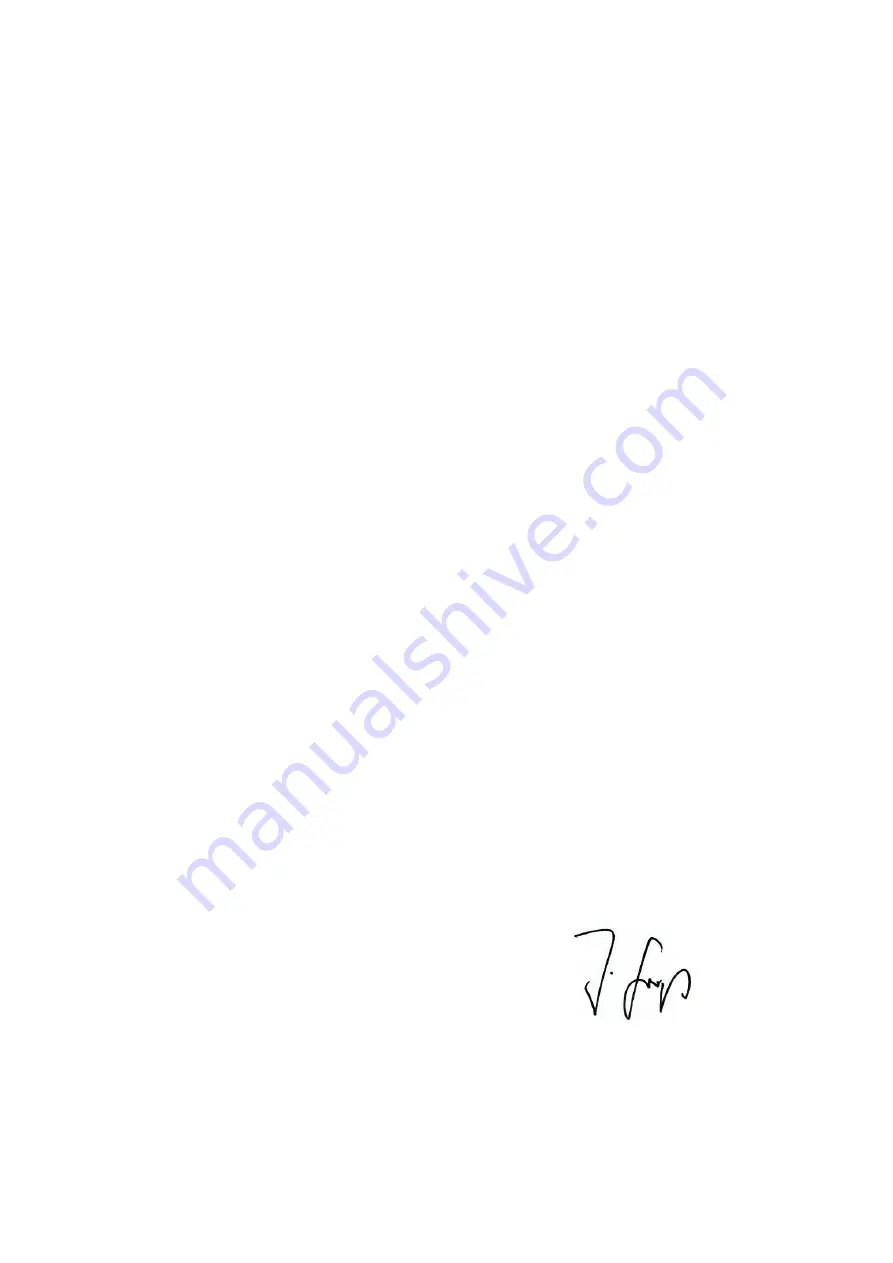
Declaration of Incorporation/Installation
According to Appendix II of the EU Machinery Directive 2006/42/EC
The manufacturer:
DewertOkin GmbH
Weststraße 1
32278 Kirchlengern
Germany
declares that the incomplete machines described below
DD11 System
DD21 System
complies with the following basic requirements of the Machinery Directive (2006/42/EC):
Sections:
1.1.3; 1.3.3; 1.3.4; 1.3.7; 1.5.1; 1.5.2; 1.5.5; 1.5.6; 1.5.7; 1.5.8;
1.5.9; 1.5.10; 1.5.13
According to
DIN EN 527-1:2011
DIN EN 527-2:2017
You may only operate this incomplete machine after you have confirmed that the end product (into
which this machine will be installed) complies with the Machinery Directive 2006/42/EC.
On request, the manufacturer is obliged to send the special documentation accompanying the
partially completed machinery in electronic form to the appropriate national institution. The special
technical documents corresponding to the machine have been created according to Appendix VII,
part B.
The following person is responsible for the technical documentation:
Silvio Wauro,
Address cited above
Phone.: +49 5223 979-0
Kirchlengern, Germany. November 12, 2018
Dr.-Ing. Josef G. Groß
Managing Director