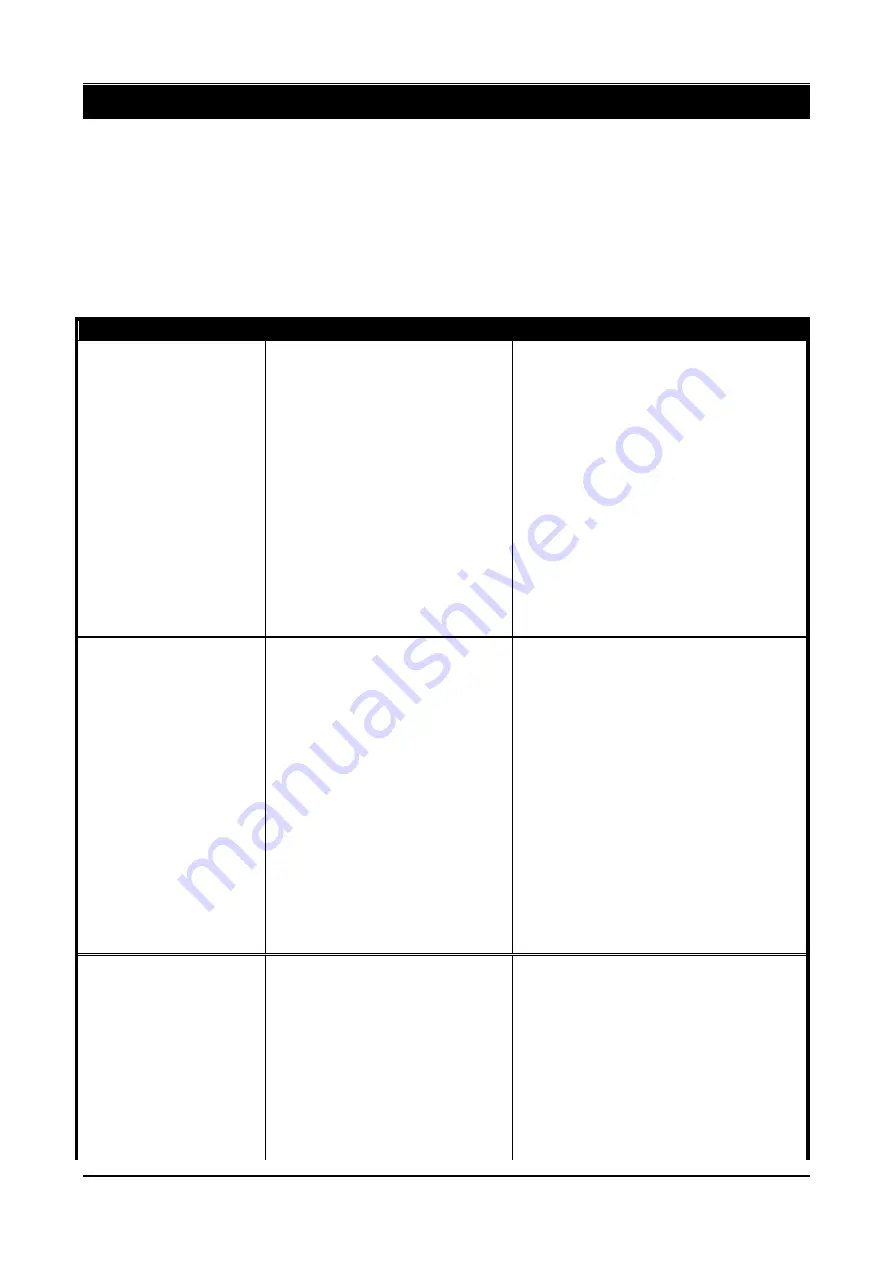
25
T R O U B L E S H O O T I N G
When encountering machine malfunctioning, please check all the parameter checking first, before
proceeding to tuning the machine.
The following list is a guide to identifying the cause of the more common problems encountered in
banding/sleeving products.
FAULT
CAUSE
REMEDY
Sleeves not feeding
properly
i)
Mandrel not straight
ii)
Material unwind not
functioning.
iii)
Product sensor not
functioning.
i)
Make sure that the mandrel is
properly installed, with all support
and feed rollers adequately
tightened.
ii)
Check the film roller is properly
secured onto the film driver, and
the film is being unwound.
iii)
Check product sensor for
obstruction, cleanliness and
function.
Cut sleeve too short
after initial setting
i)
Material unwind under
tension.
ii)
Layflat material too tight on
the mandrel
iii)
Sensor adjustment
i)
Check full spool unwind system
for obstruction or excessive
friction. Check for correct slack
web in material full spool reservoir.
ii)
Check film sizes and tolerances
and retry cut/feed further along
reel OR replace reel.
iii)
Adjust film sensor, make sure the
photo eye is positioned in places
where the printing and clear area
of the film is clearly visible.
Cut sleeve too long OR
keeps feeding
i)
Sensor adjustment.
ii)
Sensor malfunctioning .
iii)
P.L.C error signaling.
iv)
Logic card faulty.
i)
Adjust film sensor, make sure
photo eye is not positioned in area
where there is no printing
ii)
Reset sensor, if faulty, replace with
a new one.
iii)
Check input signal.
iv)
If necessary, replace a new logic
Summary of Contents for NSV-400
Page 3: ...4 1 3 BASIC BLUEPRINTS...