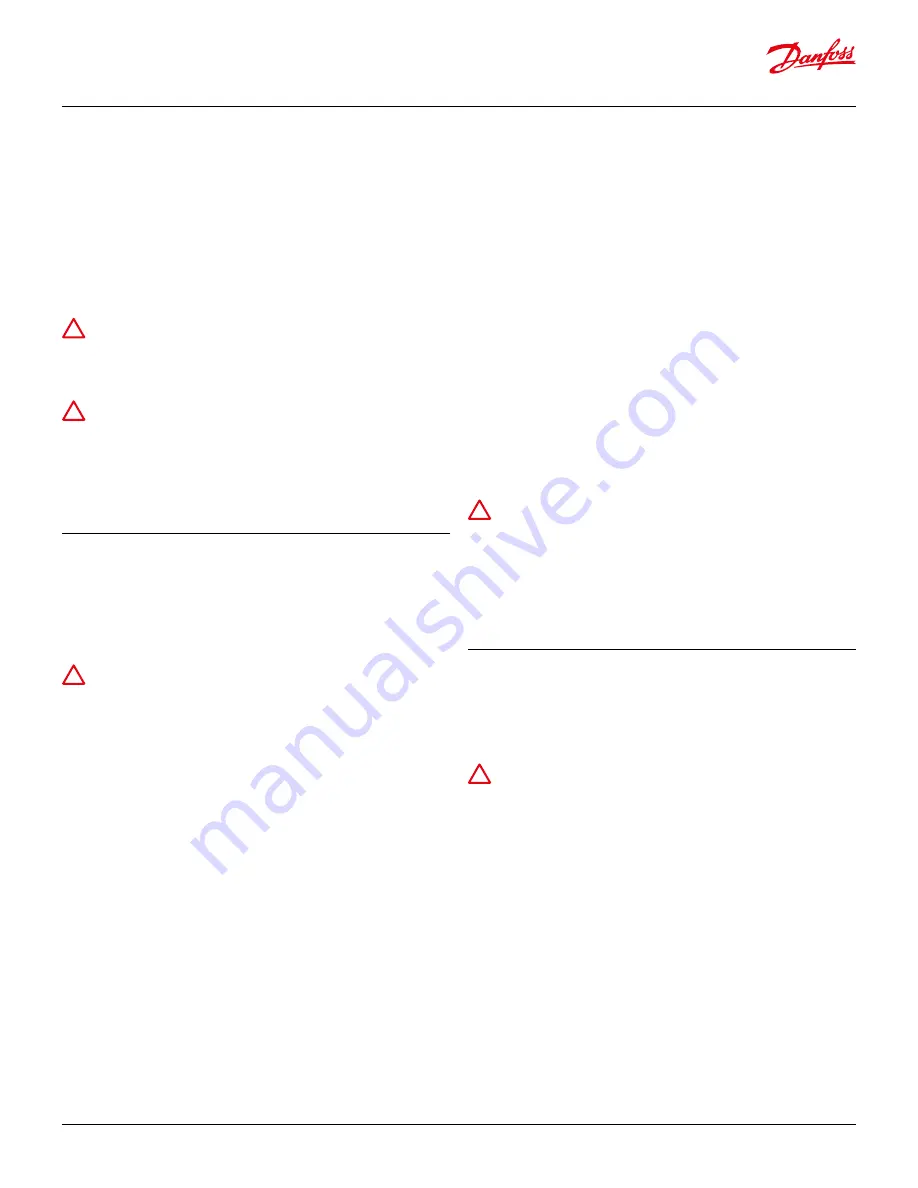
7 | PORTABLE COLL-O-CRIMP® Model T-480 Set up and operating instructions | 2022.10.
BC425482205281en-000101
Check-Out Procedure
Check for proper oil level in the power unit. The oil reservoirs in all power
units have been filled at the factory; however, if oil is required, refer to the
instruction sheet provided with each unit for proper hydraulic oil and filling
procedure. It is recommended that you follow the procedure below for your
specific model of crimper before making any hose assemblies.
For models T-480-TA and T-480-EP, the hose assembly will need to be
connected. Assemble coupler nipple into street elbow and 0-ring adapter
and assemble into press.
Assemble female half of coupler to hose assembly and thread adapter into
pump and connect hose assembly. Use pipe thread compound on all pipe
threads.
!
CAUTION
Throughout this procedure, check the power unit and all threaded connections for any leaks and tighten as necessary.
T-480-HP
!
NOTE
the following steps must be performed without tooling in the press.
1.
Turn vent/fill cap to “vent” position to vent reservoir.
2.
Open release valve and operate handle until the pusher has fully
extended.
3.
Release control valve allowing the pusher to retract.
4.
Repeat steps 2 and 3 approximately six times which will help purge air
from the system.
T-480-AH
1.
Connect air supply to the 1/4” NPT port on pump. Recommended
air inlet pressure is 60-100 psi. To ensure a long service life, it is
recommended that a filter, regulator, lubricator and gauge be installed
in the air line.
2.
Turn on air supply and adjust to recommended inlet pressure.
!
NOTE
the following steps must be performed without tooling in the press.
3.
Push down pressure valve allowing the pusher to fully extend.
4.
Release pressure valve allowing pusher to retract and purge any air
from the system.
5.
Repeat steps 3 and 4 until any air has been purged. When pusher
extends fully and retracts without hesitation, the air has been vented
from the system.
6.
Turn off air supply.
T-480-TA
1.
Connect air supply to the 1/4” NPT port on pump. Recommended
air inlet pressure is 40-150 psi. To ensure a long service life, it is
recommended that a filter, regulator, lubricator and gauge be installed
in the air line.
2.
Turn on air supply and adjust to recommended inlet pressure.
3.
Vent pump reservoir by opening vent screw.
!
NOTE
the following steps must be performed without tooling in the press.
4.
Push down pressure valve allowing the pusher to fully extend.
5.
Push down on release end of treadle allowing pusher to retract and
purge any air from the system.
6.
Repeat steps 4 and 5 until any air has been purged. When pusher
extends fully and retracts without hesitation, the air has been vented
from the system.
7.
Turn off air supply.
T-480-EP
1.
Connect power cord to suitable 15 amp, 120V grounded single phase
circuit.
2.
Open vent plug on reservoir.
3.
Turn pump switch located on side of shroud to “on” position.
!
NOTE
the following steps must be performed without tooling in the press.
4.
Press pendant switch and hold until pusher fully extends.
5.
Release pendant switch allowing pusher to retract.
6.
Repeat steps 4 and 5 until any air has been purged. When pusher
extends fully and retracts without hesitation, the air has been vented
from the system.
7.
Turn pump switch to “off” position.