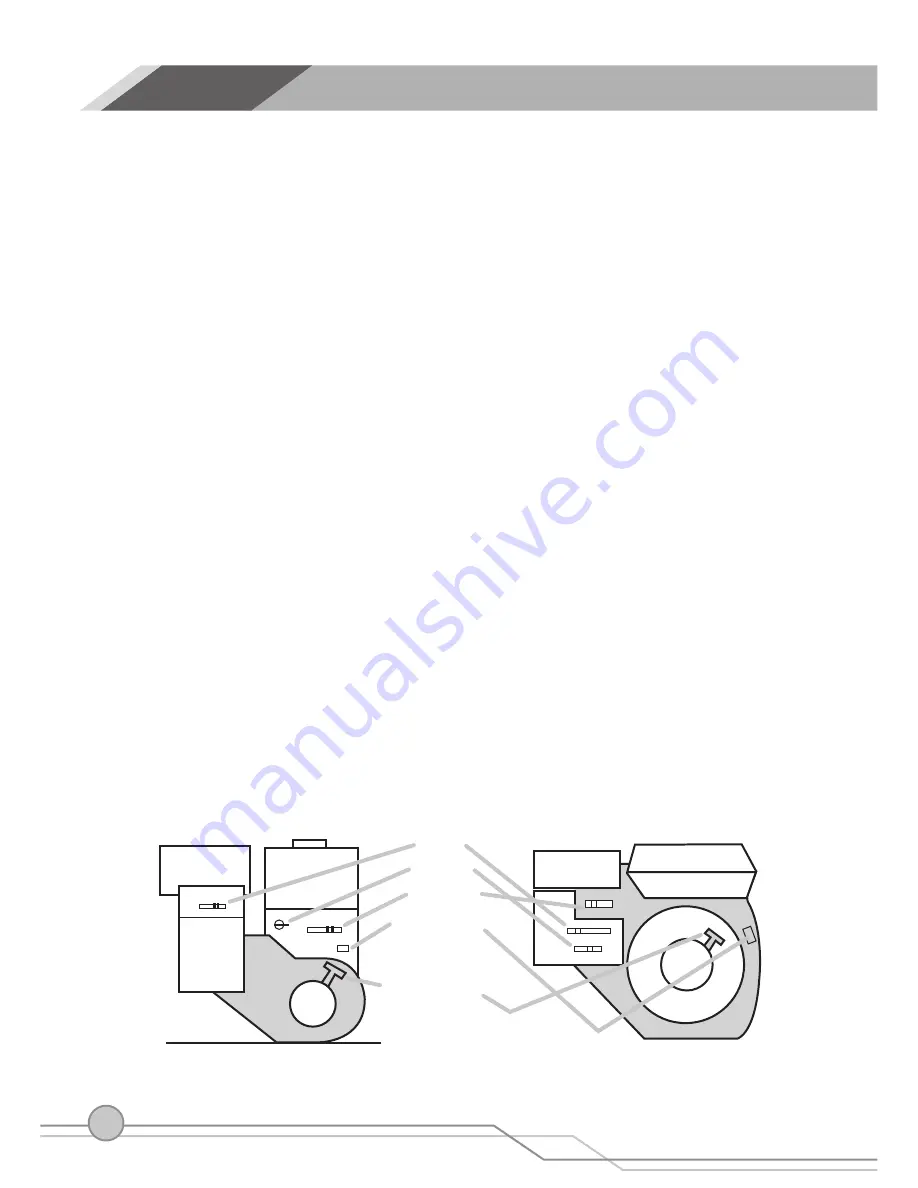
12
PRE-START CHECKS & STARTING
pre-sTarT CheCKs
• Ensure you are wearing safety glasses and hearing protection.
• Avoid wearing loose fitting clothing.
• Place the machine on a level ‘dirt or grass’ surface.
• Check that all fasteners on the machine are secure and all guards are in place.
• Check engine oil level.
• Ensure the hopper and the chipping chamber are clear.
• Keep bystanders away.
• Follow safety instructions (page 9) when filling the fuel tank.
1. Disengage the clutch. Push the lever fully down..
2. Turn the fuel tap to ‘ON’.
3. Switch on the ignition.
4. Push the throttle lever to ‘FAST’. (Rabbit)
5. Move the choke control to ‘CHOKE’.( Generally not necessary if the engine is hot.)
6. Stand facing the engine control panel and to the right of the panel. With your left hand
holding the top of the hopper and your right hand holding the starting cord handle, swiftly pull
the starting handle to the right. Repeat until the engine starts. If the engine seems to be flooded,
you may need to try a few pulls of the starter with the choke fully off.
7. As soon as the engine fires, start reducing the choke setting.
8. Once the engine sounds stable, and the choke is fully off, slowly raise the clutch lever until
it reaches the end of its stroke.
9. Check that the rotor is spinning by looking down inside the hopper. If it is not spinning,
maintenance is required. (See ‘Maintenance’ section - page 15).
10. Reduce the throttle setting to the position you need for effective machine operation. Large
diameter branches or a heavy shredding load will require full throttle.
imporTanT: The clutch is fitted to make starting easier. it may not fully disengage the drive
to the rotor, especially when the drive belt is new. neVer rely on the clutch to disengage the
drive.
sTarTinG (see engine diagram below)
Control Panel Layout (B&S)
Control Panel Layout (Honda)
CHOKE
FUEL TAP
THROTTLE
ON-OFF SWITCH
STARTER HANDLE
6.0
Summary of Contents for GARDEN CHIPPER 750
Page 1: ...Operation and Maintenance Manual www deutschermowers com au GARDEN CHIPPER 750 DEUTSCHER...
Page 2: ......
Page 4: ......
Page 23: ...NOTES...