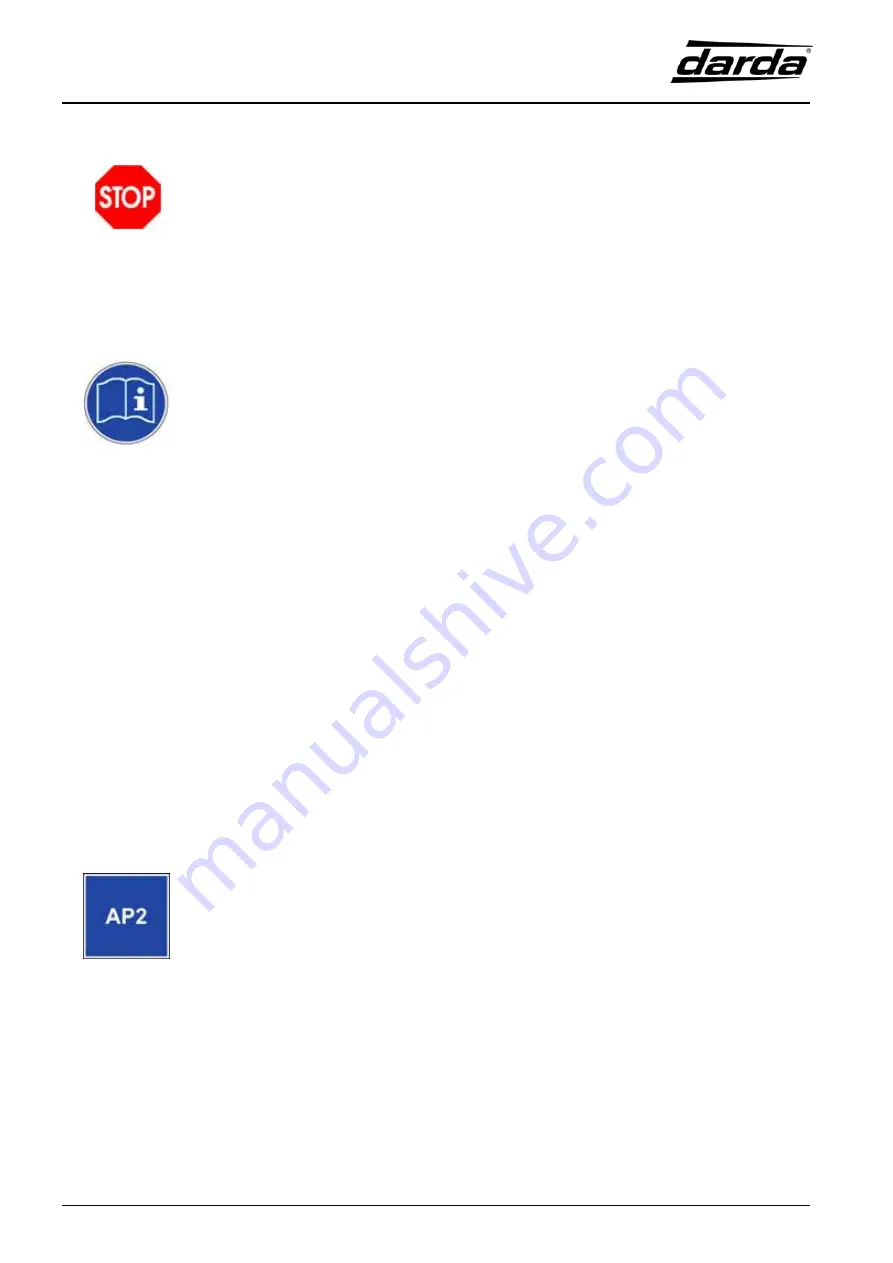
7 Maintenance / Cleaning
44
OM Hydraulic aggregate, Version 1.0 01/2013
7
Maintenance / Cleaning
We would like to draw your attention to the fact that the conversion and
hydraulic installation of the device may only be carried out by trained and
authorised personnel with a profound mechanical, hydraulic / pneumatic
and if necessary electric knowledge.
7.1 Maintenance
7.1.1 General
maintenance
Please refer to the appropriate manufacturer's documentation for mainte-
nance work for the engine/motor.
Maintenance every 4 operating hours
Check the hydraulic oil level.
Check all parts for damage and leaks.
Check whether the pressure relief valve trips at the max. operating pressure
stated in the technical data.
To do this, allow the cylinder on the stone and concrete splitter to extend all the
way or fully close the combination shears' insert.
Observe the pressure gauge on the device. If the pressure exceeds the max.
stated operating pressure, switch off the device and secure it from starting up
again. Replace the distributor block with pressure relief valve. The operator
must take appropriate organisational measures (operating procedures) for in-
stances when the safety equipment fails.
Maintenance every 40 operating hours
Check
all screw connections are tight.
whether the type plate, notices and labelling are legible.
whether there is still oil in the maintenance unit's oil vaporiser.
Maintenance when required
Check whether the silencer for the pneumatic motor
is iced over.
Interrupt work if necessary.
Oil and filter changes
We recommend changing the hydraulic oil and filters after around 2000 operating
hours or a maximum of 3 years. The oil should be at operating temperature for the
change. Wear appropriate protective clothing.
Please refer to the technical data for our authorised hydraulic oil.