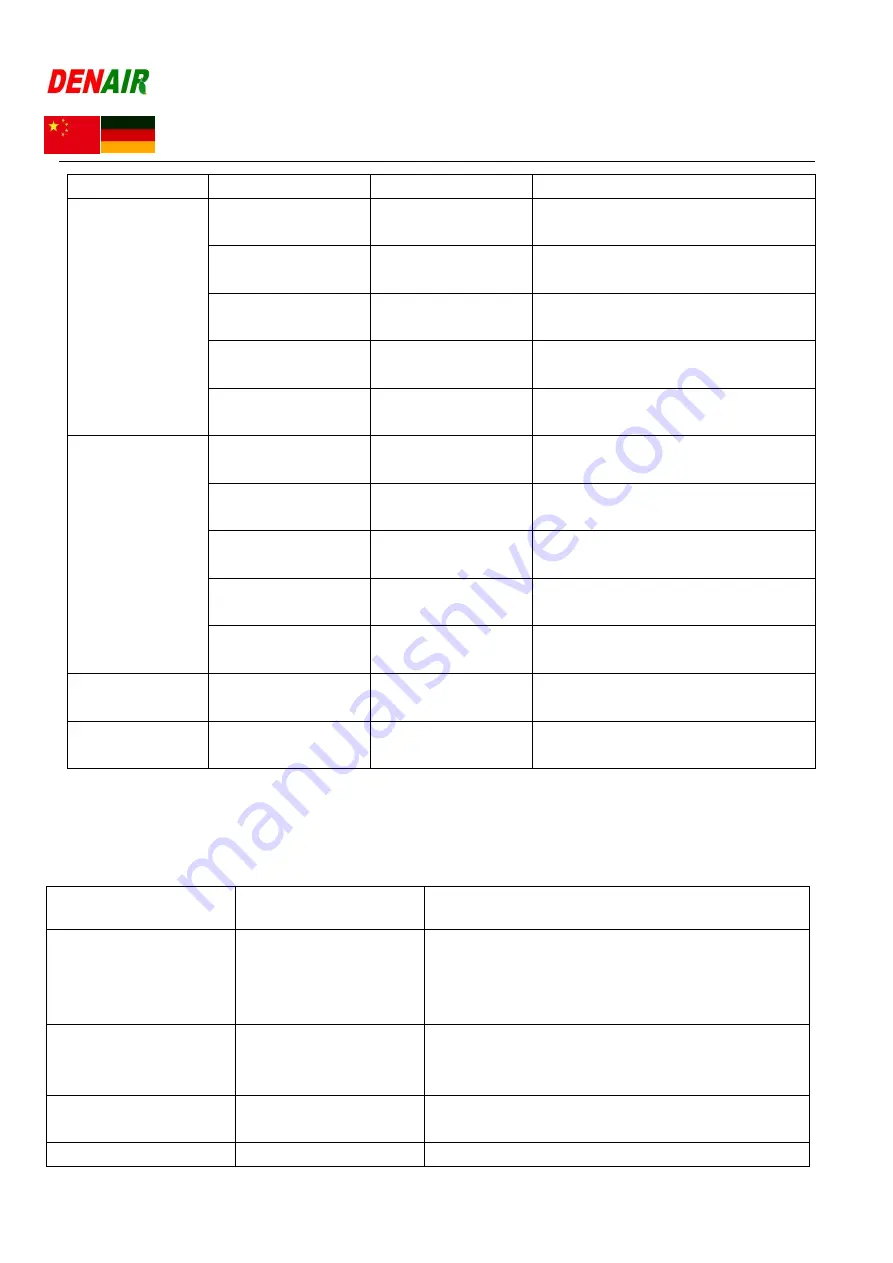
Shanghai Denair Compressor Co.,Ltd.
www.denaircompressor.net 14/48
Ganged delay time
0000second
Oil filter reset
0000 hour
Replacing oil filter could clear service
time
Olein differentiator
reset
0000 hour
Replacing olein differentiator to
clear service time
Air filter reset
0000 hour
Replacing air filter to clear service
time
Lubricating oil reset
0000 hour
Replacing lubrication oil to clear service
time
Maintenance
parameter reset
Lubricating grease
reset
0000 hour
Replacing lubricating grease to
clear service time
Oil filter
9999 hour
Set as
“
0
”
,
the time early warning of
oil filter is useless
Olein differentiator
9999 hour
Set as
“
0
”
,
the time early warning of
oil differentiator is useless
Air filter
9999 hour
Set as
“
0
”
,
the time early warning of
air filter is useless
Lubricating oil
9999 hour
Set as
“
0
”
,
the time early warning of
lubricating oil is useless
Max service time
preset
Lubricating grease
9999 hour
Set as
“
0
”
,
the time early warning of
lubricating grease is useless
Chinese-English
choice
Chinese
Set as
“
English
”
, the interface turns
into English operation
Alter user
password
****
User can alter password
C. Manufacturer Parameter
The difference between manufacturer parameter and user parameter is that manufacturer parameter can’t be
checked and should be altered just according to the manufacturer password, and the altering operation method is
the same with that of user parameter. As for its main functions, please refers to the below chart:
Parameter item
Set initial value
Functions
Air-end rated current
Motor ‘s allowed
maximum overload
value
1.2
╱
After start delaying
,
When the motor current value
greater than 1.2 times and below 4 times that of set
value
,
please delay the machine jumping according
to overload characteristic.
Fan rated current
Motor ‘s allowed
maximum overload
value
1.2
╱
ditto
Exhaust early warning
temperature.
105
℃
When the actual exhaust temperature higher than
他
the set temperature
,
prompt warning.
exhaust early warning
110
℃
When the actual exhaust temperature higher than