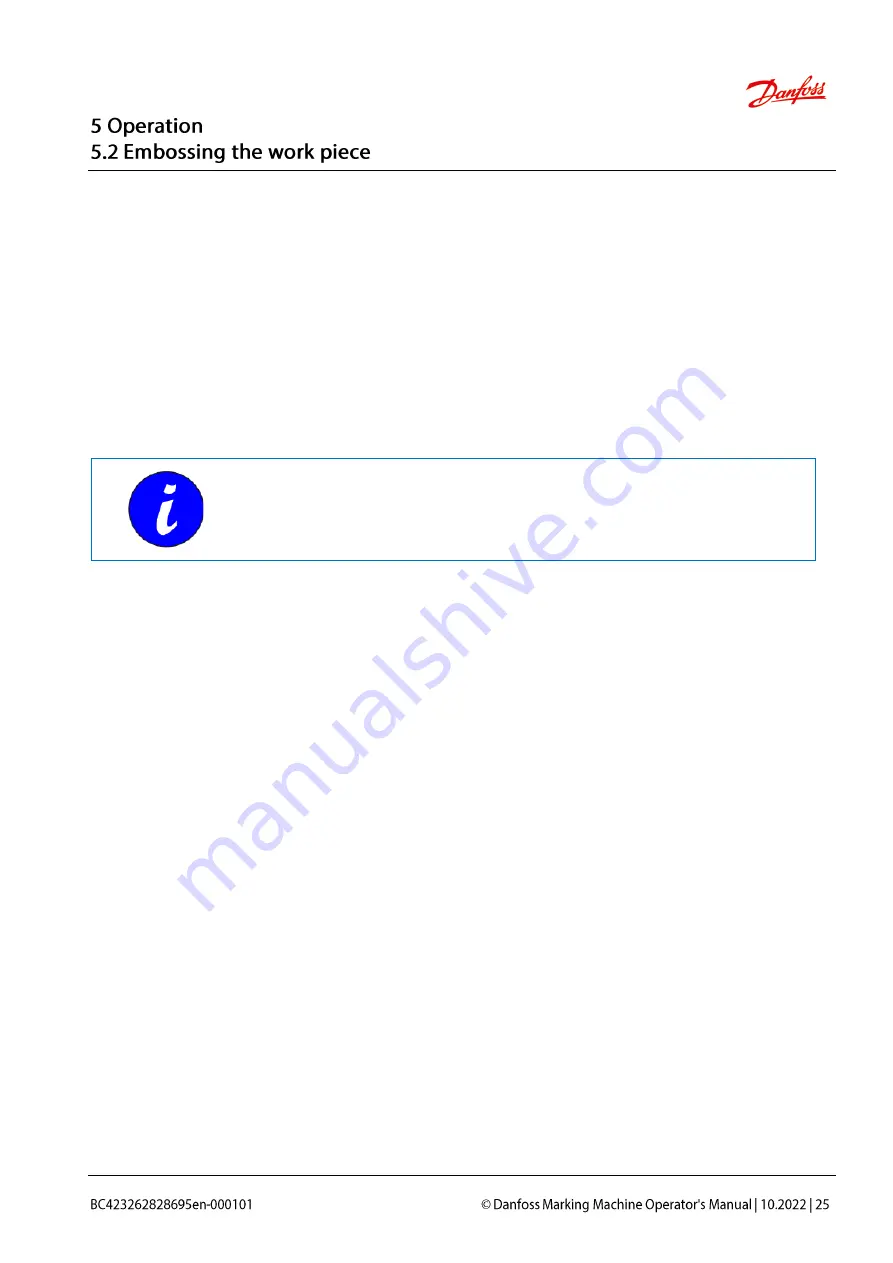
5.
Turn the hand wheel (5) until the steel types (4) are in contact
with the work piece.
6.
Remove the workpiece from the machine.
7.
Turn the hand wheel (5) counter-clockwise to the stop by a half-
turn.
8.
Position the work piece on the bearing blocks (3).
9.
Use the operating lever (1).
10. Remove the workpiece from the machine.
11. Check the forming dimension after the first forming process.
Correct the embossing depth by turning the hand wheel.
The set value may be read on the scale of the vertical guide to be
re-used for identical work pieces later.
Summary of Contents for ET6300
Page 1: ......
Page 3: ......
Page 38: ...9 2 Spare parts list...
Page 40: ...9 4 Maintenance log Slide bearing Remark Date Signature...
Page 42: ......
Page 43: ......
Page 44: ......