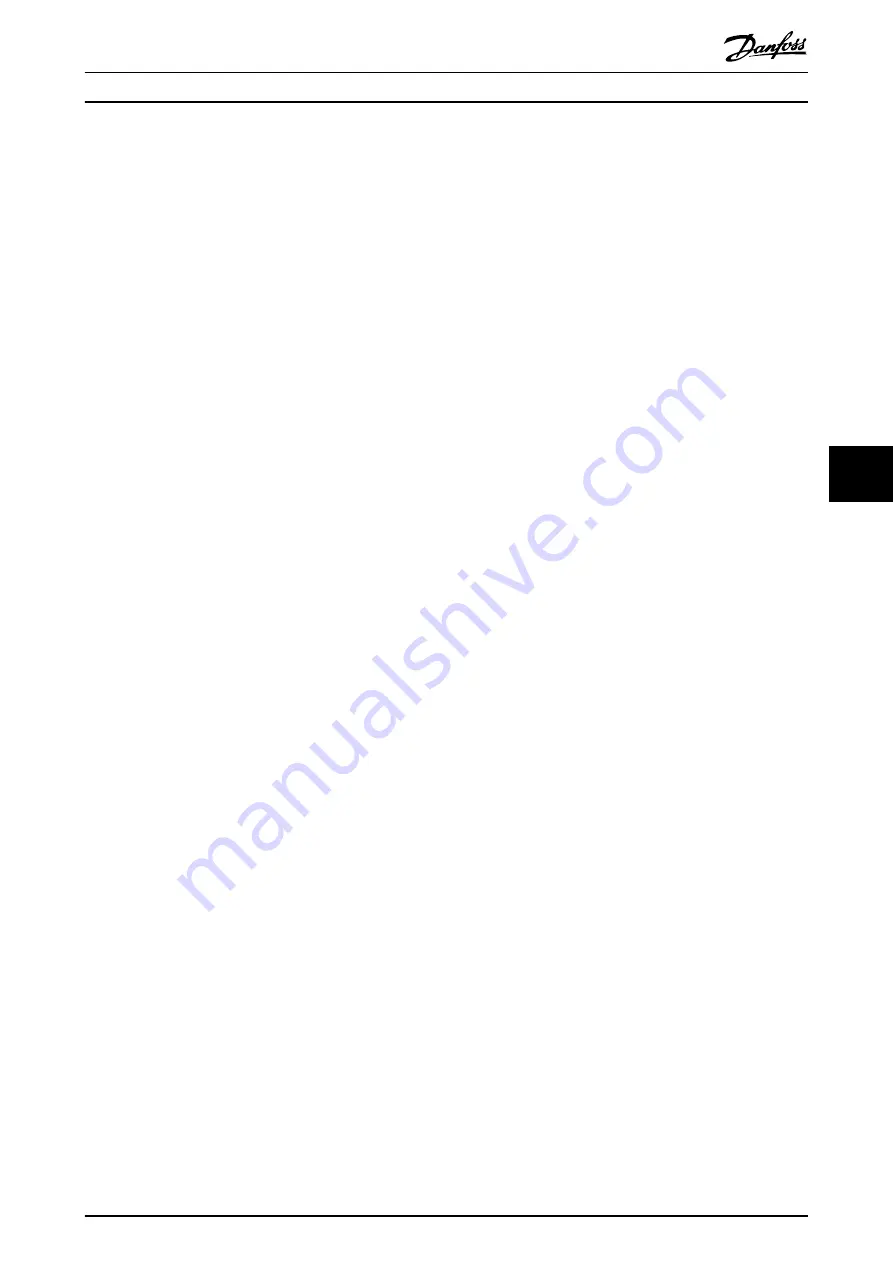
•
Increase
parameter 14-26 Trip Delay at Inverter
Fault
.
•
If the alarm/warning occurs during a power sag,
use kinetic back-up (
parameter 14-10 Mains
Failure
).
WARNING/ALARM 8, DC under voltage
If the DC-link voltage drops below the undervoltage limit,
the frequency converter checks if a 24 V DC back-up
supply is connected. If no 24 V DC back-up supply is
connected, the frequency converter trips after a fixed time
delay. The time delay varies with unit size.
Troubleshooting
•
Check that the supply voltage matches the
frequency converter voltage.
•
Perform an input voltage test.
•
Perform a soft charge circuit test.
WARNING/ALARM 9, Inverter overload
The frequency converter has run with more than 100%
overload for too long and is about to cut out. The counter
for electronic thermal inverter protection issues a warning
at 98% and trips at 100% with an alarm. The frequency
converter cannot be reset until the counter is below 90%.
Troubleshooting
•
Compare the output current shown on the LCP
with the frequency converter rated current.
•
Compare the output current shown on the LCP
with the measured motor current.
•
Show the thermal frequency converter load on
the LCP and monitor the value. When running
above the frequency converter continuous
current rating, the counter increases. When
running below the frequency converter
continuous current rating, the counter decreases.
WARNING/ALARM 10, Motor overload temperature
According to the electronic thermal protection (ETR), the
motor is too hot. Select whether the frequency converter
issues a warning or an alarm when the counter reaches
100% in
parameter 1-90 Motor Thermal Protection
. The fault
occurs when the motor runs with more than 100%
overload for too long.
Troubleshooting
•
Check for motor overheating.
•
Check if the motor is mechanically overloaded.
•
Check that the motor current set in
parameter 1-24 Motor Current
is correct.
•
Ensure that the motor data in
parameters
1–20
to
1–25
are set correctly.
•
If an external fan is in use, check that it is
selected in
parameter 1-91 Motor External Fan
.
•
Running AMA in
parameter 1-29 Automatic Motor
Adaptation (AMA)
tunes the frequency converter
to the motor more accurately and reduces
thermal loading.
WARNING/ALARM 11, Motor thermistor overtemp
Check whether the thermistor is disconnected. Select
whether the frequency converter issues a warning or an
alarm in
parameter 1-90 Motor Thermal Protection
.
Troubleshooting
•
Check for motor overheating.
•
Check if the motor is mechanically overloaded.
•
When using terminal 53 or 54, check that the
thermistor is connected correctly between either
terminal 53 or 54 (analog voltage input) and
terminal 50 (+10 V supply). Also check that the
terminal switch for 53 or 54 is set for voltage.
Check that
parameter 1-93 Thermistor Source
selects terminal 53 or 54.
•
When using terminal 18, 19, 31, 32, or 33 (digital
inputs), check that the thermistor is connected
correctly between the digital input terminal used
(digital input PNP only) and terminal 50. Select
the terminal to use in
parameter 1-93 Thermistor
Source
.
WARNING/ALARM 12, Torque limit
The torque has exceeded the value in
parameter 4-16 Torque Limit Motor Mode
or the value in
parameter 4-17 Torque Limit Generator Mode
.
Parameter 14-25 Trip Delay at Torque Limit
can change this
warning from a warning-only condition to a warning
followed by an alarm.
Troubleshooting
•
If the motor torque limit is exceeded during
ramp-up, extend the ramp-up time.
•
If the generator torque limit is exceeded during
ramp-down, extend the ramp-down time.
•
If torque limit occurs while running, increase the
torque limit. Make sure that the system can
operate safely at a higher torque.
•
Check the application for excessive current draw
on the motor.
WARNING/ALARM 13, Over current
The inverter peak current limit (approximately 200% of the
rated current) is exceeded. The warning lasts approximately
1.5 s, then the frequency converter trips and issues an
alarm. Shock loading or quick acceleration with high-inertia
loads can cause this fault. If the acceleration during ramp-
up is quick, the fault can also appear after kinetic back-up.
If extended mechanical brake control is selected, a trip can
be reset externally.
Maintenance, Diagnostics, a...
Operating Instructions
MG33AQ02
Danfoss A/S © 07/2015 All rights reserved.
41
7
7
Summary of Contents for VLT AutomationDrive FC 301
Page 2: ......