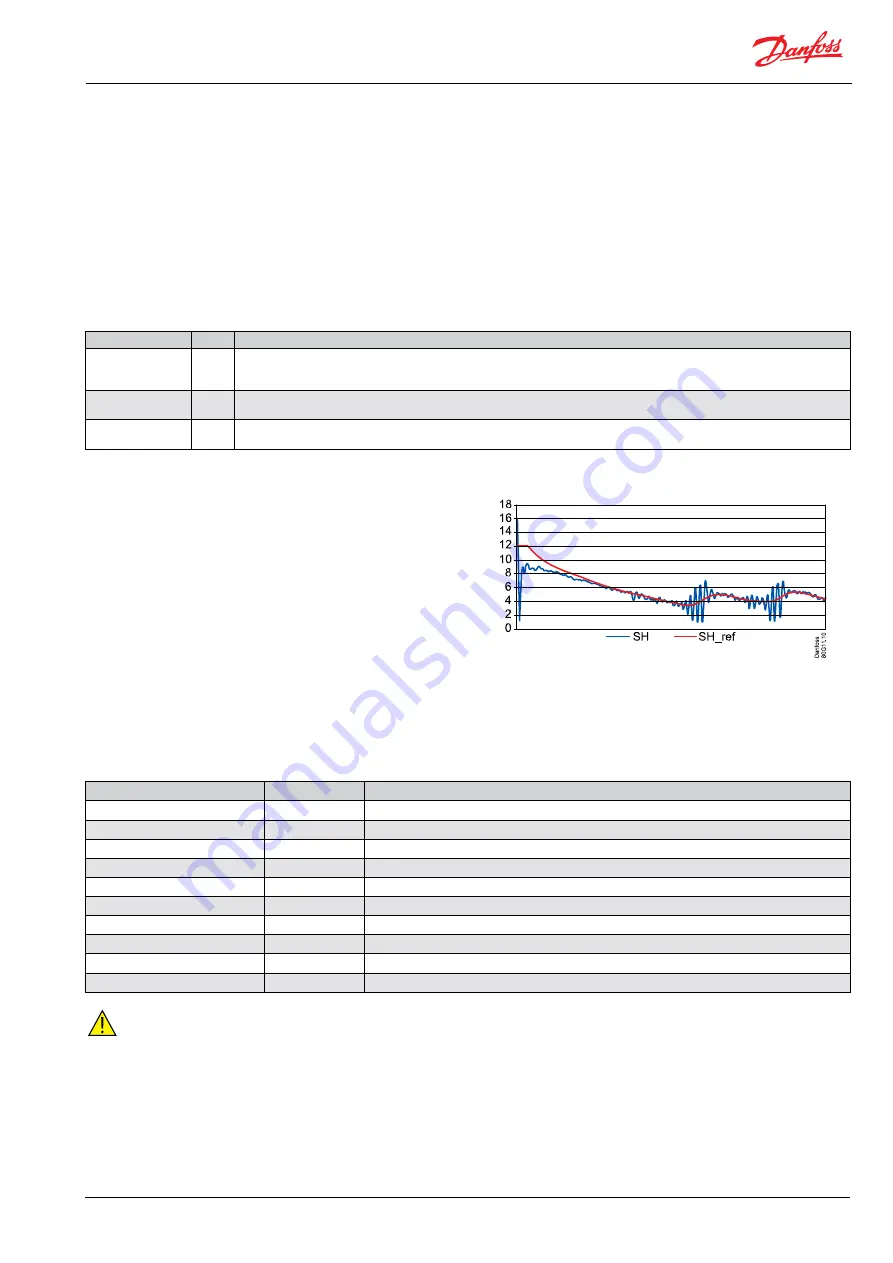
© Danfoss A/S (AC-MCI / sw), 2014-11
DKRCC.PS.RQ0.B7.02 /520H8832
9
Manual
Superheat Controller EIM 336
4.
Using external sensor values
In some applications, the suction pressure and/or the refrigerant
temperature on the evaporator outlet, is measured by a system
controller. This is often the case if the suction pressure is used to
trigger low temperature/pressure alarms by the systems main
controller. In these cases the sensors can be omitted from the EIM
336, and the sensor values can be received via modbus instead.
This requires that the systems main controller continuously
transmits these values to the EIM 336. If no new sensor value is
received within 5 seconds of the last transmission, the sensor will
revert to using the physical sensors.
The suction gas temperature S2 and the evaporator pressure
Pe can be set by writing to the registers “ext S2 Temp” and “ext
EvapPress P0” respectively.
Note
that the external evaporator pressure is received in millibar
so 8.4 bar absolute must be sent as 8400.
It is possible to set the S4 temperature as an external sensor value
also, but since this sensor is not used in the superheat regulation,
this has little practical use.
Related parameters:
Symbolic name
PNU
Description
ext EvapPress P0
2643
External evaporator pressure. This value can be used instead of a sensor.
This register must be written at least every 5 second, otherwise the sensor value will be used.
The entered value is in millibar
ext S2 temp
2644
External S2. This value can be used instead of a sensor.
This register must be written at least every 5 second, otherwise the sensor value will be used.
ext S4 air temp.
2646
External S4. This value can be used instead of a sensor. This register must be written at least every 5 second, otherwise the
sensor value will be used.
5.
Configuring the superheat control
The superheat control algorithm will attempt to regulate the
superheat down to the lowest stable value between the minimum
superheat setting, “n10 Min SH” and the maximum superheat
setting, “n09 Max SH”. If a fixed superheat reference is desired
instead, the “n10 Min SH” and “n09 Max SH” can both be set to
the desired reference value. This will disable the minimum stable
superheat search algorithm and the controller will instead regulate
the superheat according to this reference.
The time constant for the superheat control can be changed by
setting “Tn SH”.
The alpha value is the design time constant and should be in
reasonable proximity to the time constant of the evaporator. A
large alpha means a slow reaction, a small alpha means a fast
reaction.
If the superheat drops below “n22 SH close”, the controller will
close the valve faster to avoid the risk of liquid in the compressors
suction line.
Symbolic name
PNU
Description
n09 Max SH
3015
Maximum superheat reference setting.
n10 Min SH
3021
Minimum superheat reference setting.
n20 Kp T0
3025
Pressure feedback gain.
n22 SH close
3027
Superheat close level. If the superheat goes below this value, the valve will close faster.
--- Tn SH
3103
Integration time for superheat control
--- Alpha
3111
Design time constant. A large alpha means a slow response, a small alpha mean a fast response.
--- Max SH shdw
64301
Copy of 3015. If it is required to write n09 frequently, this should be used instead.
--- Min SH shdw
64302
Copy of 3021. If it is required to write n10 frequently, this should be used instead.
--- Tn SH shdw
64303
Copy of 3103. If it is required to write TnSH frequently, this should be used instead.
--- Alpha shdw
64304
Copy of 3111. If it is required to write alpha frequently, this should be used instead.
Note:
Main Switch r12 should be ON to start the regulation. This can also be
accomplished with the external hardware mainswitch.
See appendix 1 for details.