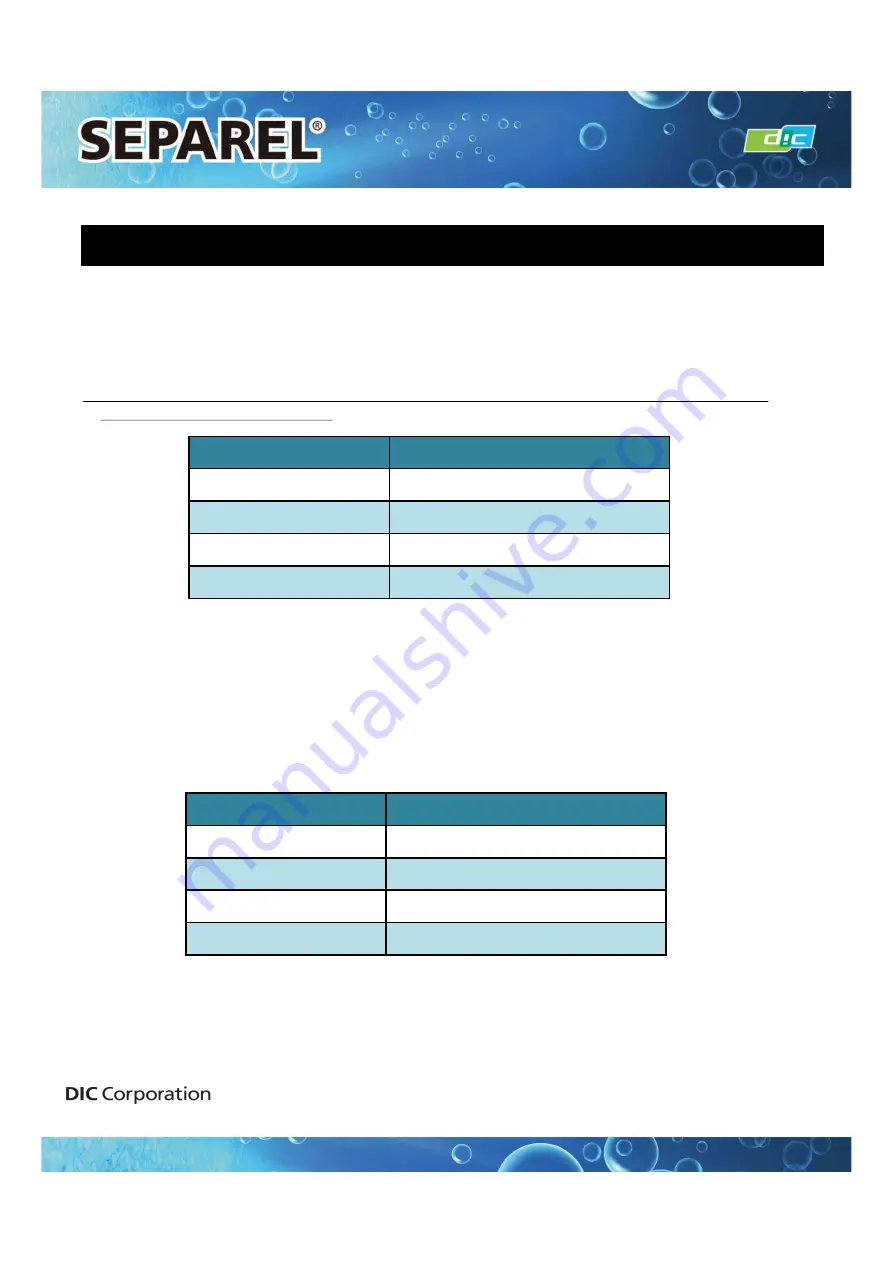
17
17
ᵮᶐᶍᶂᶓᶁᶒ
ᵫᵿᶖᶇᶋᶓᶋ ᵮᶐᶃᶑᶑᶓᶐᶃᴾᵰᶃᶑᶇᶑᶒᵿᶌᶁᶃ
ᵮᵤᵋᵎᵎᵏᵢᴾᶑᶃᶐᶇᶃᶑ
•†‥‒‿⁂⁓‒‚ ‒‥‒⁔⁓‛
ᵮᵤᵋᵎᵎᵒᵢ ᶑᶃᶐᶇᶃᶑ
•†‥‒‿⁂⁓‒‚ ‒‥‒⁔⁓‛
ᵮᵤᵋᵎᵏᵓ ᶑᶃᶐᶇᶃᶑ
•†‥‒‿⁂⁓‒‚ ‒‥‒⁔⁓‛
ᵮᵤᵋᵎᵑᵎᴾᴾᴾᶑᶃᶐᶇᶃᶑ
•†‥‒‿⁂⁓‒‚ ‒‥‒⁔⁓‛
ᵮᶐᶍᶂᶓᶁᶒ
ᵤᶊᶍᶕ ᵟᶐᶃᵿ
ᵮᵤᵋᵎᵎᵏᵢᴾᶑᶃᶐᶇᶃᶑ
•† ‒
̽
•‒‾‡⁚
ᵮᵤᵋᵎᵎᵒᵢ ᶑᶃᶐᶇᶃᶑ
‥‒
̽
‣•‒‾‡⁚
ᵮᵤᵋᵎᵏᵓ ᶑᶃᶐᶇᶃᶑ
‧•‒
̽
‧••‒‾‡⁚
ᵮᵤᵋᵎᵑᵎᴾᴾᴾᶑᶃᶐᶇᶃᶑ
‣••‒
̽
‣„•••‒‾‡⁚
Make sure that the liquid feeding pressure at the inlet port is lower than the maximum pressure value described in
the specification sheet.
If the feeding pressure exceeds the maximum value, even momentarily, the hollow fiber may be damaged and ink
may leak into the vacuum line.
ͤ
The warranty will not apply in cases where liquid feeding pressure exceeds the maximum pressure value
specified in the specification sheet,
INSTRUCTION MANUAL
Even if liquid feeding pressure is lower than the specified maximum pressure, an increased flow rate will cause
lesser degassing performance. On the other hand, if the flow rate is too low, degassing cannot be efficient.
Therefore, DIC supplies recommended flow ranges in the table below.
ͤ
The recommended flow range below was calculated when using water. In the case of high viscosity liquid, a
suitable flow range will be more narrow.
REFRENCE DATA 4:
Setting Value of Vacuum Pressure Degree
Application Materials Product Division