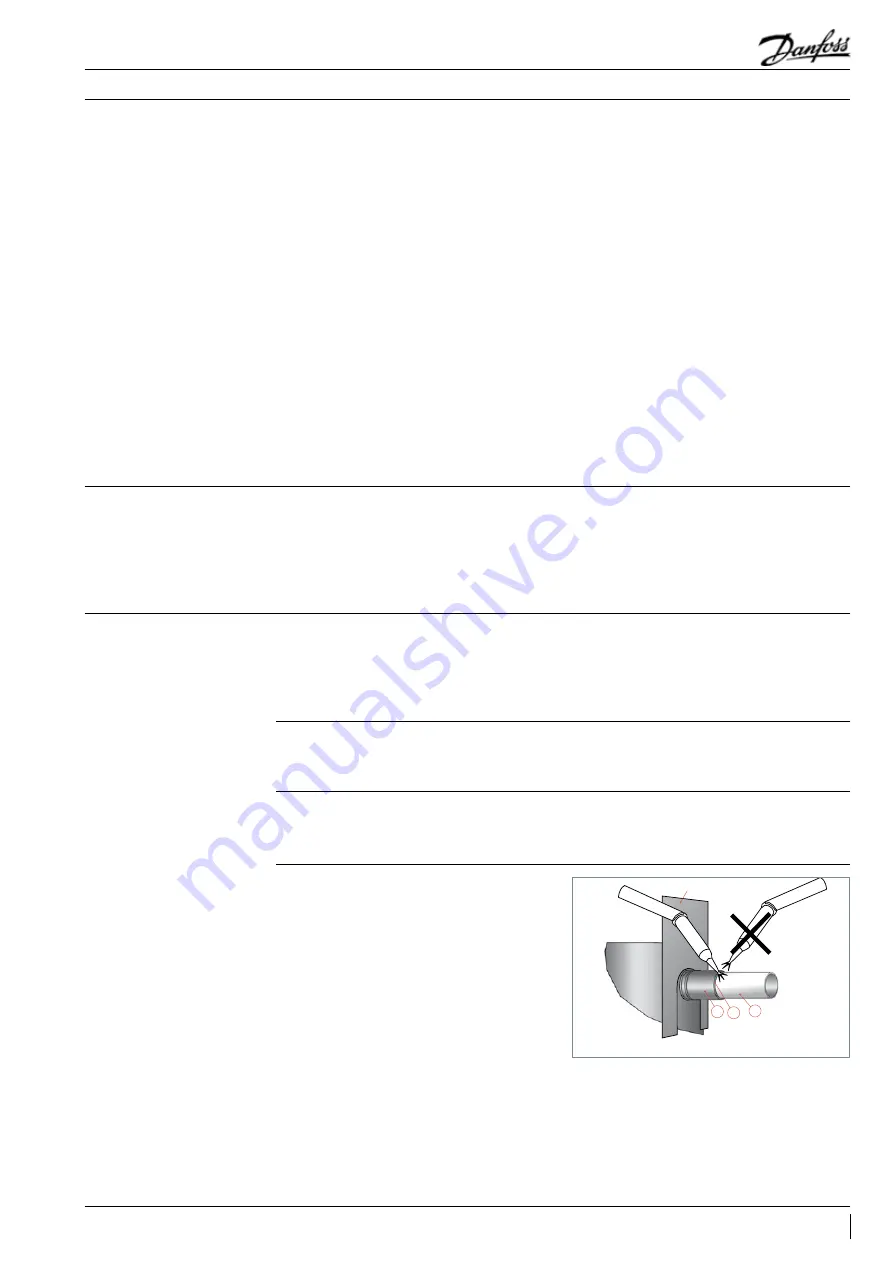
Installation
System cleanliness
The refrigerant compression system, regardless
of the type of compressor used, will only provide
high efficiency and good reliability, along with a
long operating life, if the system contains solely
the refrigerant and oil it was designed for. Any
other substances within the system will not
improve performance and, in most cases, will be
highly detrimental to system operations.
The presence of non-condensable substances
and system contaminants such as metal
shavings, solder and flux, have a negative
impact on compressor service life. Many of these
contaminants are small enough to pass through
a mesh screen and can cause considerable
damage within a bearing assembly. The use of
highly hygroscopic polyol ester oil in R410A
compressors requires that the oil be exposed
to the atmosphere as little as possible. System
contamination is one of main factors affecting
equipment reliability and compressor service
life. It is important therefore to take system
cleanliness into account when assembling a
refrigeration system.
During the manufacturing process, circuit
contamination may be caused by:
• Brazing and welding oxides,
• Filings and particles from the removal of burrs
in pipe-work,
• Brazing flux,
• Moisture and air.
Consequently, when building equipment
and assemblies, the precautions listed in the
following paragraphs must be taken.
Tubing
Only use clean and dehydrated refrigeration
grade copper tubing. Tube-cutting must be
carried out so as not to deform the tubing
roundness and to ensure that no foreign debris
remains within the tubing. Only refrigerant grade
fittings should be used and these must be of
both a design and size to allow for a minimum
pressure drop through the completed assembly.
Follow the brazing instructions on next pages.
Never drill holes into parts of the pipe-work
where fi lings and particles can not be removed.
Brazing and soldering
When brazing copper-to-copper connections,
the use of copper/phosphorus brazing alloy
containing 5% silver or more with a melting
temperature of below 800°C is recommended. No
flux is required during brazing.
Copper to copper
connections
Do not bend the compressor discharge or suction
lines or force system piping into the compressor
connections, because this will increase
stresses that are a potential cause of failure.
Recommended brazing procedures and material,
are described section “Compressor connection”.
These operations must be performed by a
qualified personnel in compliance with all
pertinent practices and safety procedures.
Dissimilar metals
connection
When manipulating dissimilar metals such as
copper and brass or steel, the use of silver solder
(5% or more) and anti-oxidant flux is necessary.
Please contact Danrfoss Technical support for any
deviation from this guidelines.
Compressor connection
When brazing the compressor fittings, do not
overheat the compressor shell, which could
severely damage certain internal components
due to excessive heating. Use of a heat shield
and/or a heat-absorbent compound is highly
recommended. Due to the relatively sizable
tubing and fitting diameters a double-tipped
torch using acetylene is recommended for
brazing operation on CH scroll compressors.
heat shield
C B
A
35
FRCC.PC.026.A4.02
Application Guidelines