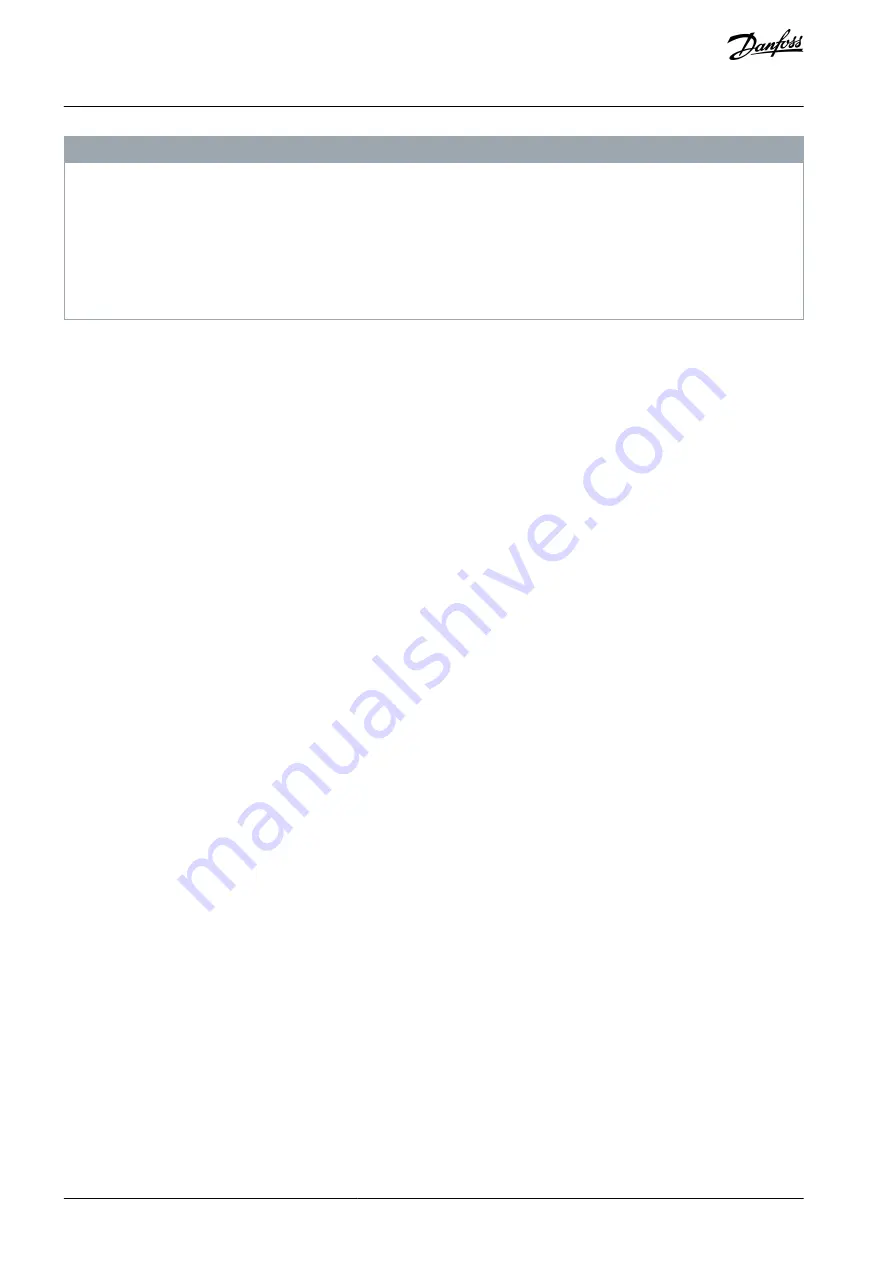
•
•
•
•
•
•
-
-
•
•
•
•
•
•
•
•
•
•
-
N O T I C E
CONNECTING/DISCONNECTING HYBRID CABLES
Never connect or disconnect the hybrid cable to or from the servo drives when the servo system is connected to mains or auxili-
ary supply, or when voltage is still present. Doing so damages the electronic circuitry. Ensure that the mains supply is disconnec-
ted and the required discharge time for the DC-link capacitors has elapsed before disconnecting or connecting the hybrid cables
to the PSM 510.
To avoid electrical shock, fully disconnect the PSM 510 from the mains and wait for the discharge time to elapse before dis-
connecting or connecting the hybrid cables or disconnecting cables from the PSM 510.
2.3 Safety Instructions and Precautions
Compliance with the safety instructions and precautions is necessary at all times.
Orderly and proper transport, storage, fitting, and installation, as well as careful operation and maintenance, are essential for the
trouble-free and safe operation of the servo system and its components.
Only suitably trained and qualified personnel may work on the servo system and its components or in its vicinity.
Only use accessories and spare parts approved by Danfoss.
Comply with the specified ambient conditions.
The information in this manual about the use of available components is provided solely by way of examples of applications
and suggestions.
The plant engineer or system engineer is personally responsible for checking the suitability of the supplied components and the
information provided in this manual for the specific application concerned:
For compliance with the safety regulations and standards relevant to the specific application.
For implementing the necessary measures, changes, and extensions.
Commissioning the servo system or its components is not allowed until it has been ascertained that the machine, system, or
plant in which they are installed conforms to the statutory provisions, safety regulations, and standards that apply to the appli-
cation in the country of use.
Operation is only allowed in compliance with the national EMC regulations for the application concerned.
Compliance with the limit values specified by national regulations is the responsibility of the producer of the plant, system, or
machine.
Compliance with the specifications, connection conditions, and installation conditions in this manual is mandatory.
The safety regulations and safety provisions of the country in which the equipment is used must be observed.
To protect the user against electrical shock and to protect the servo system against overload, protective grounding is obligatory
and must be performed in accordance with local and national regulations.
2.3.1 Operational Safety
Operational safety
Safety-related applications are only allowed if they are explicitly and unambiguously mentioned in this manual.
All applications that can cause hazards to people or damage to property are safety-related applications.
The stop functions implemented in the software of the PLC do not interrupt the mains supply to the Power Supply Module
(PSM 510). Therefore, they must not be used for electrical safety for the servo system.
The servo system can be brought to a stop by a software command or a zero speed setpoint, however DC voltage remains
present on the servo drives and/or mains voltage in the PSM 510. Also, when the system is stopped, it may start up again on its
own if the circuitry is defective or after the elimination of a temporary overload, a problem with the supply voltage, or a prob-
lem with the system. If personal safety considerations (for example, risk of personal injury caused by contact with moving ma-
chine parts after an unintended start) make it necessary to ensure that an unintended start cannot occur, these stop functions
are not sufficient. In this case, ensure that the servo system is detached from the mains network, and prevent unintended motor
starting, for example by using the Safe Torque Off function.
AQ262449648484en-000101 / 175R1135
22 | Danfoss A/S © 2020.08
Safety
VLT® Servo Drive System ISD 510/DSD 510
Operating Guide