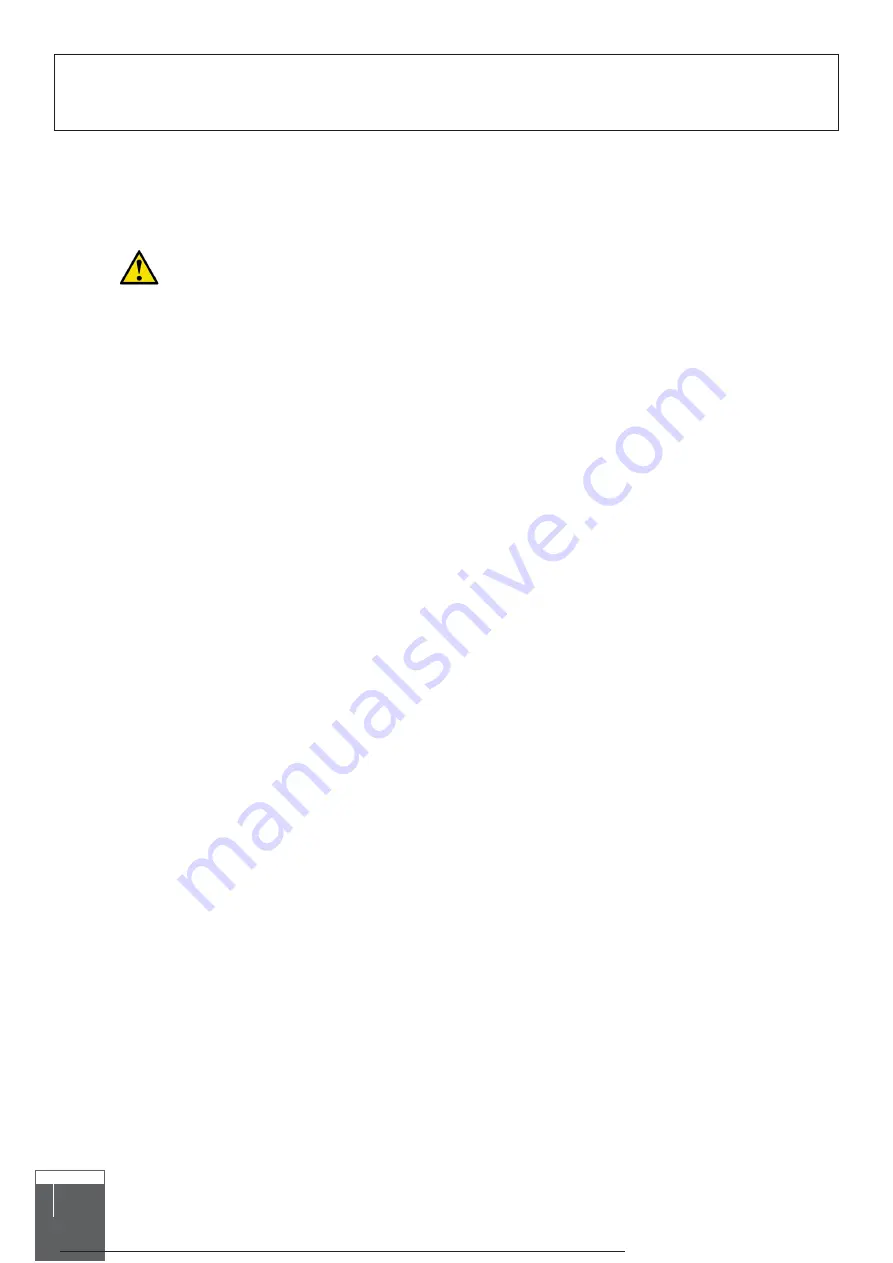
jaw should not move up and down. Fit the Cap Screw and tighten using a hexagonal wrench. Remember to
install the washers on these screws.
Changing the Hard Jaws – Moving (Cylinder) Side
Release the 8off Cap Screws that hold the Clamp Cylinder in place and remove the Clamp Cylinder. Undo
the two clamp supply hoses, carefully marking them to ensure correct re-assembly. Once removed, unscrew
the round Hard Jaw counter-clockwise and replace with a new one using a new O-ring. Ensure the Jaw is
fully tightened on the Clamp Cylinder piston rod so that the O-ring is no longer visible. Inspect the bronze
Guide Bush inside the Clamp Body whilst the cylinder is out – check the grooves in the front area of the
bush and the condition of the bore. Replace the bush if badly worn.
Assemble the Clamp Cylinder back into the Clamp Body, fit the clamp hoses then fit and tighten the Cap
Screws using the hexagonal wrench. Ensure the clamp functions correctly after completing the work.
h.
Inspect the rubber Sandwich Mounts (Elastomers) for wear or damage. Wear is typified by splitting/
tares. This usually occurs in the rubber adjacent to the bonded steel plates and is usually a result of
fatigue in the material over a long period of time. Crazing/softening may occur but this is usually
associated with long term exposure to sunlight or exposure to petroleum based products.
As a general rule change the Sandwich Mount if any single tare or split exceeds 40mm (1½”) or if
the rubber has become contaminated.
i.
Check the overall condition of the Swivel Assembly. Check that the Lifting Bolt and Nut (that are
the centre piece of this assembly) only allow rotational movement with minimal axial movement.
Excessive axial movement will allow the assembly to rattle around, make more noise and cause in
turn more wear. If the axial play exceeds 1mm it will be necessary to tighten the nut. To do this
remove the coil/spring pin with a punch and hammer, tighten the nut further and drill and pin it in
the new position.
j.
Check the condition of the boom Adaptor Bracket, Shear Pins, Spacers and Bushes. The whole
assembly should be relatively tight with minimal play in the components. The bracket needs to
be able to float a little from side to side – as much as 5/10 mm is acceptable. The pins and bushes
should however be little more than a running fit – clearances of more than 0.5mm would be
considered excessive.
excavator mounted vibrator
24
continued - maintenance
Summary of Contents for EMV 550
Page 2: ......
Page 4: ......
Page 34: ...parts lists for the emv550 www dcpuk com 34 ...
Page 41: ......
Page 44: ......
Page 46: ......
Page 48: ...appendix a auxiliary equipment ...
Page 50: ......
Page 56: ......