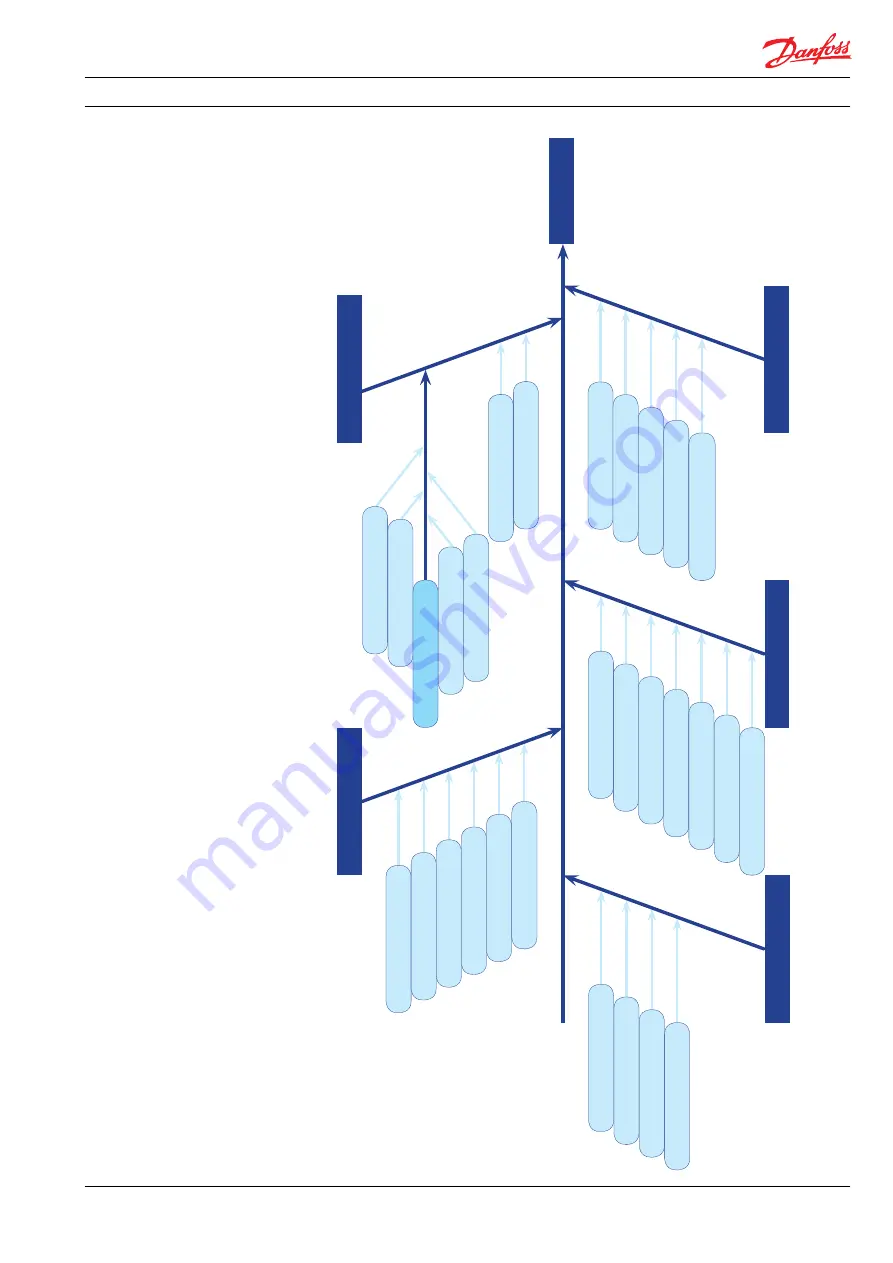
Guideline
Trouble shooting guide for PAH, PAHT, PAHT C , PAHT G pumps
61
180R9379 | AQ188686503004en-000801 | PAH 2-12.5 } 07.2022
Trouble shooting
fish bone chart
1.
N
o fl
ow
/p
re
ssu
re
3. H
ig
h t
or
qu
e o
n e
l. m
ot
or
4. N
oi
se f
ro
m p
um
p
5.
N
ois
e f
ro
m
ins
ta
lla
tio
n
2. R
edu
ce
d fl
ow
/p
re
ss
ur
e
1.
1 D
ry r
un
ni
ng
1.
2 P
ump
re
ve
rs
in
g
1.
3 N
o r
ot
at
io
n o
f e
le
ct
ri
c m
ot
or
1.
4 N
o r
ot
at
io
n o
f p
um
p
1.
5 A
xi
al f
or
ce o
n p
um
p s
ha
ft
1.
6 P
um
p da
mag
e
2.
1.
5 Pr
e-t
re
at
m
en
t
2.
1.
6 M
ain
filt
ra
tio
n
2.1
W
ea
r i
n p
um
p
(in
te
rnal
le
ak
ag
e)
2.
1.
7 T
yp
e o
f fl
ui
d
2.
1.
8 H
ig
h flui
d t
emp
era
tu
re
4.
1 A
ir
in
flui
d
4.
2 B
le
ed
ing
c
ond
it
ion
s of
pu
m
p
4.
3
M
in
/m
ax
n
ominal
inl
et
p
res
su
re
4.
4 P
um
p r
ev
er
si
ng
4.
5 H
ig
h r
ot
at
io
n s
pe
ed (
RP
M
)
4.
6 O
utl
et
p
res
sure
5.1
In
le
t/
ou
tle
t c
on
ne
ct
ion
s
(h
os
es
/p
ip
es
)
5.
2
Le
ngt
h/
di
m
en
si
on
s of
inl
et
/o
ut
le
t l
in
e
5.
3 Ho
se
st
iffn
es
s
5.
4
H
os
es
/p
ip
es
m
ou
nt
ed
di
re
ctl
y o
n f
ra
m
e
5.
5
V
ib
ra
ti
on d
am
pe
r u
nd
er t
he
el
ec
tric
m
ot
or
3.1
T
oo
h
igh
o
utl
et
p
re
ss
ure
from
pu
m
p
3.
3 C
on
st
an
t t
orq
ue
3.
4 W
at
er p
um
p d
am
ag
e
4.
7 S
of
t s
ta
rt
/s
to
p
PU
M
P F
AI
LE
D
3.
2 P
um
p s
ta
rt
s aga
in
st
p
re
ss
ure
2.
2 Lo
w
in
le
t p
re
ss
ure
2.
3 R
PM
Summary of Contents for PAH 2
Page 32: ... Danfoss DCS im 2022 07 AI073186502976en 001901 32 ...
Page 42: ... Danfoss DHS im 2022 02 180R9379 AQ188686503004en 000701 PAH 2 12 5 42 ...
Page 43: ...M a n u a l Electric Motors Motor Manual hoyermotors com ...
Page 47: ...47 180R9379 AQ188686503004en 000801 PAH 2 12 5 07 2022 ...
Page 79: ...79 180R9379 AQ188686503004en 000801 PAH 2 12 5 07 2022 ...
Page 80: ... Danfoss DCS im 2022 07 180R9379 AQ188686503004en 000801 PAH 2 12 5 80 ...