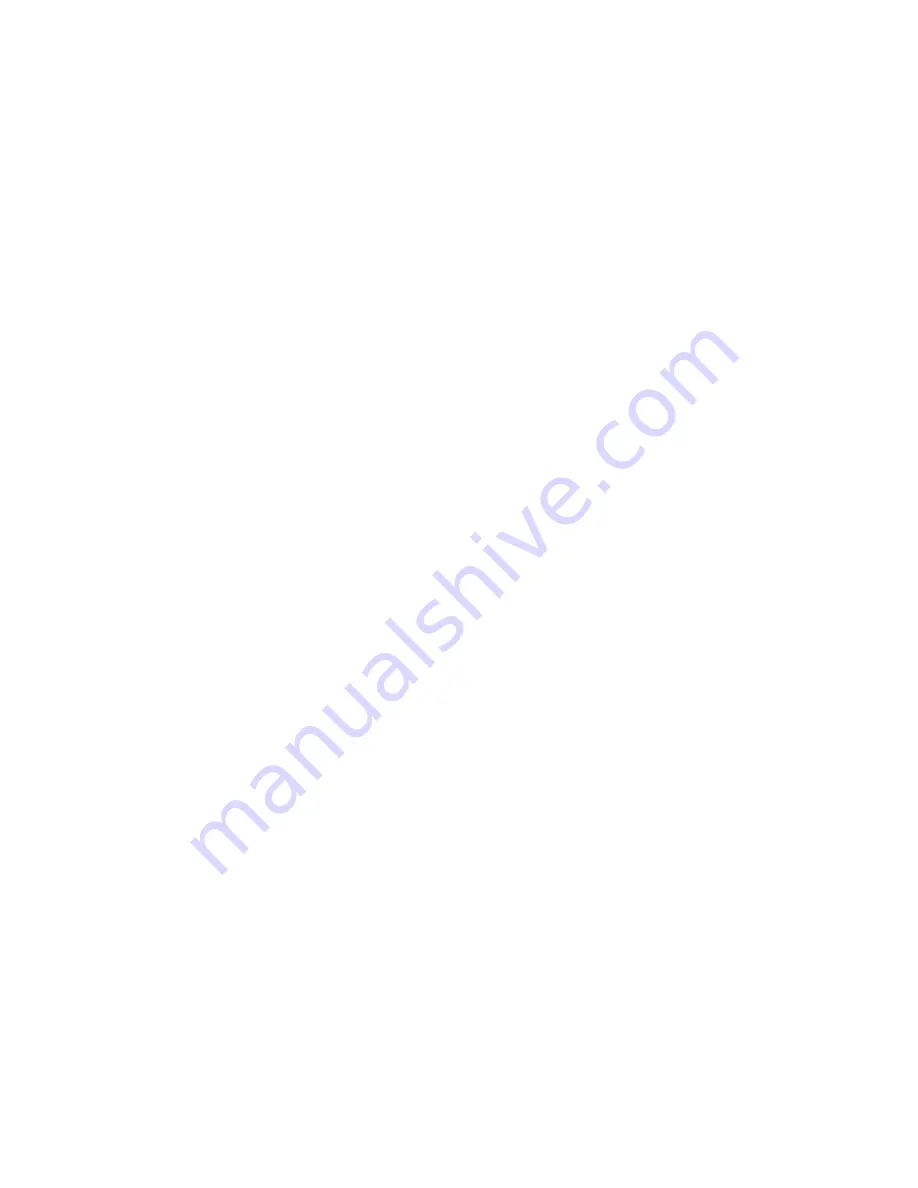
Safety technology: MCB14x Document No.:
MG34Y104
Rev.: 06 23 October 2012 Page 4 of 25
1.
Declaration of Conformity
The manufacturer, DINA Elektronik GmbH Wolfschlugen, hereby declares that the product MCB14x is compliant
with the provisions of the following directives:
According to the Machinery Directive 2006/42/EC, Annex II 1A
In accordance with Annex I. 1. 5. 1 of the Machinery Directive, the protective aims of the Low Voltage Directive are
fulfilled.
Directive 2004/108/EC: "EMC Directive"
GS-ET-20: Additional requirements for the testing and certification of safety switch devices
DIN EN 60947-5-1: Control units and switching elements; Electromechanical control units
DIN EN 62061: Functional safety of safety-related electrical, electronic and programmable electronic control
systems
EN 60204-1:2006 + A1:2009: Electrical equipment of machines
EN 50178:1997:
Electronic equipment for use in power installations
The device meets the requirements of the test specifications stated below in Chapter 1.1.
1.1. Test specifications
Test according to EN 13849-1 with validation according to EN 13849-2 for PLe/Cat 4 in dual channel applications
for frequency converters with and without STO
Test according to EN 13849-1 with validation according to EN 13849-2 for PLd/Cat 3 in dual channel applications
for frequency converters with STO without contact-based energy isolation
Test according to EN 13849-1 with validation according to EN 13849-2 for PLc/Cat 1 in single channel applications
for frequency converters with and without STO
EC type test certification:
MCB140
ET 12037
MCB141
ET 12082
1.2. Intended Use
The intended use of the monitoring module MCB14x is to protect individuals in the hazardous area of machinery
and equipment by:
-
Monitoring emergency stop devices
-
Monitoring the drive speed
-
Monitoring existing protective interlocks
-
Monitoring the functionality of existing drive energy isolators
Based on the rated input information, various control signals to operate a drive inverter are generated in such a
way as to fulfil the following safety operations:
-
Status-based drive enable (STO according to EN IEC 61800-5-2)
-
Tripping of ramp signal for controlled drive shutdown (SS1 according to EN IEC 61800-5-2)
-
Speed-dependent release control of existing protective devices (SLS according to EN IEC 61800-5-2, SMS
Safe Maximum Speed and SSM according to EN IEC 61800-5-2)
-
Immediate tripping of drive energy isolator in the event of hazards and faults
(STO according to EN IEC 61800-5-2)
The user must ensure that a restart interlock function is implemented in the control system.
1.3. Important note
The product described here was developed in order to take over the various safety-related operations as part of an
overall system.
The overall system is made up of sensors, evaluation and reporting units and concepts for safe tripping. It is the
responsibility of the manufacturer of a system or machine to ensure its correct overall functionality.
The manufacturer of the system/machine is obliged to check and verify the effectiveness of the implemented safety
concept within the overall system.
This verification must be performed again after any modification to the safety concept or safety parameters.
The company DINA Elektronik GmbH is unable to guarantee all of the features of an overall system that was not
designed by DINA Elektronik GmbH.
In addition, DINA Elektronik GmbH shall not assume any liability for recommendations specified or implied by the
following description. No new guarantee, warranty or liability claims that go over and above the General Terms and
Conditions of Delivery of Dina Elektronik GmbH can be derived on the basis of the following description.