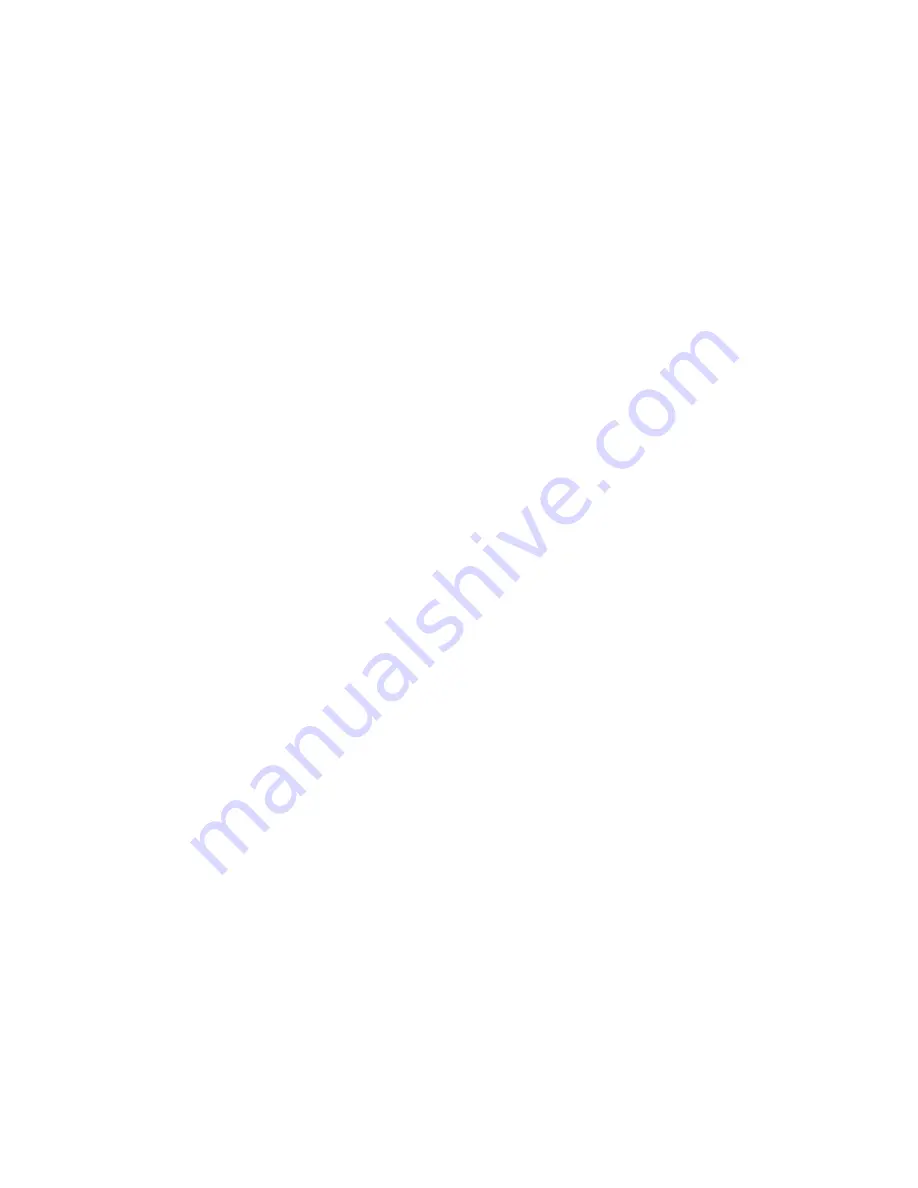
9
Danfoss
FT1390 Crimp Machine Operator´s Manual October 2022
Maintenance
Maintenance Intervals
Die Cage Lubrication
Every 50 crimps
Relube sliding surfaces of dies
Every 500 crimps
Remove old grease and relube
Every 1000 crimps
Die cage maintenance
Crimp Ring Maintenance
Every 500 crimps
Remove old grease and relube
Every 2000 crimps
Remove old grease, inspect for
wear or damage and relube if OK.
Cylinder Plate Bushing Maintenance
Every 2000 crimps
Remove old grease, inspect for
wear or damage and relube if OK.
Use PTFE lubricant
(Part Number: T-400-G 1.5 oz tube, FF91455 16 oz. can).
Maintenance Procedures
Machine Maintenance Procedure
1. Sliding surfaces must be kept free of dirt and other abrasive
materials.
2. All exposed black metal surfaces should be coated
occasionally with a light film of oil to prevent corrosion.
3. Periodically check the oil level in the fluid reservoir of the
hydraulic power unit. Maintain the oil level according to the
indicator on top of the reservoir. Add ENERPAC hydraulic oil
as needed.
Note:
Completely retract the crimp ring when checking the
oil level.
Maintenance Procedure
Die Cage Maintenance Procedures
1. Lubricate the die cage. For maximum service, die surfaces
require lubrication at 50-crimp intervals with PTFE lubricant.
Periodically remove PTFE residue that has built up on the
sides of the dies and in the crimp ring during the crimping
process. Do not allow contaminated PTFE to come into
contact with the dies. (This can cause dies to stick to the
crimp insert.) PTFE residue becomes contaminated with
metal and plating chips and airborne contaminants, which
can cause premature wear of the dies and crimp ring.
2. Die cage maintenance should be performed at 1000-crimp
intervals or every six months, which ever occurs first. Die
cages should be free of grease and debris and inspected for
worn or damaged components.
a. The sliding surface of the dies should appear smooth
with no apparent galling. Galled dies must be replaced.
Individual dies in a cage can be replaced without
replacing all dies.
b. Replace springs that show any sign of damage or
collapse such as those which are shorter than the other
springs.
c. The spring plate should appear smooth with no
apparent galling. Galled spring plates must be replaced.
d. Inspect remaining components, and replace those that
are badly worn.
Reassemble components, and liberally apply PTFE to the die
surface which slides along the spring plate. Torque the die
cage bolts to 50 in.-lbs.
Ensure that all dies slide in and out freely.
Warning:
Removal of the cylinder and hydraulic power unit
from a crimp machine that is not secured to the floor will
cause reduced stability.
Summary of Contents for FT1390
Page 1: ...Crimp machine operator s manual Danfoss FT1390 crimp machine...
Page 19: ......