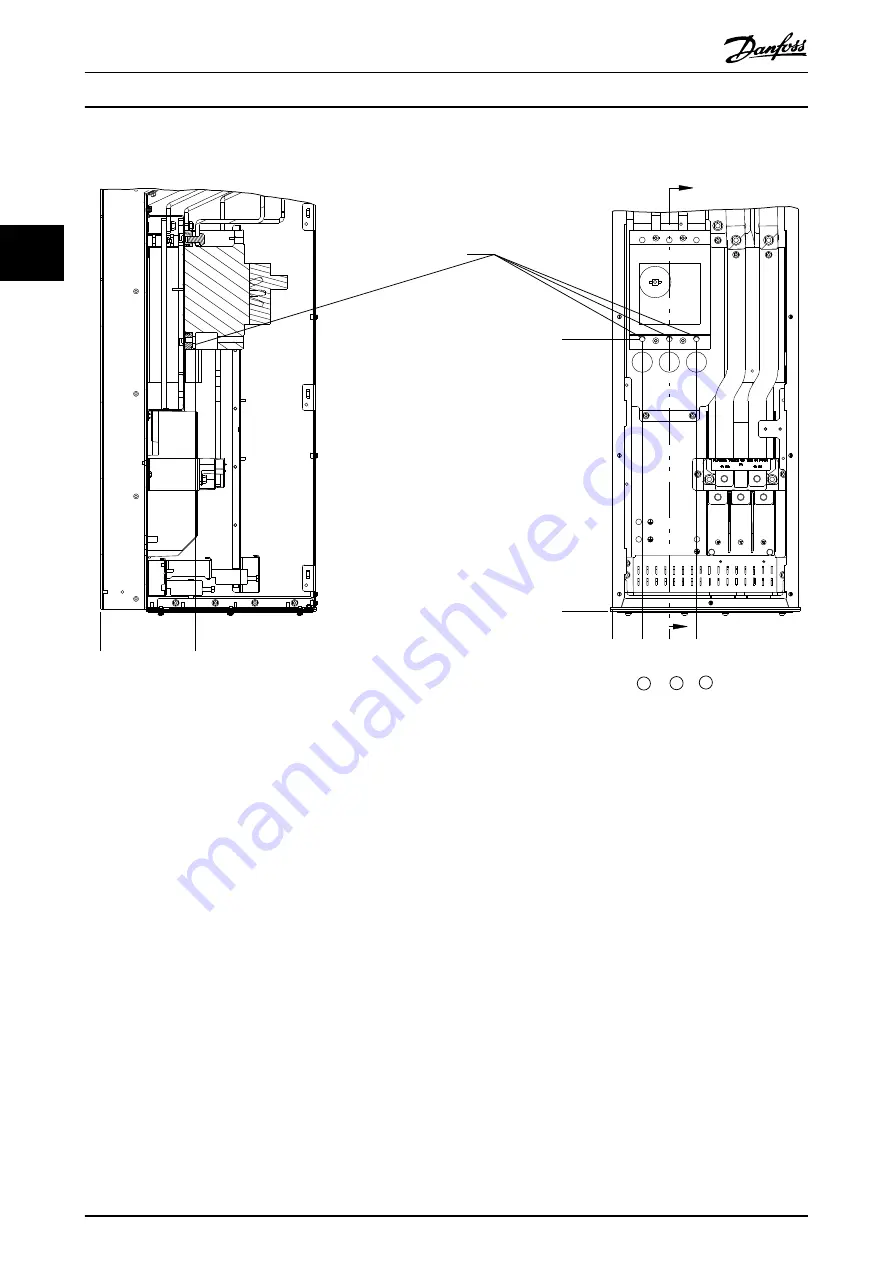
A
A
467
18.4
[
]
0
0.0
[
]
52 2.1[
]
0 0.0[
]
99 3.9[
]
145 5.7[
]
163 6.4[
]
0 0.0[
]
MAINS TERMINAL
SECTION A-A
MAINS TERMINALS
R
S
T
130BC541.10
Illustration 2.17 Terminal Locations, D6h with Circuit Breaker Option
Installation
VLT
®
AQUA Drive D-Frame
Operating Instructions
20
MG21A202 - VLT
®
is a registered Danfoss trademark
2
2