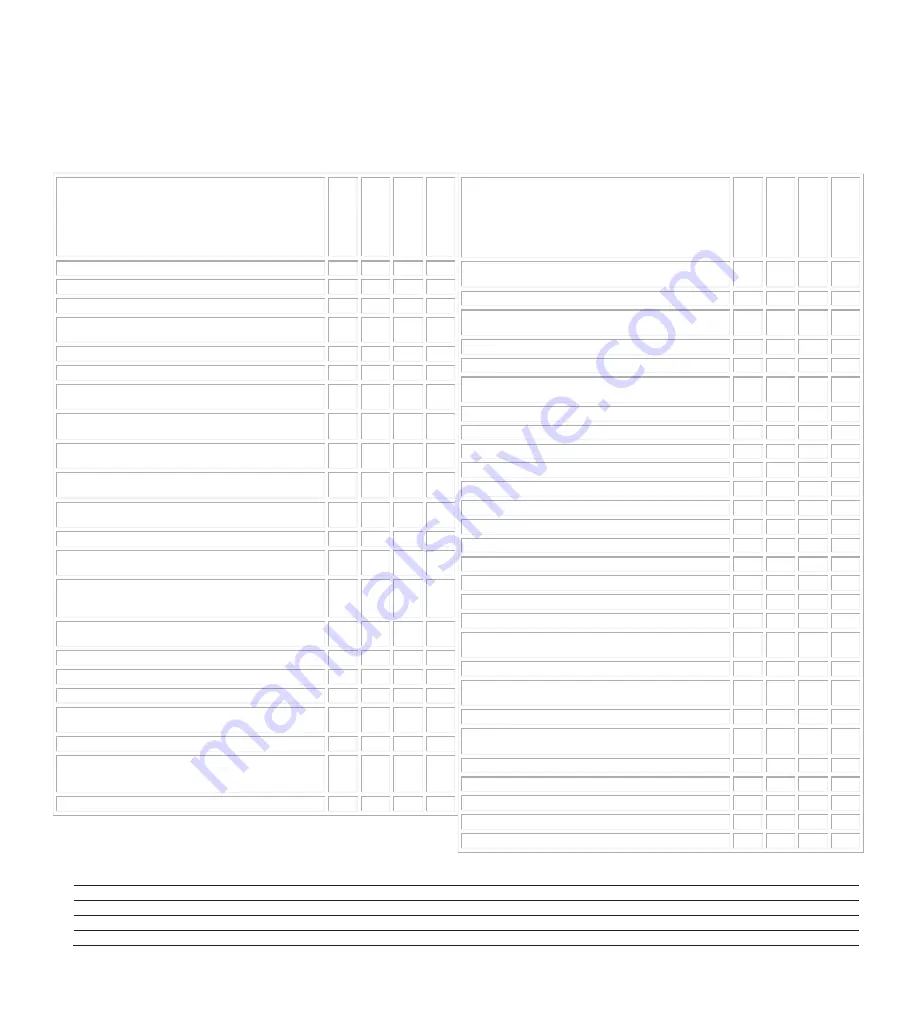
PIVIN & DRAPEAU inc.
26/27
5. INSPECTION REPORT
Model :
BCSI
__ ; Date : _________________ ; Page __ / __ ;
Technician : _________________ ; O.T. : __________ ; Gate serial # : ______________ ; # operations : _________ ;
Client name : ______________________ ; Gate localisation : ___________________________________________ ;
* :
√
– Immediate authorisation of works and repaired;
R
– refusal;
Q
– quote.
Notes
:
Technician signature: ________________________________ ; Client signature : ________________________________________
Notes
:
Conf. (
√
) \
Non-conf. (
N
)
C
orrect
ed
*
N / A (
√
)
See notes (
√
)
A – MECHANICAL PARTS INSPECTION
A1 – Operator concrete base : cracks, movement, stability
A2 – Operator anchors : tighten nuts
A3 – Reducer : oil level and leakage, play in the reducer,
crack in the box
A4 – Pulleys: fitting on the shaft, wear, pulleys alignment
A5 – Belts A34 : replacement, tension adjustment
A6 – Springs-system base plate hinge to operator frame :
bearing bushing (maximum play 0.010”)
A7 – Springs-system hinge to levers : bearing bushing
(maximum play 0.010”)
A8 – Connecting rod hinge to connecting rod lever :
bearing bushing (maximum play 0.010”)
A9 – Connecting rod hinge to torque limiter : bearing
bushing (maximum play 0.010”)
A10 – Spring sliding plate bearing bushing : maximum
play 0.010”
A11 – Connecting rod : deformation, cracks
A12 – Connecting rod lever : deformation, cracks. Tighten
the
5/8”
nuts to
250 lbs·ft ,
gradually and alternatively
A13 – Springs-system levers : deformation, cracks.
Tighten the ½” nuts to
160 lbs·ft,
gradually and
alternatively
A14 – Main shaft levers : deformation, cracks. Tighten the
3/8” nuts to
55 lbs·ft,
gradually and alternatively.
A15 – Springs system : deformation, cracks
A16 – Springs : cracks, rupture.
A17 – Operator frame : deformation, cracks, corrosion
A18 – Doors and covers : deformation, insulating material,
proper functioning of locks
A19 – Driving arm : deformation, cracks, corrosion
A20 – Driving arm : tighten the nuts following these :
½"
to
75 lbs·ft
with the gate and
¾”
to
380 lbs·ft
with the
operator
A21 – Gate : structure, fence, nuts, gate path
Notes
:
Conf. (
√
) \
Non-conf. (
N
)
C
orrect
ed
*
N / A (
√
)
See notes (
√
)
A22 – Springs : make adjustments to equilibrate the gate at
45°
A23 – Limit switches cams : make
adjustments
A24 – Connecting rod : adjust the nut to level the gate.
Tighten the jam nuts.
A25 – Torque limiter : adjust
B – ELECTRICAL COMPONENTS INSPECTION
B1 – Electrical panel : voltages, check wires connections,
proper behaviour of components
B2 – Electrical motor : proper operation, installation
B3 – Crank switch : proper operation, installation
B4 – Limit switches : proper operation, installation
B5 – Heating element and thermostat : proper behaviour
B6 – Sound alarm : proper operation
B7 – Safety edge : proper operation
C – LUBRICATION
C1 – Antifriction bearings on main shaft : lubricate
C2 – Antifriction bearing on torque limiter shaft : lubricate
C3 – Springs-system columns : lubricate
C4 – Covers locks : lubricate
D – ACCESSORIES INSPECTION
D1 – Detection loops : insulation, electrical continuity and
proper behaviour
D2 – Electrical photocell : proper operation, adjustments
D3 – Pedestal : electromagnet operation, installation,
alignment with gate, base stability
D4 – Traffic lights : proper operation
D5 – Access system : proper operation, installation, base
stability
E – CLEANING AND TOUCH-UP
E1 – Cleaning : grease and oil surplus, dust
E2 – Touch-up
F – FINAL CHECK
F1 – Proper operation of gate system
Summary of Contents for BCSI
Page 17: ...17 27 Fig 3 1 1 Fig 3 1 2 Fig 3 1 3 ...
Page 38: ......
Page 39: ......
Page 40: ......
Page 41: ......