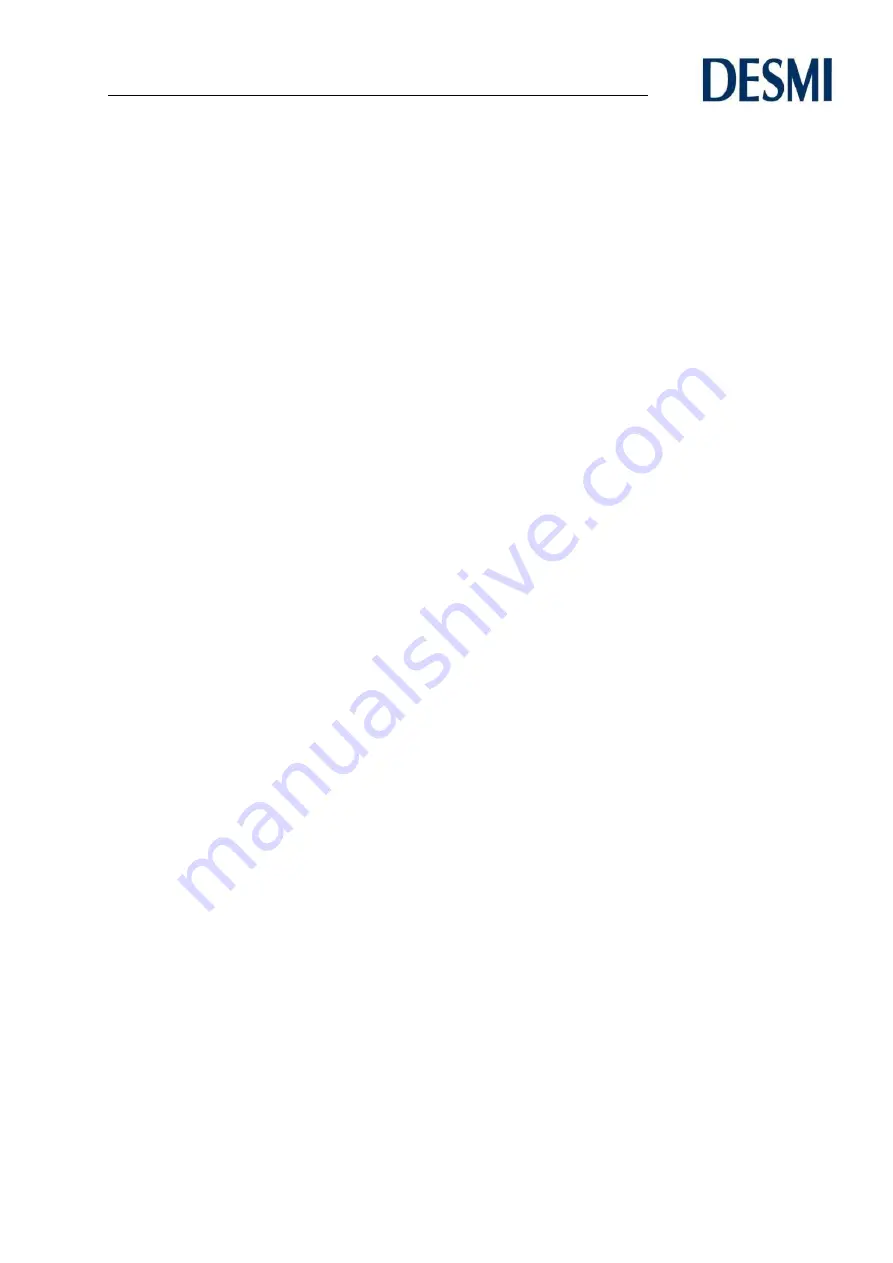
INSTALLATION
DESMI Pumping Technology A/S
Tagholm 1
9400 Nørresundby
– Denmark
Tlf. nr.: +45 96 32 81 11
Fax +45 98 17 54 99
45
E-mail: [email protected] www.desmi.com
Bypass
The pump must not run against a closed valve as this will cause a rise in temperature / formation
of steam in the pump which may cause damage to the pump.
If there is any special design of the pump running against a closed valve, ensure a minimum liquid
flow through the pump by connection of a bypass or drain to the outlet pipe. The minimum flow
rate must be at least 30% of maximum flow rate for short term operation, the flow rate and head
are stated on the pump name plate.
Note:
Operation outside 70 to 120 % of BEP flow reduce the
pump life (incl. shaft seal and pump bearings) significantly.
Allowable vibration levels on the pumps
As standard, DESMI centrifugal pumps with electric motor generate less than 2.8 mm/s vibration
velocity (measured in 3 directions at motor flange level on vertical pumps) during a factory test.
The pump and electric motor industry generally agrees that vibration levels above 7 mm/s are
damaging
– i.e. this will result in shorter lifetimes of e.g. bearings and/or shaft seals in pumps (and
bearings in motors) than normally expected. This agrees with the recommendations in the
international standard ISO10816-3.
Vibration prevention on vertical Pumps installed on ships.
High vibration levels at pump / motor top is a well-known issue in vertical pumps installed on ships.
Often external excited vibrations combined with the relative high Centre of Gravity compared with
the size of the pump baseplate and/or the foundation stiffness below result in too high vibration
levels in pump and motor top.
I.e. it is normally not the vibrations induced by the motor and/or the pump itself that causes problems
(except if the pump or motor has mechanical problems and/or the pump is running with much higher
flow than it is designed for
– this can cause so high turbulence levels in pump and piping system
that excessive vibrations occur).
Changing the structure can minimize the vibration level significantly - either by reinforcing the
foundation stiffness below the base plate of the pump and/or by adding lateral supports at pump top
/ motor mounting flange level (the lateral supports will typically be the cheapest/fastest/easiest
solution).
Whether this should be a rigid or a flexible support is not easy to determine since this depends on
the actual installation and the available fixing points in the vessel.
In cases where the lateral supports are transferring hull vibrations (e.g. from main engine in ship) to
the support connection points on pump or motor then a flexible element can then be added for
Summary of Contents for NSL 100-215
Page 2: ......