on the heat pump.
-
Connection of the control wire to the control panel
of the heat pump via terminal X1: L/N/PE.
-
Connection of the load wire to the control panel
of the heat pump via terminal X5: L1/L2/L3/PE.
-
Connection of the well pump load wire to the
control panel of the heat pump via terminal
X5: L11/L21/L31/PE.
-
Connection of the well pump (to be provided
by the customer) to the control panel of the
heat pump via terminal X1: PE and pump
contactor K2: 2/4/6.
When connecting the load wire of the well pump it
must be ensured that the power supply for these
terminals cannot be disconnected by the tariff
contactor in order to ensure the cutout delay of
the well pump.
A l l e l e c t r i c a l c o m p o n e n t s r e q u i r e d f o r t h e
operation of the heat pump are located on the
control panel.
For detailed instructions concerning the connection
and functioning of the heat pump controller refer to
the operating manual supplied with the controller..
An all-pole disconnecting-device with a contact-
gap of at least 3 mm (e.g. utility company disable
contactor or power contactor) as well as a 3-pole
circuit breaker with simultaneous tripping of all
external conductors. The required cross-sectional
area of the conductor is to be selected according
to the power consumption of the heat pump, the
technical connection requirements of the relevant
electrical utility company as well as all applicable
provisions. Details on the power consumption of
the heat pump are contained on the product
information sheet and the rating plate. The terminals
are designed for a conductor cross-section of
max. 10 mm˝.
When connecting the load line, make
sure that the phase sequence is correct (if the
phase sequence is not correct the heat pump will
not perform properly and generate abnormal
noise).
CAUTION!
CAUTION!
Summary of Contents for WI 14CS
Page 30: ...Notes...
Page 31: ...Notes...