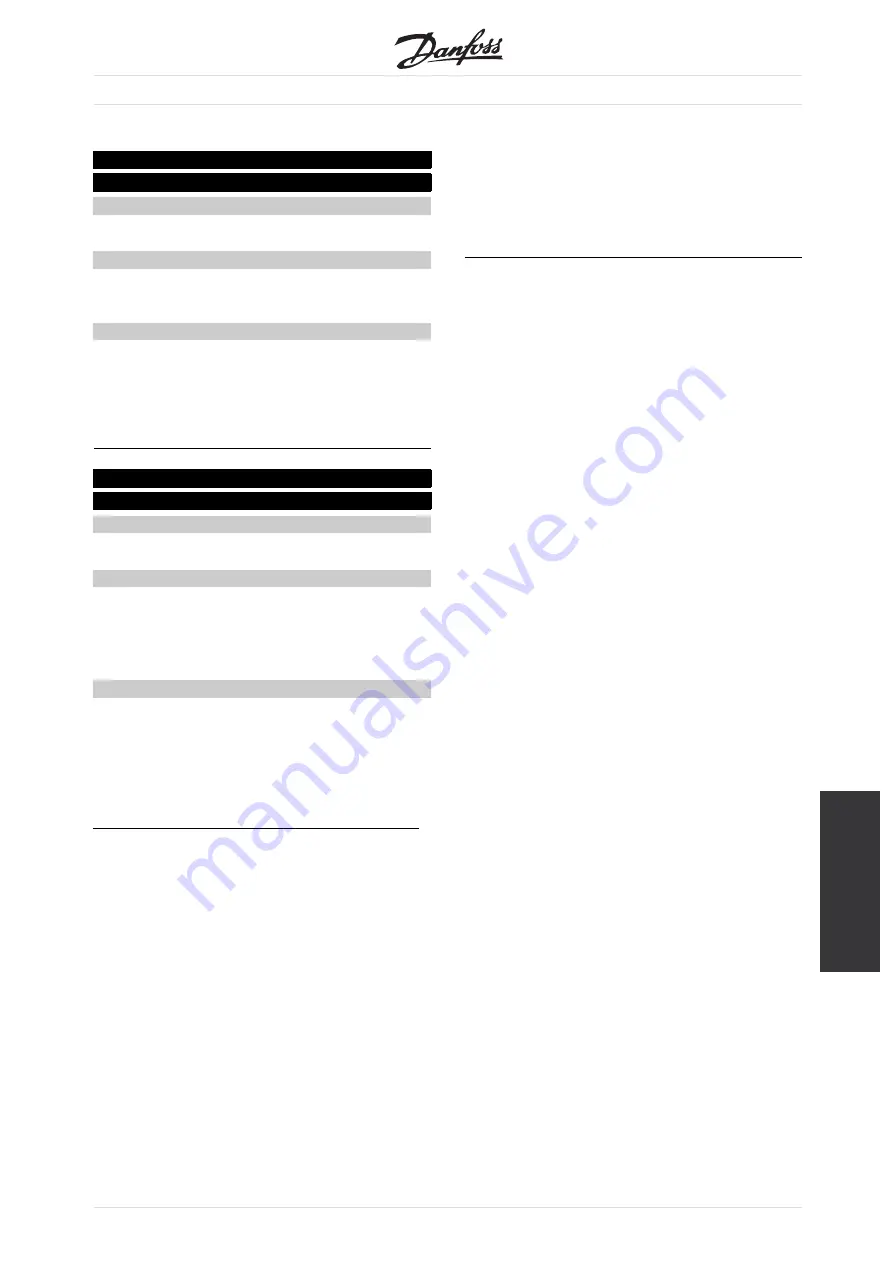
Cascade Controller Option
System Optimisation
■
Optimization of the process regulator
Quick Menu 038 Par. 423 PID proportional gain
(PID PROP. GAIN)
Value:
0.00 - 10.00
✭
0.01
Function:
Determines how fast the system responds
to a change in feedback.
Description of choice:
Quick regulation is obtained by a high gain, but
if the gain is too high, the process may become
unstable. See
Optimization of the Process Regulator
for information on proper adjustment.
Quick Menu 039 Par. 424 PID integration time
(PID INTEGR.TIME)
Value:
0.01 - 9999.00 sec. (OFF)
✭
OFF
Function:
The integrator adds the error signal over time and
uses this to correct the speed of the drive. The
integration time is the time needed by the integrator
to have the same effect as the proportional gain.
Description of choice:
Fast regulation is obtained by setting a short
integration time. However, if this time is too short,
the process will overcorrect and become unstable.
See
Optimization of the Process Regulator
for
information on proper adjustment.
Procedure for Optimization of the Process Regulator
The process regulator is set by Quick Menu items
38 and 39 (parameters 423 and 424). To optimize
the proportional gain and integration time, in most
processes, this can be done as follows:
1. Start the motor.
2. Set parameter 423,
PID Proportional Gain
, to 0.3
and increase it until the feedback signal becomes
unstable. Then reduce the value until the feedback
signal has stabilized. Now lower the proportional
gain by about half (40% to 60%).
3. Set parameter 424,
PID Integration Time
, to 20
seconds and reduce the value until the feedback
signal becomes unstable. Increase the integration
time until the feedback signal stabilizes. Now
increase the integration time from 15% to 50%.
Starting and stopping the drive will produce the
necessary error signal in the process to set the PID.
PID equation:
The VLT PID controller operates in accordance
to the following equation:
PID out = P[e(t) + 1/ l f e(t) dt] + D e(t)/dt
MG.60.I3.02 - VLT is a registered Danfoss trademark
53