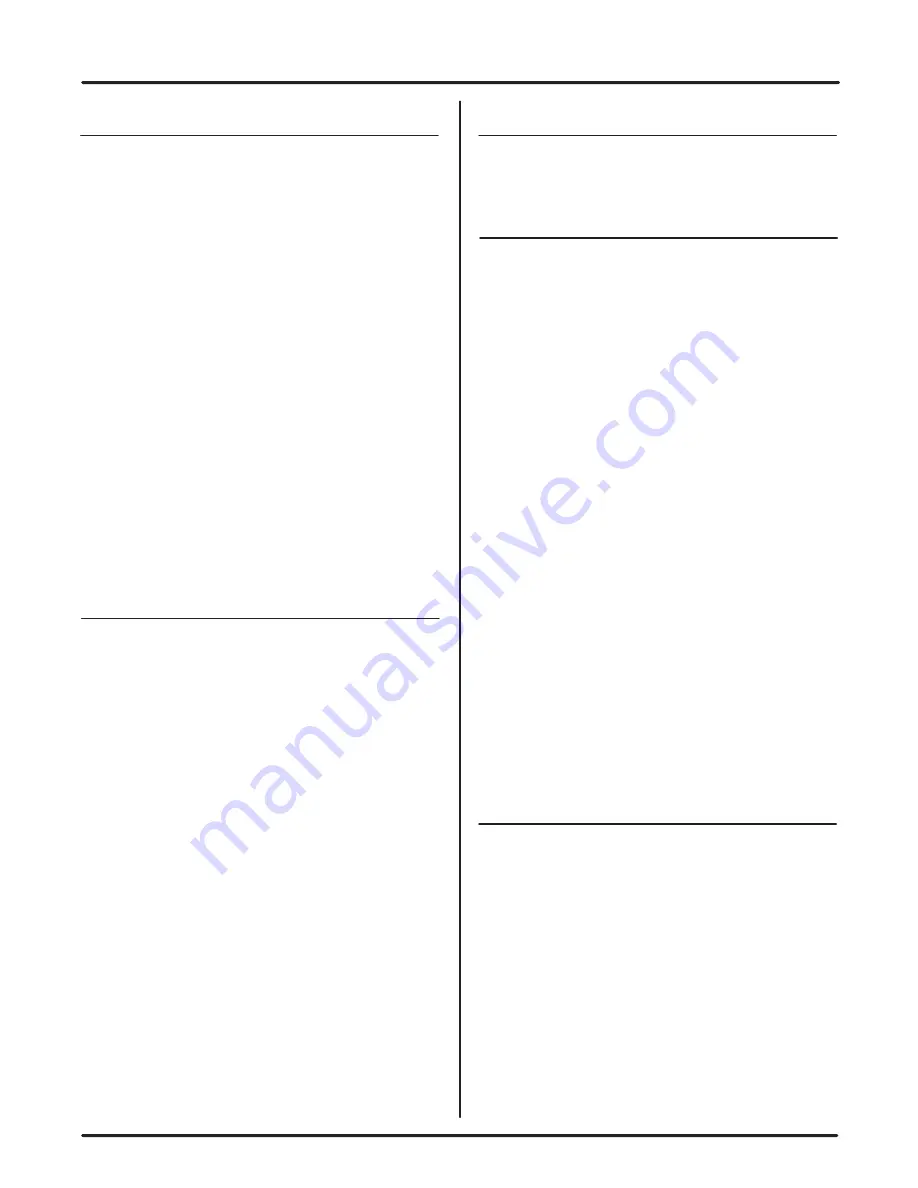
-11-
142664 - 5900 Series (24-November-2020)
TRANSPORTING
Follow this procedure when preparing to transport:
1. Clear the area of bystanders, especially small
children, before converting into transport
configuration.
2. Operate the lift hydraulics to raise the blade fully
and install a certified safety chain to secure it.
3. Clean the SMV sign, lights and reflectors.
4. Maintain a safe speed. Slow down when
cornering and on rough roads.
5. Slow down and pull off to the side of the road
when meeting other traffic.
6. Use hazard flashers on tractor unless prohibited
by law.
Transport & Storage
TRANSPORT SAFETY
• Read and understand ALL the information in the
Operator's Manual regarding procedures and
SAFETY when operating the machine in the field/
yard or on the road.
• Check with local authorities regarding machine
transport on public roads. Obey all applicable
laws and regulations.
• Always travel at a safe speed. Use caution when
making corners or meeting traffic.
• Make sure the SMV (Slow Moving Vehicle)
emblem and all the lights and reflectors that are
required by the local highway and transport
authorities are in place, are clean and can be
seen clearly by all overtaking and oncoming
traffic.
• Keep to the right and yield the right-of-way to
allow faster traffic to pass. Drive on the shoulder,
if permitted by law.
• Always use hazard warning flashers on tractor
when transporting, unless prohibited by law.
Decals, especially safety and reflective, should be
replaced when they become damaged or worn.
Contact your dealer.
Safety Decals
142386
Warning Decal, Falling Blade
2
Reflective Decals
142557
Amber Reflector, 2” x 9” lg
2
(located top front corners of blade)
142556
Red Reflector, 2” x 9” lg
2
142650
Fluorescent Reflector, 2” x 9” lg
2
Product Decals
142008
Degelman Logo, 25-3/4” lg
2
142780
5900 Blade Decal
1
REPLACEMENT DECALS
STORAGE
After the season's use, completely inspect all major
systems of the machine. Repair or replace any worn
or damaged components to prevent unnecessary
down time at the beginning of next season.
Since the unit can be used in extremely adverse
conditions during the season, the machine should be
carefully prepared for storage to ensure that all dirt,
mud, debris and moisture has been removed.
Follow this procedure when preparing to store:
1. Wash the entire machine thoroughly using a water
hose or pressure washer to remove all dirt, mud,
debris or residue.
2. Inspect all parts to see if anything has become
entangled in them. Remove the entangled
material.
3. Lubricate all grease fittings to remove any
moisture.
4. Inspect all hydraulic hoses, fittings, lines and
couplers. Tighten any loose fittings. Replace any
hose that is badly cut, nicked or abraded or is
separating from the crimped end of the fitting.
5. Touch up all paint nicks and scratches to prevent
rusting.
6. Oil the exposed rams on the hydraulic cylinder to
prevent rusting.
7. Select an area that is dry, level and free of debris.
STORAGE SAFETY
• Store unit in an area away from human activity.
• Do not permit children to play near the stored unit.