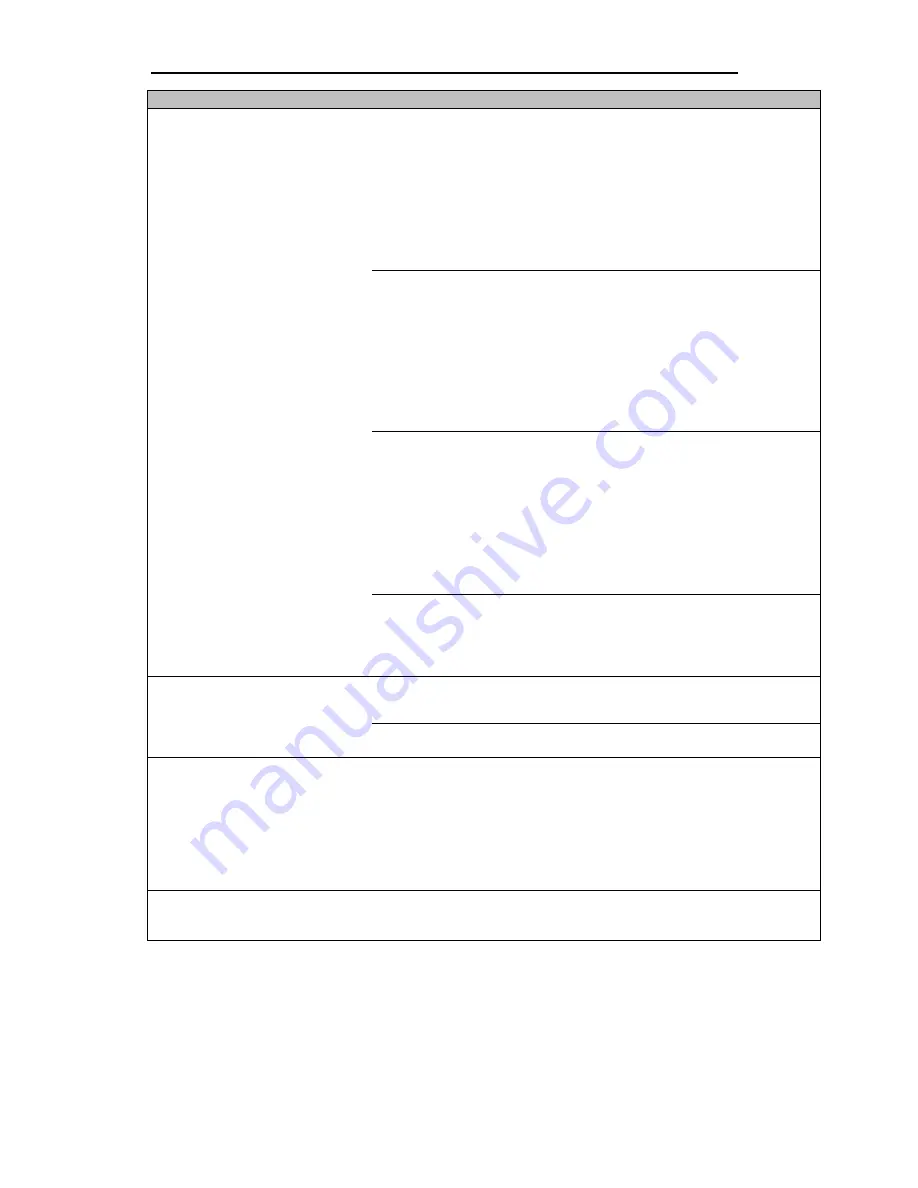
Delitek Waste Compactors – user -/service manual-rev 1.2
DT-200i “Green Ship” Waste Compactor – standard versions 34
Symptoms
Cause
Solution
The compaction force seems to
be insufficient or very low
(continued).
Blocked air-vent/wrong filler
cap.
On the hydraulic oil tank: please check
that the air vent/airing on the filling cap
is not blocked. A blocked air vent can
eventually cause the hydraulic system
to malfunction.
Alternatively, if the hydraulic oil tank
was delivered with an airtight
temporary filling cap; Replace this with
the original dipstick.
Hydraulic oil level is to low
Please ensure that the waste
compactor contains sufficient hydraulic
oil in the hydraulic oil tank found on
the hydraulic aggregate. The oil tank
must contain 3,2 liters hydraulic oil or
be 3/4 full (Univis 32). Check the oil
level by controlling the dipstick. The oil
level should be between 55mm and
65mm up on the dipstick.
Air pockets in the hydraulic
system
If the waste compactor/hydraulic
system has been forced to operate
with insufficient hydraulic oil level, air
pockets may have occurred in the
system. Check and refill oil as
described above. Start the waste
compactor and run the compaction
cycle a few times in order to
automatically empty the system for
entrapped air.
Compaction of solid waste
and waste with high density.
The compaction ratio will strongly
depend on what kind of waste is
compacted. Solid items of metal, wood
and plastic may have none or very low
compaction ratio.
The piston does not return to its
upper position (0-position)
Solenoid valve(s) or coils
may be defect
Coils or solenoid valves must be
replaced. Contact Delitek AS.
The switch on the press-plate
may be defect.
Contact Delitek As and have the
switch replaced.
The container is difficult to move
and maneuver.
Wheels may be defect
Control the wheels on the container,
and check that they are free rolling.
Contact Delitek As and have the
wheels replaced if some of them is
defect. Two of the wheels have
rotating action and two have fixed
direction.
The loading hatch refuse to rest in
open position
One or both of the gas
pistons on the hatch are
defect
Contact Delitek AS and order for spare
parts. See chapter. 8.