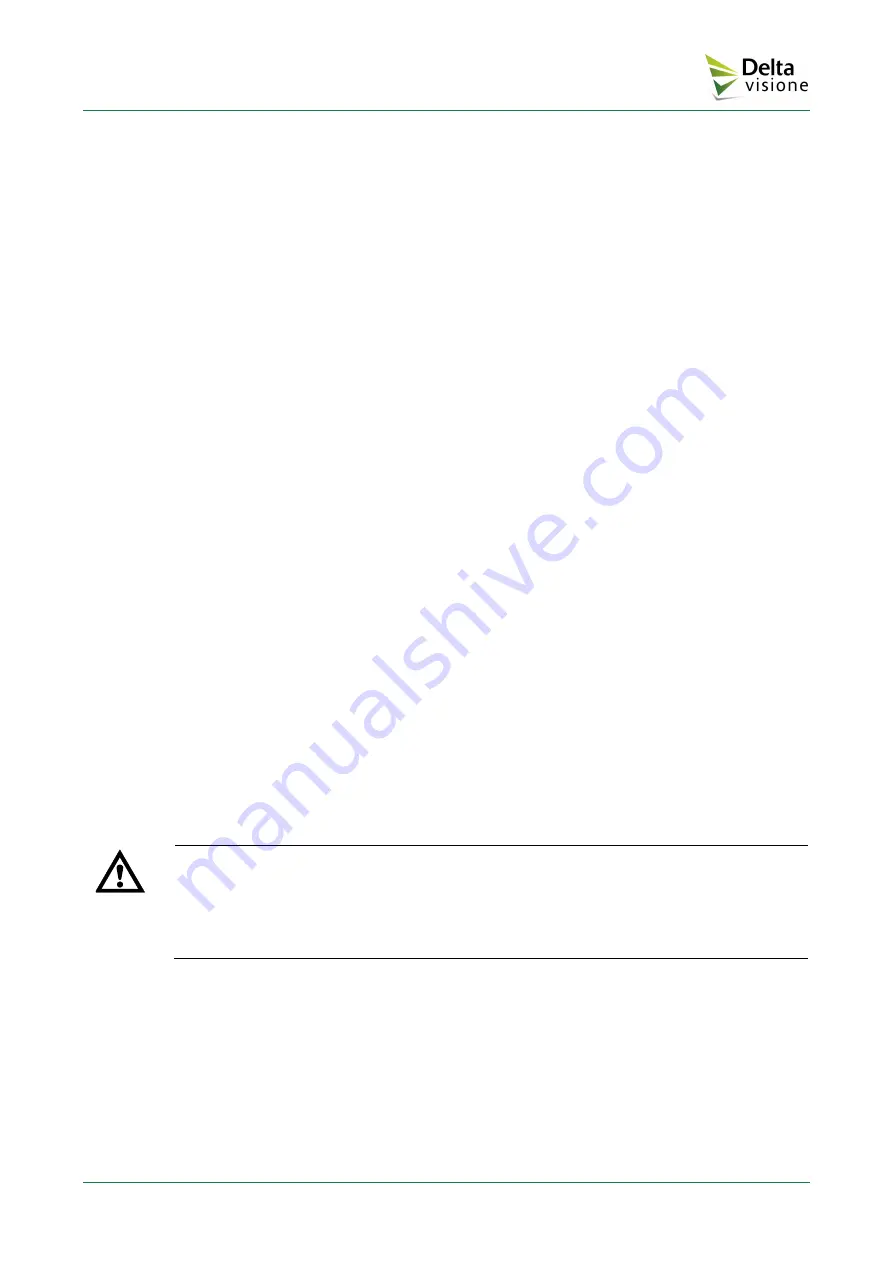
DEV7
– Use and Maintenance Manual
Pag. 21
Integration
Integration of the marking machine in the line or work bench is indispensable in order to put it into
operation.
The machine must be set on a flat surface to ensure accurate marking.
There must be sufficient space around the machine for the operator to move easily during normal
operation and routine maintenance, as well as adequate natural lighting
.
Lighting
As the marking machine can operate under normal lighting conditions, there is no need to add any other
light sources to the natural lighting of the work environment.
Protective devices
The particular intended use of the machine and the problems posed by the variety of the parts to be
marked do not allow the type of protection to be defined in advance. It is therefore pointed out that:
All additional
protections, external drives and integration devices are the user’s respon
sibility. It
is therefore strictly prohibited to use the machine without integrating it properly into the
operating environment in accordance with the legislation in force
.
Noise
The DEV7 marking machine was designed in such a way as to reduce to a minimum the sound emissions
caused by the movement and drives of the punch. The system is however used for marking parts whose
shape and material may vary considerably and so its noise emissions therefore also vary.
It is not possible to determine, unambiguously and in a way that is valid for all the applications,
the A-weighted emission sound pressure level, nor the peak C-weighted instantaneous sound
pressure value, nor the A-weighted sound power level emitted by the machinery
.
When the machine is integrated in a production line, or work bench or in a machine complying with
Machine Directive 2006/42/CE, it is the responsibility of the integrator to undertake appropriate
measures for reducing noise within the permissible limits or for the measurement of pressure and sound
power levels. Following these assessments, it will be possible to determine if and what types of personal
protective equipment for hearing should be worn by the operators.
A T T E N T I O N
It is mandatory that the operator uses additional personal protective equipment
against noise, in the case in which a prior integration of the system has not reduced
within the allowable limits the acoustic emissions from the machine during its
operation.
Summary of Contents for DEV7
Page 1: ...DEV7 Rel 4 1 27 12 2017 MarkingSystem DEV7 Useandmaintenancemanual ...
Page 2: ......
Page 6: ......
Page 20: ......
Page 28: ......
Page 30: ......
Page 39: ...DEV7 Use and Maintenance Manual Pag 37 Attachment 2 Pneumatic diagram ...
Page 40: ......
Page 42: ......
Page 44: ...DEV7 Use and Maintenance Manual Pag 42 ...
Page 45: ...DEV7 Use and Maintenance Manual Pag 43 ...
Page 46: ......
Page 47: ...DEV7 Use and Maintenance Manual Pag 45 Attachment 5 Exploded view drawings of punches ...