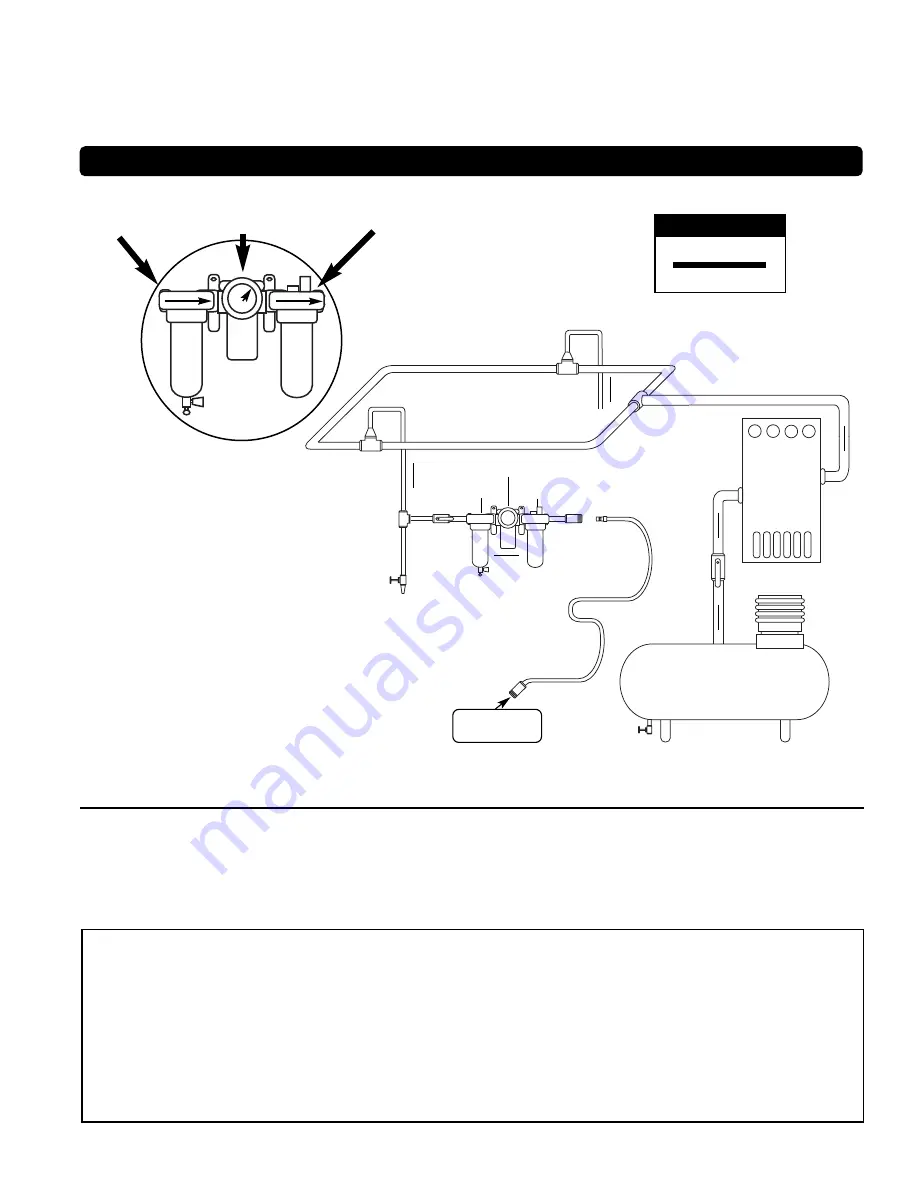
Notice
All Dynabrade motors use the highest quality parts and metals available and are machined to exacting tolerances. The failure of quality pneumatic motors can
most often be traced to an unclean air supply. Air pressure easily forces dirt or water contained in the air supply into motor bearings causing early failure. Dirt
and water often score the inner workings of the tool resulting in limited efficiency and power. Our warranty obligation is contingent upon proper use of our
tools and cannot apply to equipment which has been subjected to misuse such as unclean air, wet air or a lack of maintenance during the use of this tool.
3
Air System
•
Dynabrade Air Power Tools are designed to
operate at 90 PSIG (6.2 Bar/620 kPa) maximum
air pressure at the tool inlet, when the tool is
running. Use recommended regulator to control
air pressure at each work station, if the supply
pressure is high.
•
Ideally the air supply should be free from
moisture. To facilitate removing moisture
from air supply, the installation of a
refrigerated air dryer after the compressor
and the use of drain valves at each
tool station is recommended.
MAINTENANCE INSTRUCTIONS - CONTINUED
Handling and Storage:
•
Protect abrasive accessories from exposure to water, solvents, high humidity, freezing temperature and extreme temperature changes.
•
Store accessories in protective racks or compartments to prevent damage.
To Tool Station
Closed Loop Pipe System
Ball
Valve
Ball
Valve
Filter
Regulator
Lubricator
Air Flow
Drain
Valve
Drain
Valve
PSIG at Air Tool
Air Compressor
and Receiver
Drain
Valve
Air Hose
90 PSIG MAX
(6.2 Bar)
Air Flow
Refrigerated
Air Dryer
Filter
Regulator
Lubricator
90 PSIG
(6.2 Bar)
1
DROP/MIN.
20
SCFM
LUBRICATOR SETTING
➤
➤
➤
➤
➤
➤
Lifetime Warranty
All Dynabrade portable pneumatic power tools are rigorously inspected and performance tested in our factory before shipping to our customers. If
a Dynabrade tool develops a performance problem and an inherent defect is found during normal use and service, Dynabrade will warrant this tool
against defects in workmanship and materials for the lifetime of the tool. Upon examination and review at our factory, Dynabrade shall confirm that
the tool qualifies for warranty status, and will repair or replace the tool at no charge to the customer. Normally wearable parts and products are
NOT covered under this warranty. Uncovered items include bearings, contact wheels, rotor blades, regulators, valve stems, levers, shrouds,
guards, O-rings, seals, gaskets and other wearable parts. Dynabrade’s warranty policy is contingent upon proper use of our tools in accordance
with factory recommendations, instructions and safety practices. It shall not apply to equipment that has been subjected to misuse, negligence,
accident or tampering in any way so as to affect its normal performance. To activate lifetime warranty, customer must register each tool at
www.dynabrade.com. Dynabrade will not honor lifetime warranty on unregistered tools. A one-year warranty will be honored on all unregistered
portable pneumatic power tools. Lifetime warranty applies only to portable pneumatic tools manufactured by Dynabrade, Inc. in the USA. Lifetime
warranty applies only to the original tool owner; warranty is non-transferable.