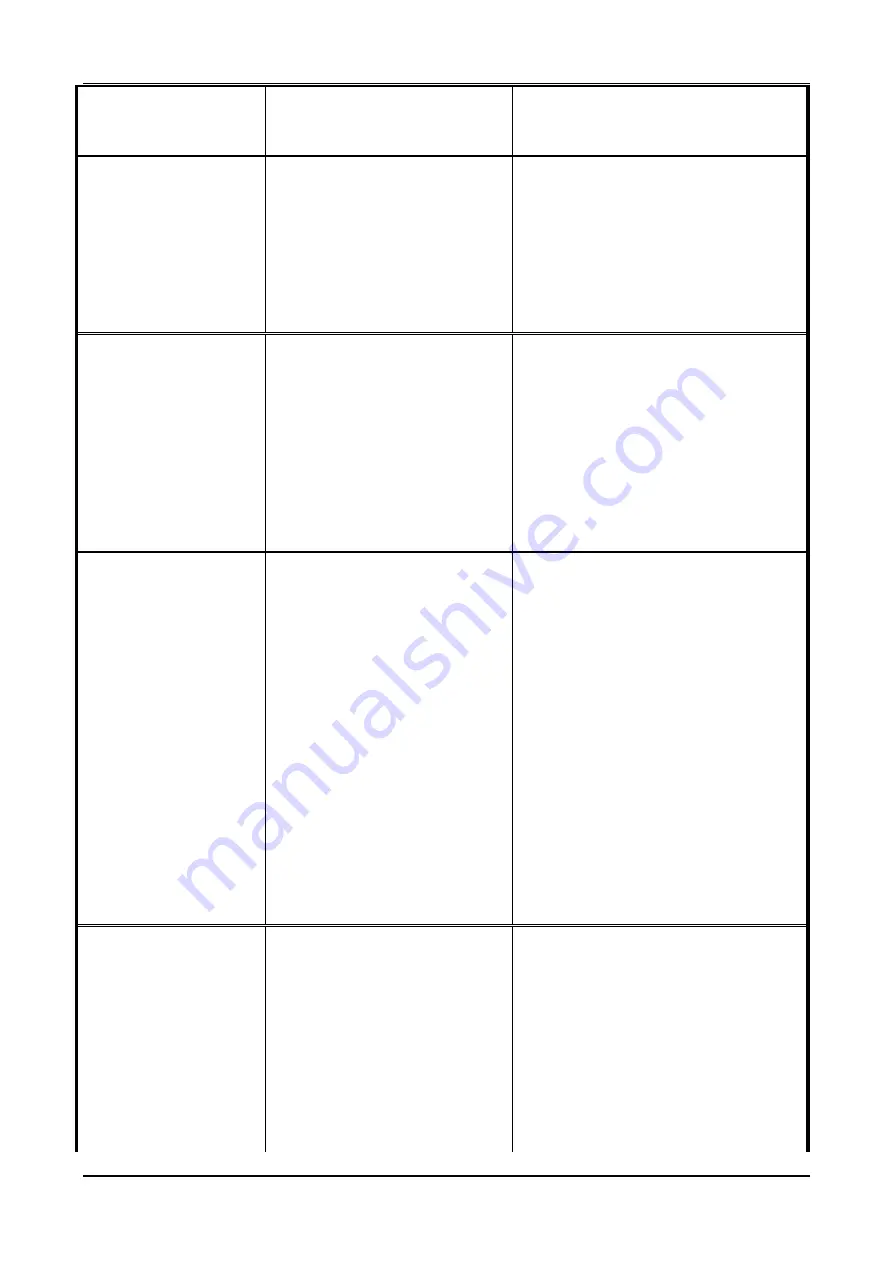
26
card.
Cutter are not able to
cut the sleeve
appropriately
i)
Fault in pneumatic supply
circuit.
ii)
Reciprocating cutter blade
blunt or damaged.
i)
Check complete circuit for
function and any component for
failure.
ii)
Inspect cutter blade and replace
blade if necessary.
Material jam above, or
inside cutting blade
i)
Material jammed caused by
incomplete cutting.
ii)
Material jammed caused by
blade not turning away
from the mandrel after
cutting
i)
Check the cutter blade for damages
and replace blade if necessary.
ii)
Reposition the blade position;
please refer to section 2.4. Please
note that this is the cause of the
jam up before adjusting the blade
position.
Material splits when
passing through the film
spreader/mandrel.
iii)
Material too heavily creased
during manufacture.
iv)
Film spreader damaged or
has sharp edges.
v)
Film spreader too tight a fit
to material.
vi)
Perforator damaging
material.
vii)
Material not welded on
seam correctly.
iii)
Remove material and open flat and
check for damage on crease
indicated by opaque witness marks
along crease.
iv)
Check for damage and replace if
necessary.
v)
Check material size and tolerances
with reference to film spreader.
vi)
Check perforator wheel for free
rotation and lubricate if necessary.
vii)
This fault sometimes occurs at end
of reel – replace reel.
Sleeve not being fitted
to product
i)
Shooting Head set too
high/low to product.
ii)
Product not central in
relationship to centre line
of material feed.
iii)
Sleeve fed too early.
iv)
Sleeve fed too late.
i)
Set vertical adjustment system to
correct height.
ii)
Adjust conveyor guide rails and
scroll to centralise product. See
section 2.9 Pitching Scroll.
iii)
Adjust product sensor in direction
of product flow.
iv)
Adjust product sensor against
Summary of Contents for NSV-400
Page 3: ...4 1 3 BASIC BLUEPRINTS...