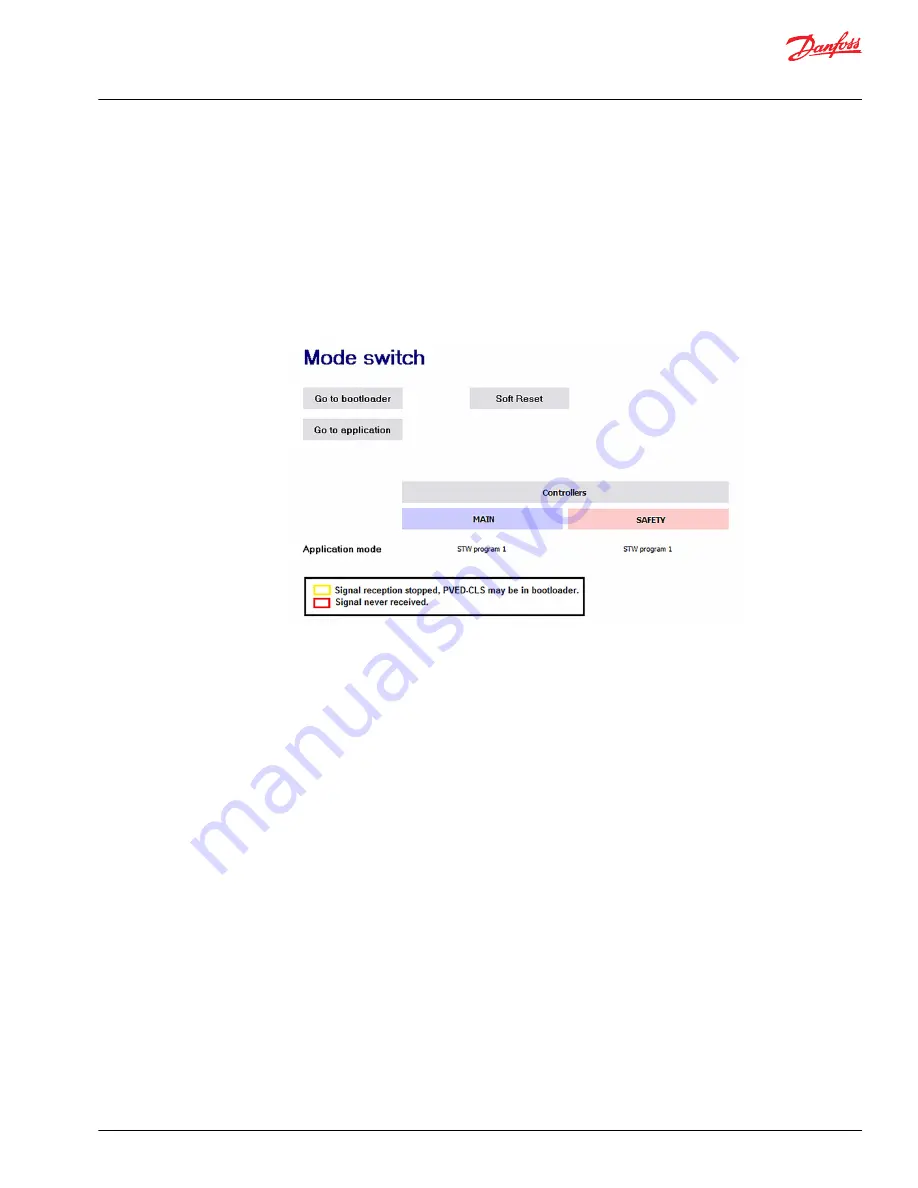
Resolving safe-state mode by soft reset
If the PVED-CLS is in safe-state mode, it is possible that a soft reset will resolve the underlying issue.
1. Open the Mode switch page.
The Mode Switch page is used to change between Bootloader and Application modes. When a
Config page is entered while in Normal View in the Service Tool, the PVED-CLS enters Bootloader
mode. To return to Application mode go to the Mode switch page and press the “Go to application”
button.
If the PVED-CLS is already in application mode (there is no red or yellow box around the Main and
Safety states) the "Go to application" button does not need to be pressed.
2. Press the "Soft Reset" button to reboot the PVED-CLS.
This may clear the Safe State if it was caused by exceeding a speed threshold or a temporarily missing
message.
If the PVED-CLS remains in safe-state mode, proceed to the
Resolving safe-state mode with SPN and FMI
codes
on page 42 section for further troubleshooting.
Application Guide
PVED-CLS startup guide
Troubleshooting
©
Danfoss | October 2018
AB285975085591en-000101 | 41