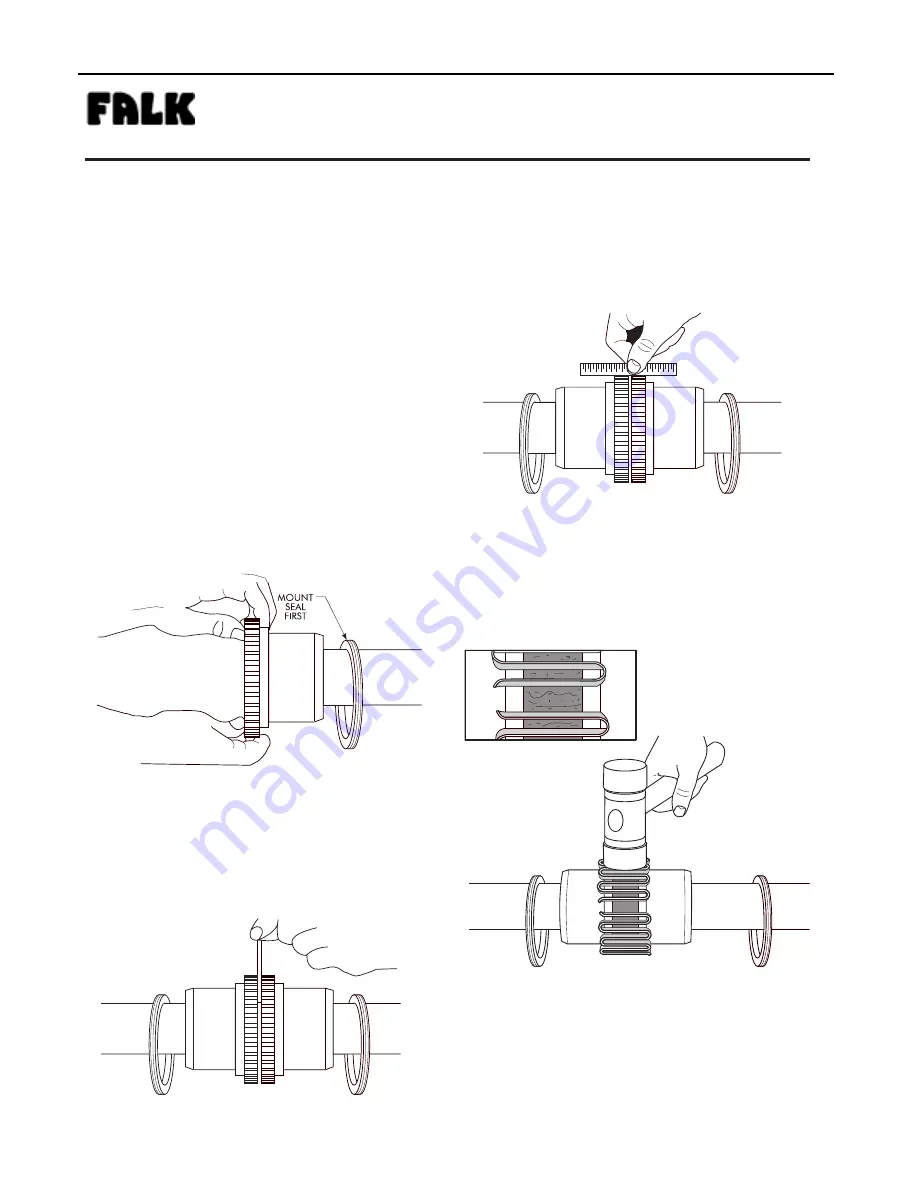
DDFP
WARNING:
If an oil bath is used, the oil must have a flash
point of 350˚F (177˚C) or higher. Do not rest hubs on the
bottom of the container. Do not use an open flame in a
combustible atmosphere or near combustible materials.
Heat hubs as instructed above. Mount hubs as quickly as possible
with hub flange face flush with shaft end. Allow hubs to cool before
proceeding. Insert setscrews (if required) and tighten.
Maximize Performance And Life
The performance and life of couplings depend largely upon
how you install and maintain them. Before installing couplings,
make certain that foundations of equipment to be connected
meet manufacturersí requirements. Check for soft foot. The use
of stainless steel shims is recommended. Measuring
misalignment and positioning equipment within alignment
tolerances is simplified with an alignment computer. These
calculations can also be done graphically or mathematically.
Alignment is shown using spacer bar and straight edge. This
practice has proven to be adequate for many industrial
applications. However, for superior final alignment, the use of
dial indicators (see Manual 458-834 for instructions), lasers,
alignment computers or graphical analysis is recommended.
1 — Mount Seals And Hubs
Lock out starting switch of prime mover. Clean all metal parts
using a non-flammable solvent. Lightly coat seals with grease
and place on shafts BEFORE mounting hubs. Heat interference
fit hubs as previously instructed. Seal keyways to prevent
leakage. Mount hubs on their respective shafts so the hub face
is flush with the end of its shaft unless otherwise indicated.
Tighten setscrews when furnished.
2 — Gap and Angular Alignment
Use a spacer bar equal in thickness to the gap specified in
Table 2, Page 5. Insert bar as shown below left, to same depth
at 90˚intervals and measure clearance between bar and hub
face with feelers. The difference in minimum and maximum
measurements must not exceed the ANGULAR installation limits
specified in Table 2.
3 — Offset Alignment
Align so that a straight edge rests squarely (or within the limits
specified in Table 2) on both hubs as shown above and also at
90˚intervals. Check with feelers. The clearance must not
exceed the PARALLEL OFFSET installation limits specified in
Table 2. Tighten all foundation bolts and repeat Steps 2 and 3.
Realign coupling if necessary.
4 — Insert Grid
Pack gap and grooves with specified lubricant before inserting grid.
When grids are furnished in two or more segments, install them so
that all cut ends extend in the same direction (as detailed in the
exploded view picture above); this will assure correct grid contact
with non-rotating pin in cover halves. Spread the grid slightly to
pass over the coupling teeth and seat with a soft mallet.
Type T10
•
Sizes 1020 –1140 & 20–140 (Page 3 of 6)
Steelflex ® Couplings
•
Installation and Maintenance
®
a good name in industry
Page 42
SECTION 3.6