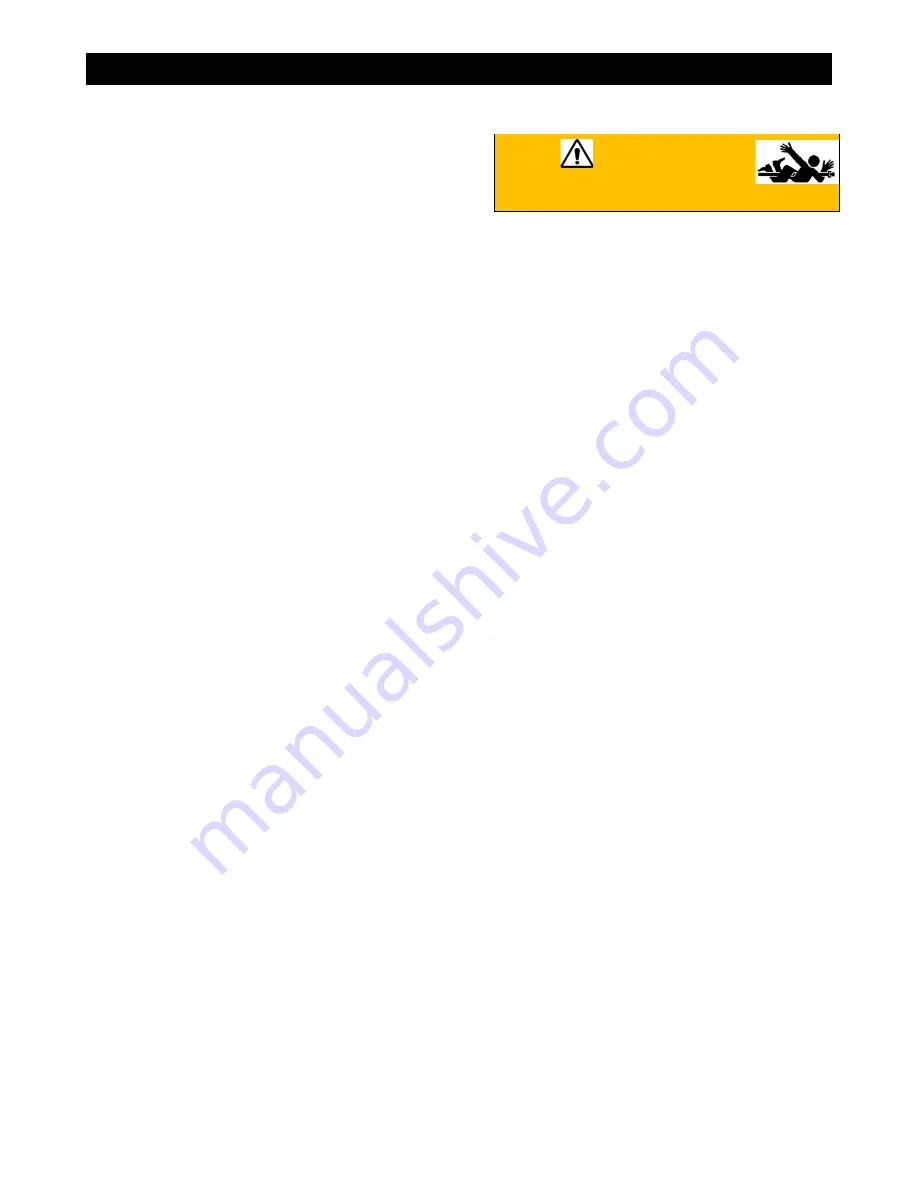
MAINTENANCE
Radiator
Ensure that the radiator is cool prior to
cleaning. Use compressed air to clean the
radiator fins being careful not to damage the
fins. A mild detergent with low pressure water
can also be used to degrease the radiator.
NOTE: Damaged radiator fins can and will
diminish the cooling capacity of the radiator.
Control Panel
Do not spay water on the control panel to
clean. Use a damp cloth or compressed air to
clean electrical components. Dry the control
panel after cleaning.
Display Screen and Camera Lens
Do not spray water on the display screen or
the camera lens to clean. Use a damp cloth to
wipe it clean and dry the screen with a lint free
cloth.
Engine
Use a mild detergent and water to clean the
engine. Do not to spray water forcefully on the
engine to prevent damage to components.
NOTE: Do not spray water into the exhaust
pipe or air filter.
Part Lubrication
WARNING
DO NOT grease parts with the
engine running.
Lubricate all necessary parts on schedule for
maximum saw efficiency. Occasionally
lubricate controls, cables, hinges, latches, and
linkages with a spray lubricant when
movement becomes stiff and/or sluggish. Use
one to two full pumps of NLGI No. 2 premium,
lithium-based grease when lubricating all
grease fittings.
NOTE: Use more grease on bearing grease
fittings if they are too hot to touch after
completing work.
Post Cleaning
•
Lubricate the machine as required.
•
Dry all electrical components using
compressed air.
•
Do not start the machine until it has had
time to thoroughly dry.
41