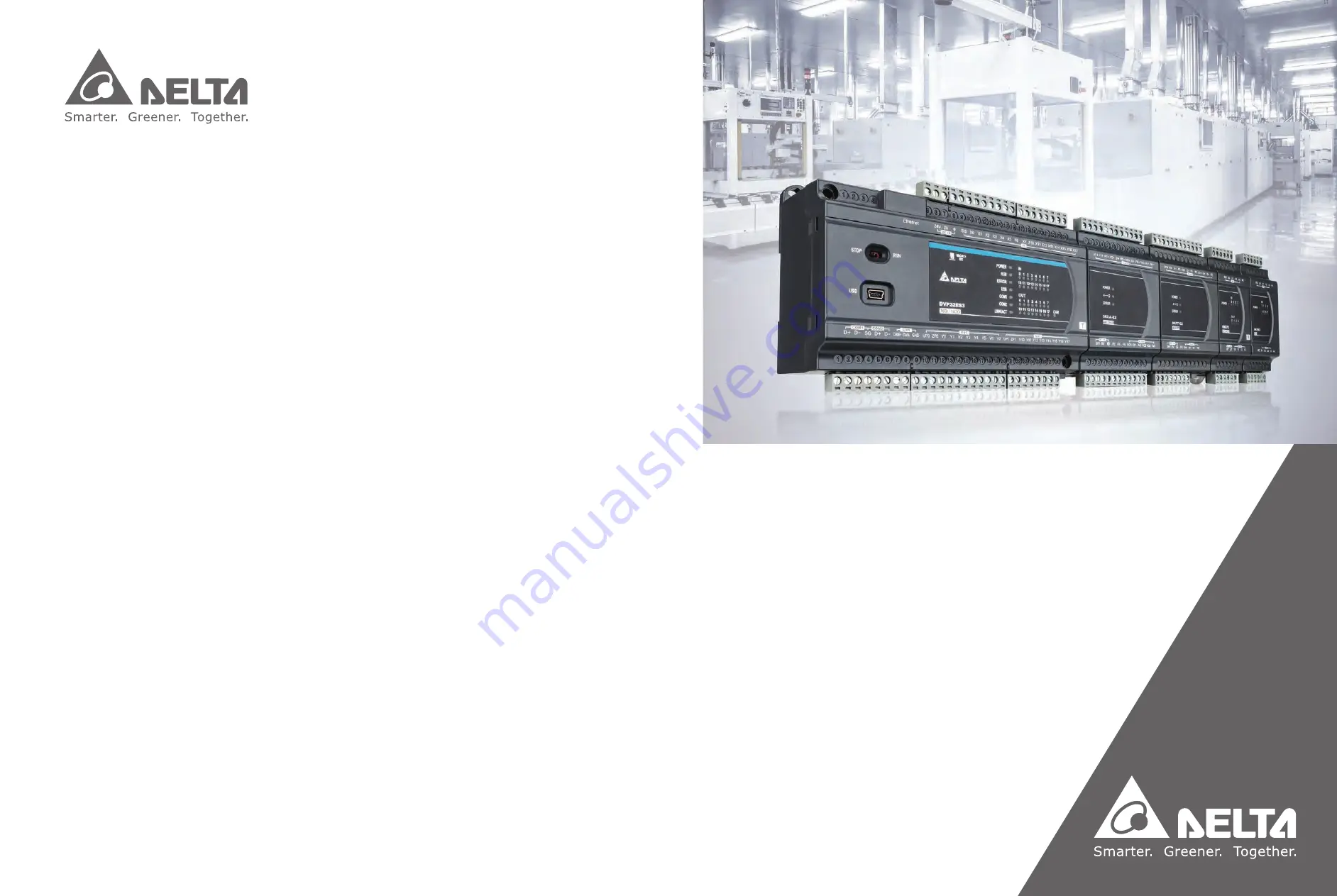
www.deltaww.com
Industrial Automation Headquarters
Delta Electronics, Inc.
Taoyuan Technology Center
No.18, Xinglong Rd., Taoyuan District,
Taoyuan City 33068, Taiwan
TEL: 886-3-362-6301 / FAX: 886-3-371-6301
Asia
Delta Electronics (Shanghai) Co., Ltd.
No.182 Minyu Rd., Pudong Shanghai, P.R.C.
Post code : 201209
TEL: 86-21-6872-3988 / FAX: 86-21-6872-3996
Customer Service: 400-820-9595
Delta Electronics (Japan), Inc.
Tokyo Office
Industrial Automation Sales Department
2-1-14 Shibadaimon, Minato-ku
Tokyo, Japan 105-0012
TEL: 81-3-5733-1155 / FAX: 81-3-5733-1255
Delta Electronics (Korea), Inc.
Seoul Office
1511, 219, Gasan Digital 1-Ro., Geumcheon-gu,
Seoul, 08501 South Korea
TEL: 82-2-515-5305 / FAX: 82-2-515-5302
Delta Energy Systems (Singapore) Pte Ltd.
4 Kaki Bukit Avenue 1, #05-04, Singapore 417939
TEL: 65-6747-5155 / FAX: 65-6744-9228
Delta Electronics (India) Pvt. Ltd.
Plot No.43, Sector 35, HSIIDC Gurgaon,
PIN 122001, Haryana, India
TEL: 91-124-4874900 / FAX : 91-124-4874945
Delta Electronics (Thailand) PCL.
909 Soi 9, Moo 4, Bangpoo Industrial Estate (E.P.Z),
Pattana 1 Rd., T.Phraksa, A.Muang,
Samutprakarn 10280, Thailand
TEL: 66-2709-2800 / FAX : 662-709-2827
Delta Energy Systems (Australia) Pty Ltd.
Unit 20-21/45 Normanby Rd., Notting Hill Vic 3168, Australia
TEL: 61-3-9543-3720
Americas
Delta Electronics (Americas) Ltd.
Raleigh Office
P.O. Box 12173, 5101 Davis Drive,
Research Triangle Park, NC 27709, U.S.A.
TEL: 1-919-767-3813 / FAX: 1-919-767-3969
Delta Greentech (Brasil) S/A
São Paulo Office
Rua Itapeva, 26 – 3˚ Andar - Bela Vista
CEP: 01332-000 – São Paulo – SP - Brasil
TEL: 55-11-3530-8642 / 55-11-3530-8640
Delta Electronics International Mexico S.A. de C.V.
Mexico Office
Vía Dr. Gustavo Baz No. 2160, Colonia La Loma,
54060 Tlalnepantla Estado de Mexico
TEL: 52-55-2628-3015 #3050/3052
*We reserve the right to change the information in this manual without prior notice.
EMEA
Headquarters:
Delta Electronics (Netherlands) B.V.
Sales: [email protected]
Marketing: [email protected]
Technical Support: [email protected]
Customer Support: [email protected]
Service: [email protected]
TEL: +31(0)40 800 3800
BENELUX:
Delta Electronics (Netherlands) B.V.
De Witbogt 20, 5652 AG Eindhoven, The Netherlands
Mail: [email protected]
TEL: +31(0)40 800 3800
DACH:
Delta Electronics (Netherlands) B.V.
Coesterweg 45, D-59494 Soest, Germany
Mail: [email protected]
TEL: +49(0)2921 987 0
France:
Delta Electronics (France) S.A.
ZI du bois Challand 2, 15 rue des Pyrénées,
Lisses, 91090 Evry Cedex, France
Mail: [email protected]
TEL: +33(0)1 69 77 82 60
Iberia:
Delta Electronics Solutions (Spain) S.L.U
Ctra. De Villaverde a Vallecas, 265 1º Dcha Ed.
Hormigueras – P.I. de Vallecas 28031 Madrid
TEL: +34(0)91 223 74 20
Carrer Llacuna 166, 08018 Barcelona, Spain
Mail: [email protected]
Italy:
Delta Electronics (Italy) S.r.l.
Ufficio di Milano Via Senigallia 18/2 20161 Milano (MI)
Piazza Grazioli 18 00186 Roma Italy
Mail: [email protected]
TEL: +39 02 64672538
Russia:
Delta Energy System LLC
Vereyskaya Plaza II, office 112 Vereyskaya str.
17 121357 Moscow Russia
Mail: [email protected]
TEL: +7 495 644 3240
Turkey:
Delta Greentech Elektronik San. Ltd. Sti. (Turkey)
Şerifali Mah. Hendem Cad. Kule Sok. No:16-A
34775 Ümraniye – İstanbul
Mail: [email protected]
TEL: + 90 216 499 9910
GCC:
Delta Energy Systems AG (Dubai BR)
P.O. Box 185668, Gate 7, 3rd Floor, Hamarain Centre
Dubai, United Arab Emirates
Mail: [email protected]
TEL: +971(0)4 2690148
Egypt + North Africa:
Delta Electronics
511 Cairo Business Plaza, North 90 street,
New Cairo, Cairo, Egypt
Mail: [email protected]
DVP-ES3
Series
Operation Manual
D
VP-ES3
Series Operation Manual
DVP-0289420-01
2019/0
9
/
0
5
Summary of Contents for DVP-ES3 Series
Page 26: ...DVP ES3 Series Operation Manual 1 14 _1 MEMO ...
Page 232: ...DVP ES3 Series Operation Manual 8 28 _8 MEMO ...
Page 385: ...DVP ES3 Series Operation Manual 13 8 _13 MEMO ...
Page 399: ...DVP ES3 Series Operation Manual B 4 _ B MEMO ...